Новости
Полное руководство по выбору станка для лазерной резки листового металла: Эффективность, Точность, и универсальность
1. Введение в станки для лазерной резки листового металла
Laser cutting machines for sheet metal have revolutionized the manufacturing and fabrication industries. They use a highly focused laser beam to cut, melt, or vaporize metal sheets, allowing for intricate designs, точные разрезы, and rapid production. These machines are crucial in various sectors, including automotive, аэрокосмический, и электроника, where the demand for precision and efficiency is paramount.
This guide explores the ins and outs of laser cutting machines for sheet metal, covering their working principles, преимущества, типы, Приложения, and key considerations for choosing the right machine. By understanding these aspects, manufacturers can optimize their production processes and achieve superior results.
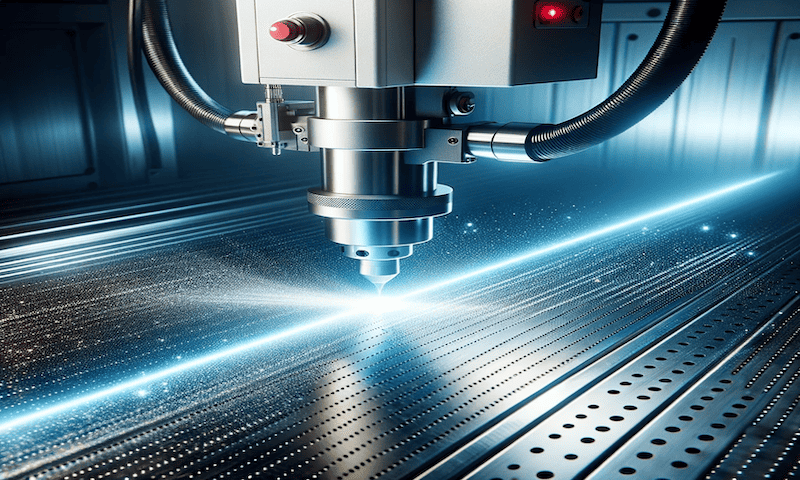
2. How Laser Cutting Machines for Sheet Metal Work
Laser cutting machines for sheet metal use concentrated beams of light to heat the material to a point where it melts or vaporizes. The process involves several key components and steps:
- Components of a Laser Cutting Machine
– Лазерный источник: The heart of the machine, where the laser beam is generated. Depending on the type of laser (fiber or CO2), the laser source uses different methods to amplify light.
– Режущая голова: This part directs the laser beam onto the sheet metal, focusing the energy to a small point for precise cutting.
– Контроллер ЧПУ: The CNC system guides the cutting head according to pre-programmed paths, ensuring accuracy and repeatability.
– Assist Gas Delivery System: Gases like nitrogen or oxygen are used to assist the cutting process by blowing away molten material, preventing oxidation and improving edge quality.
– Система охлаждения: This system prevents the laser source and other components from overheating, ensuring continuous operation without compromising performance.
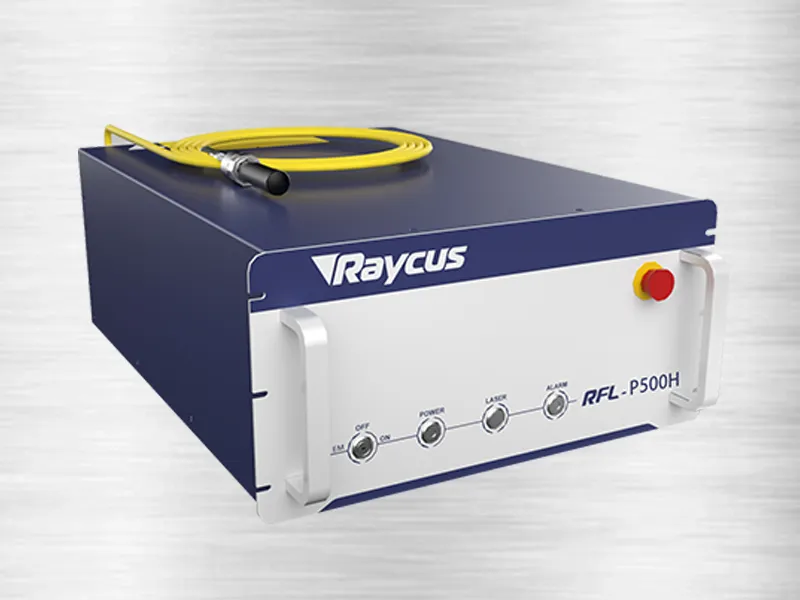
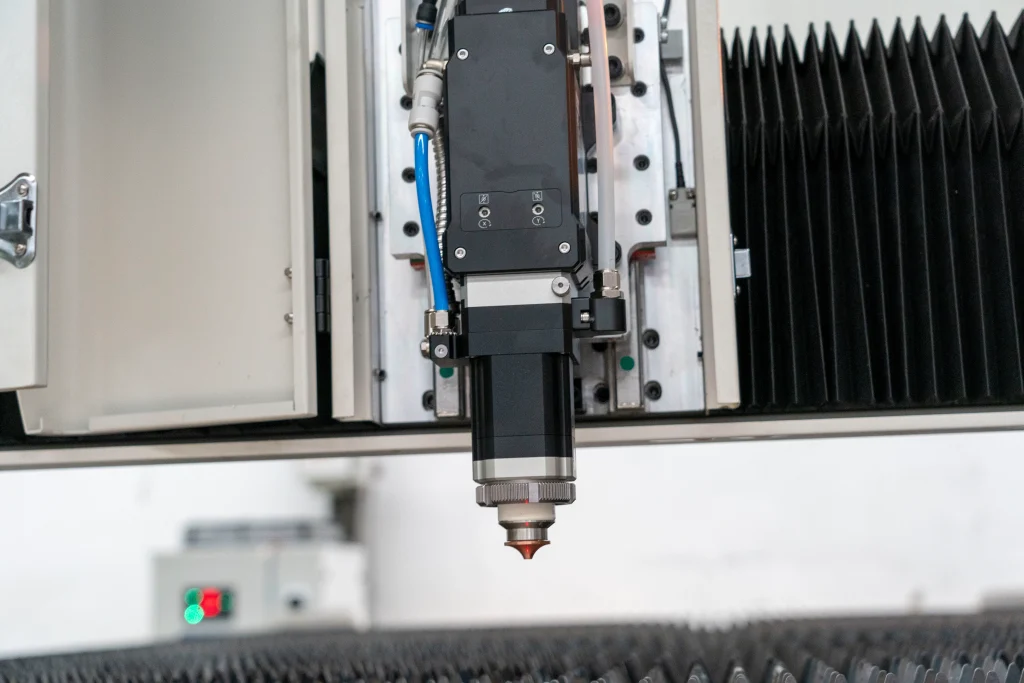
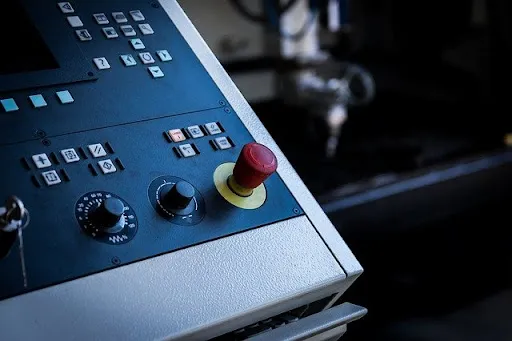
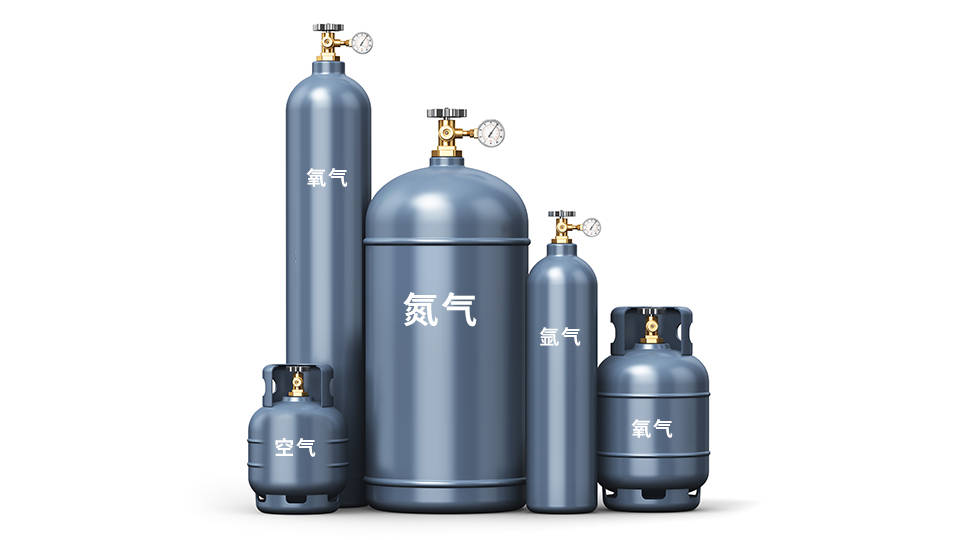
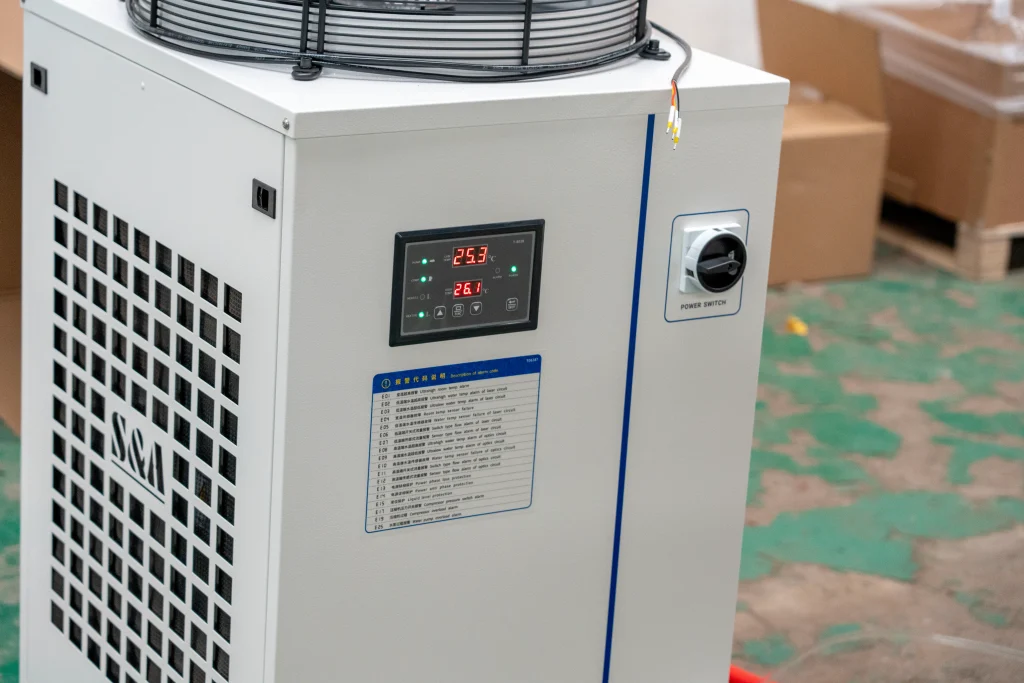
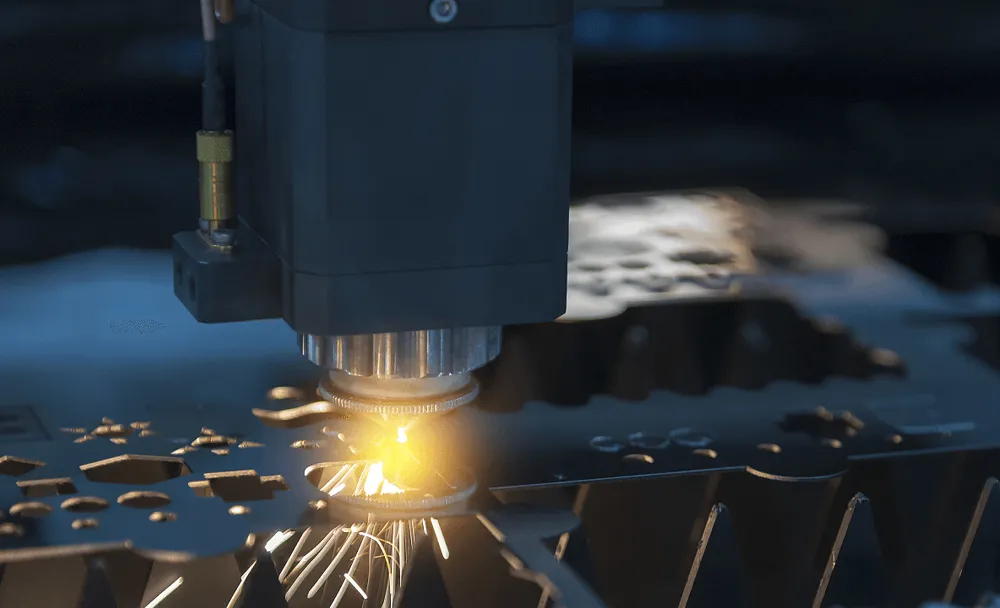
- The Process of Laser Cutting Sheet Metal
1. Design and Input: The process begins with creating a design using CAD software. The design is then converted into a CNC-readable format.
2. Материальное размещение: The sheet metal is positioned on the cutting bed and secured for stability.
3. Laser Operation: The laser beam is directed onto the metal, melting or vaporizing it along the specified path. The assist gas helps to clear away molten material.
4. Cutting and Finishing: Once the cutting is complete, the parts are removed, inspected, and any required post-processing is done, such as deburring.
3. Types of Laser Cutting Machines for Sheet Metal
There are two primary types of laser cutting machines commonly used for sheet metal: волокно -лазеры и лазеры CO2. Each has unique advantages that make them suitable for specific applications.
- Волоконные станки для лазерной резки
Fiber laser cutting machines are known for their efficiency and precision. They use a solid-state laser, where the light is amplified through optical fibers. Key characteristics include:
– Higher Precision: Fiber lasers produce a smaller beam diameter, allowing for sharper cuts and finer details.
– Better for Reflective Metals: Due to their shorter wavelength, fiber lasers are particularly effective at cutting reflective metals like aluminum and copper.
– Lower Maintenance: These machines are typically more robust and require less maintenance compared to CO2 lasers.
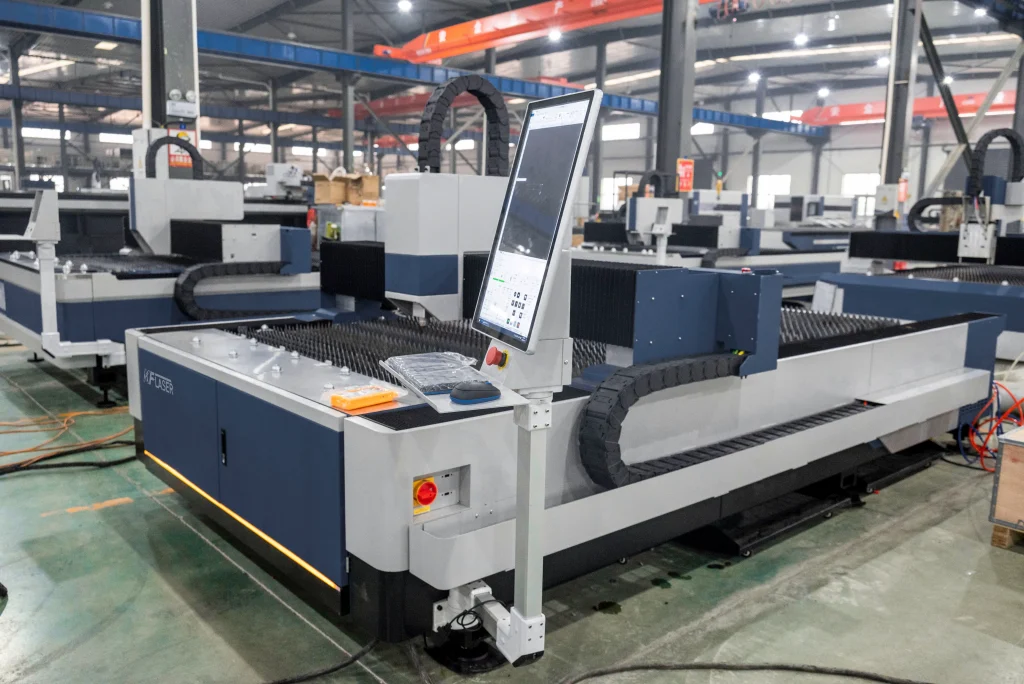
- Станки для лазерной резки CO2
CO2 lasers utilize a gas mixture (primarily CO2) Чтобы генерировать лазерный луч. They are often used for non-metal materials but can also cut certain metals with appropriate settings. Key characteristics include:
– Wider Beam: The larger beam size is effective for cutting thicker materials, though it may be less precise than fiber lasers for detailed work.
– More Suitable for Non-Metallic Materials: CO2 lasers are ideal for cutting wood, пластмассы, and other organic materials, making them versatile for mixed-material projects.
– Lower Initial Cost: CO2 laser machines generally have a lower upfront cost, though their operating costs can be higher due to power consumption and maintenance.
4. Benefits of Using Laser Cutting Machines for Sheet Metal
The popularity of laser cutting machines for sheet metal stems from their numerous advantages. Here’s a closer look at what makes them the go-to choice for manufacturers:
- Точность и аккуратность
Laser cutting provides extremely tight tolerances, making it ideal for applications requiring high precision, such as aerospace components and medical devices. The ability to maintain consistent accuracy throughout production ensures that parts fit together perfectly, reducing assembly time and costs.
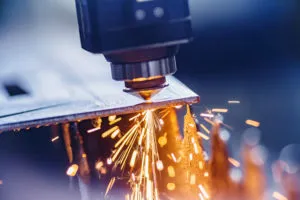
- Скорость и эффективность
Laser cutting machines can cut through sheet metal at impressive speeds, especially when working with thinner materials. Эта скорость приводит к более высокой производительности, allowing manufacturers to fulfill large orders quickly. Кроме того, the rapid processing capabilities mean that more complex designs can be executed without a significant time penalty.
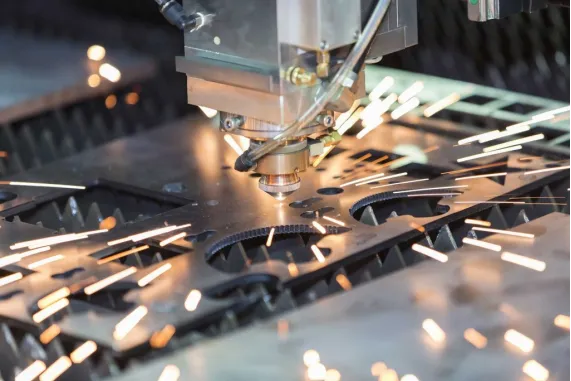
- Clean Cuts and Minimal Post-Processing
Laser cutting produces smooth edges with minimal burrs, reducing the need for additional finishing processes like grinding or sanding. This clean-cut finish is particularly important for applications where appearance and precision are critical, such as in consumer electronics and high-end furniture.
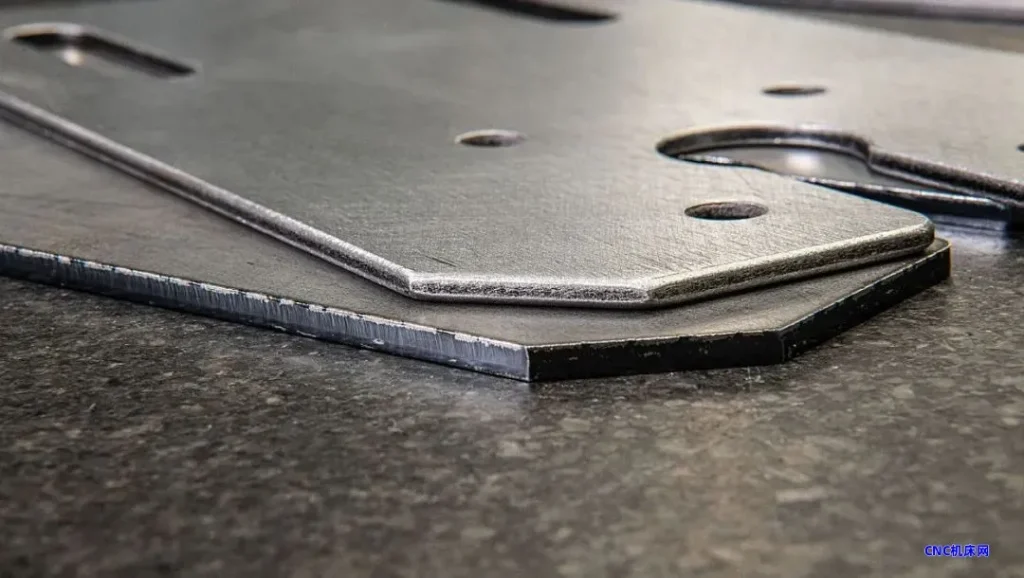
- Универсальность в обработке материалов
Laser cutting machines can process a wide range of metals, включая нержавеющую сталь, углеродистая сталь, алюминий, и медь. Такая универсальность делает их пригодными для различных отраслей промышленности., from automotive manufacturing to architectural design. They can also adapt to different material thicknesses, providing flexibility in production.
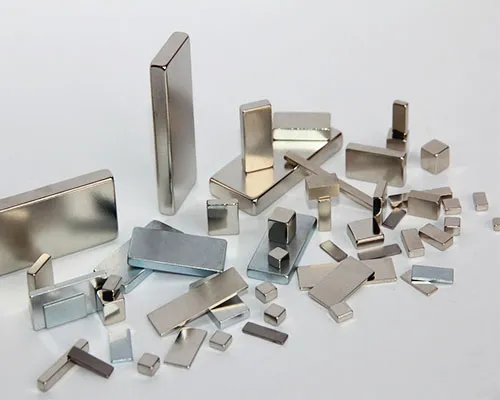
- Автоматизация и интеграция
Современные лазерные режущие машины могут быть интегрированы в автоматизированные производственные линии, снижение необходимости ручного вмешательства. Features like automatic loading and unloading systems, мониторинг в реальном времени, and CNC programming simplify the manufacturing process, allowing for continuous, масштабная продукция.
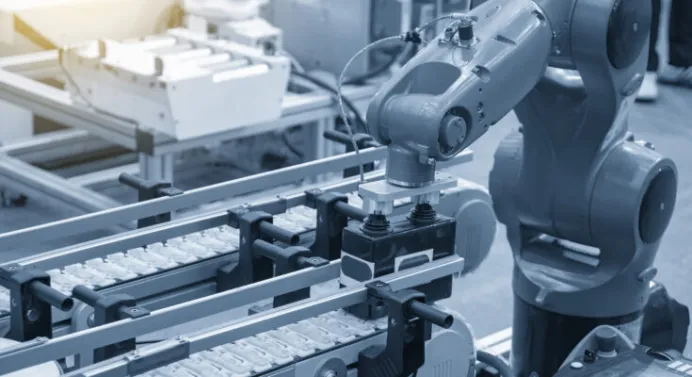
5. Applications of Laser Cutting Machines in Different Industries
The capabilities of laser cutting machines make them valuable across a wide range of industries. Here are some of the primary sectors where these machines play a crucial role:
- Автоматизированная индустрия
Laser cutting machines are used to produce intricate parts for vehicles, such as engine components, панели кузова, и выхлопные системы. The precision and speed of laser cutting help automotive manufacturers meet the strict safety and performance standards required in this sector.
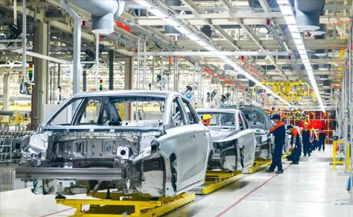
- Аэрокосмическая промышленность
In aerospace, laser cutting machines are essential for creating lightweight yet strong components. The ability to cut complex shapes with high accuracy ensures that each part meets stringent specifications, contributing to the overall safety and efficiency of aircraft.
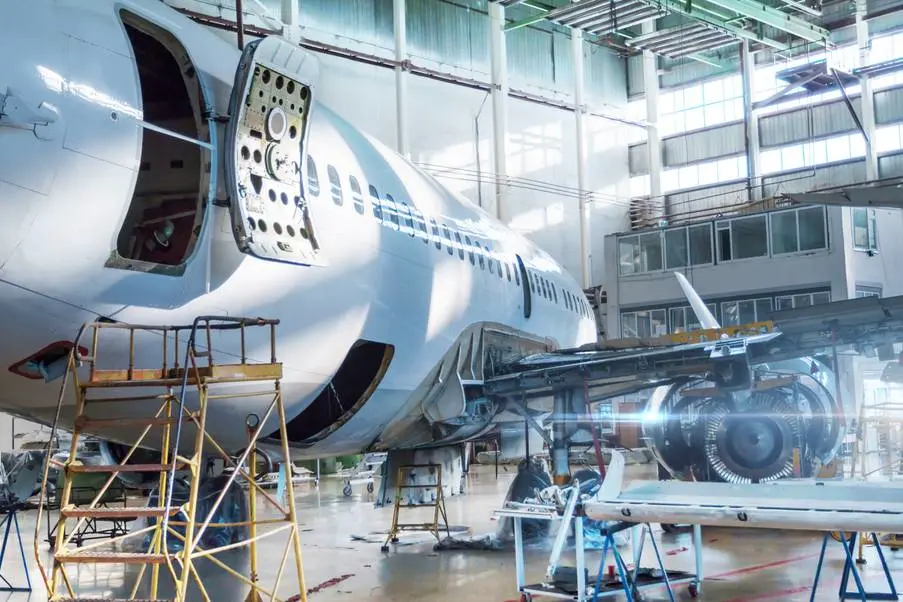
- Производство электроники
Laser cutting is ideal for the precise cutting of metal parts used in electronics, such as heat sinks, шасси, и корпуса. The process ensures that components fit precisely within devices, enhancing product reliability and durability.
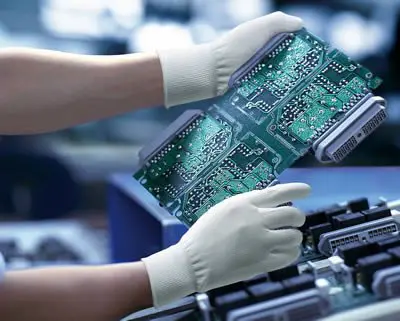
- Строительство и Архитектура
В строительстве, laser-cut metal is used for structural elements, декоративные панели, and custom architectural features. The ability to create intricate designs allows architects and builders to bring unique concepts to life, from modern facades to detailed interior elements.
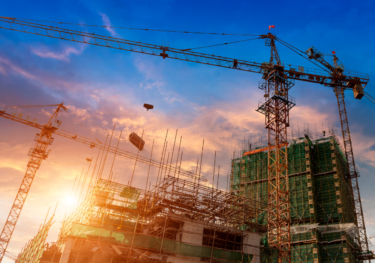
- Medical Devices and Equipment
Medical instruments and devices require high levels of precision, which makes laser cutting an ideal choice for their fabrication. From surgical tools to implants, laser-cut metal parts meet the exacting standards of the medical industry.
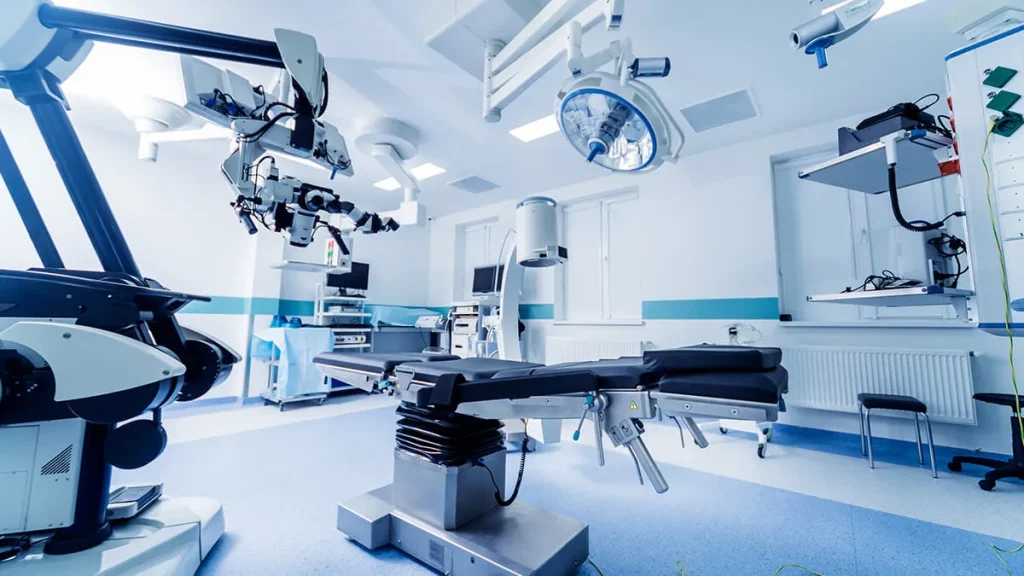
6. Key Considerations When Choosing a Laser Cutting Machine for Sheet Metal
Selecting the right laser cutting machine involves evaluating several critical factors to ensure that it meets your production needs. Here’s what to consider:
- Тип и толщина материала
Different metals and material thicknesses require different laser power levels. While fiber lasers excel at cutting thinner metals with high precision, thicker materials might benefit from the broader beam of a CO2 laser. It’s essential to match the machine’s capabilities with the types of materials you will be working with.
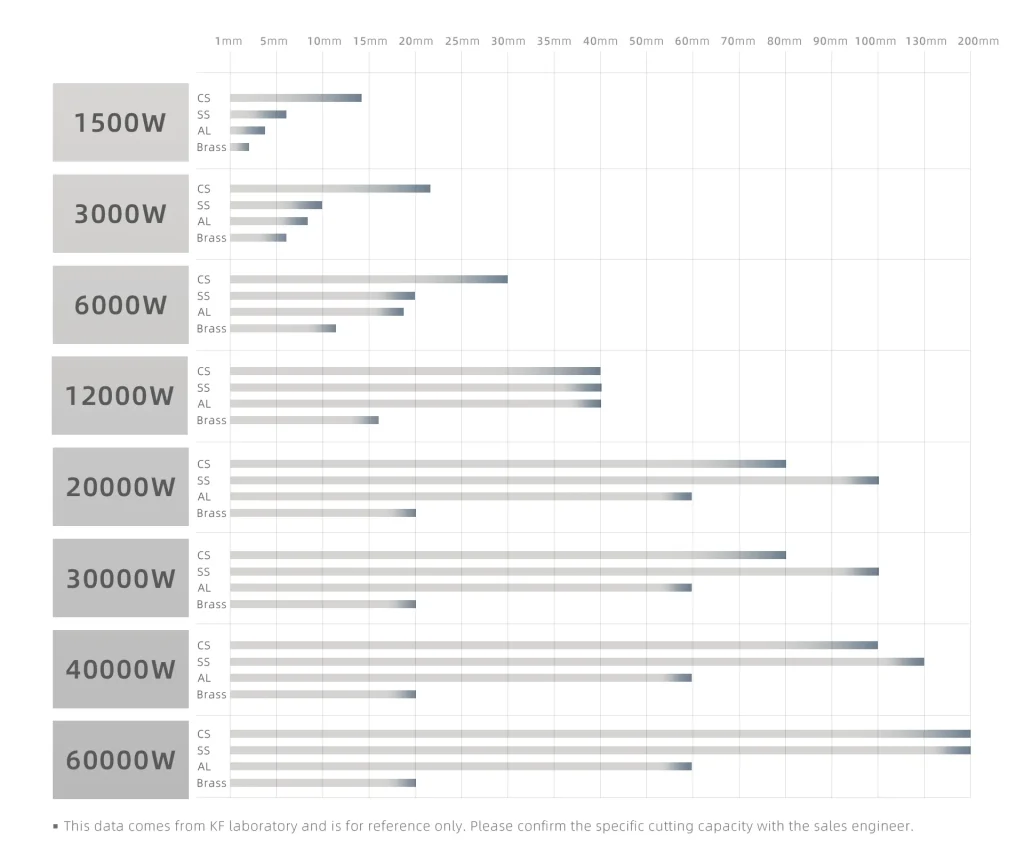
- Скорость резки и точность
The balance between speed and precision is crucial. Faster cutting speeds increase productivity but might compromise the cut quality for intricate designs. Consider the complexity of your projects and choose a machine that offers adjustable settings to meet your specific requirements.
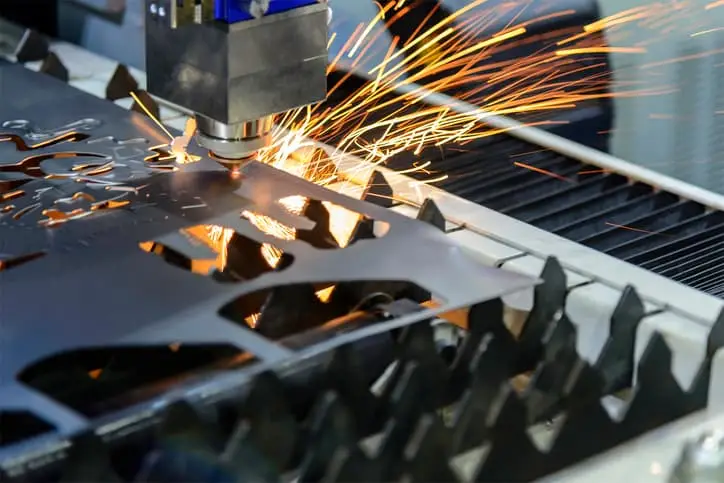
- Затраты на техническое обслуживание и эксплуатацию
While fiber lasers generally have lower maintenance needs, they may require higher initial investment. Evaluate the long-term operating costs, включая потребление энергии, replacement parts, and maintenance frequency, to ensure that the machine is cost-effective over its lifespan.
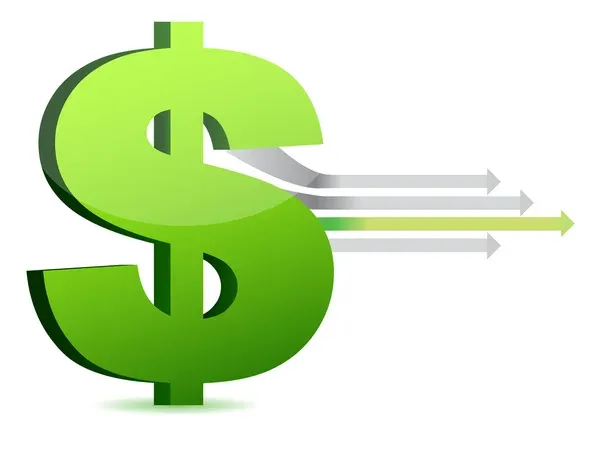
- Возможности автоматизации
Для крупносерийного производства, automation features such as automated loading systems, программное обеспечение для гнездования, and real-time monitoring can significantly reduce labor costs and improve efficiency. Consider machines that offer these capabilities if you plan to scale your operations.

7. Enhancing Productivity with the Right Laser Cutting Settings
Getting the best performance from a laser cutting machine involves fine-tuning the settings to match your material and design needs. Here are some tips to optimize your laser cutting process:
- Adjusting Laser Power
Higher power settings are suitable for thicker metals, while lower settings work best for thin sheets to avoid burning or warping. Adjusting the power appropriately ensures clean cuts without excess heat affecting the material.
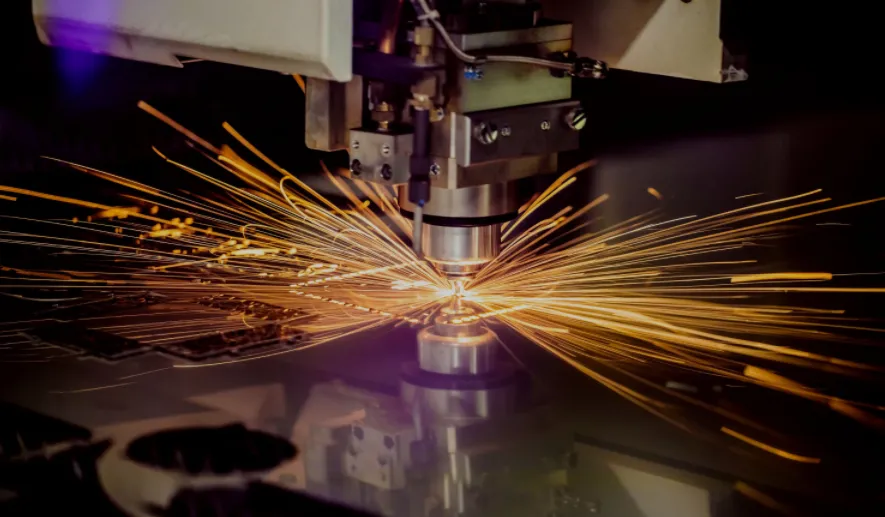
- Selecting the Right Assist Gas
The choice of assist gas—oxygen, азот, or air—can impact the cut quality and speed. Например, oxygen is often used for cutting thicker steel as it accelerates the cutting process through oxidation, while nitrogen is preferred for clean cuts on stainless steel to prevent oxidation.
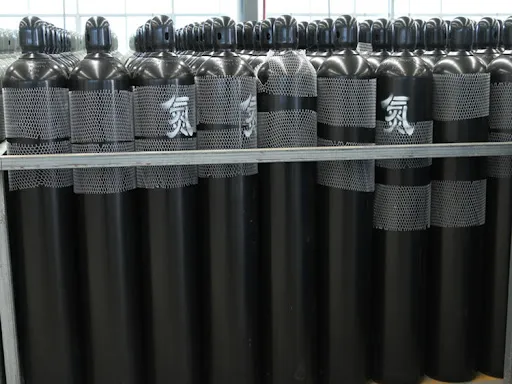
- Focusing the Laser Beam
Proper focus is crucial for achieving precise cuts. Use focus test routines to determine the optimal distance between the cutting head and the workpiece. This ensures that the laser energy is concentrated on the right spot, producing smoother edges and sharper details.
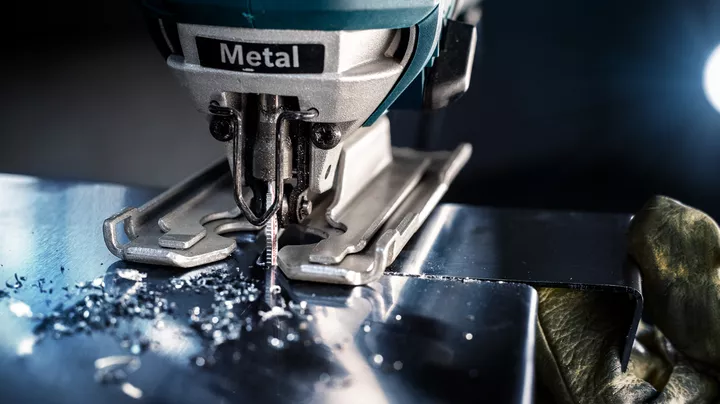
- Managing Cutting Speed
Finding the right balance between speed and quality is essential. A higher speed may be effective for simple cuts, but intricate designs might require slower speeds to maintain accuracy. Testing different speeds can help you find the best setting for each project.
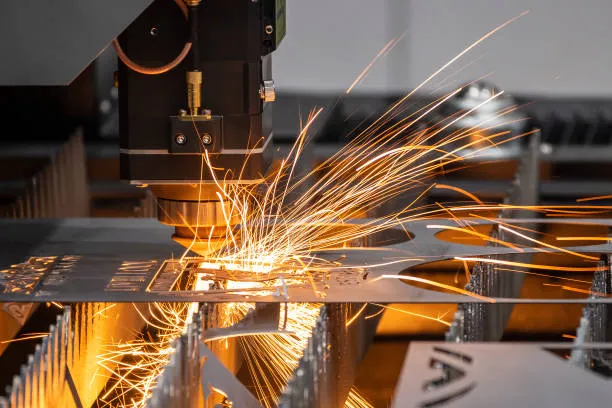
8. Будущие тенденции в технологии лазерной резки
Laser cutting technology continues to evolve, with new innovations making machines more efficient and versatile.
Some emerging trends include:
– Hybrid Laser Machines: Combining fiber and CO2 capabilities in a single machine, offering greater flexibility for manufacturers handling diverse materials.
– AI Integration: Advanced software using artificial intelligence to optimize cutting paths, reducing material waste and increasing production speed.
– Enhanced Safety Features: Innovations like automatic shut-off and real-time monitoring improve safety in industrial settings, allowing operators to focus on productivity.
These advancements promise to make laser cutting even more accessible and efficient, helping manufacturers stay competitive in a rapidly changing market.
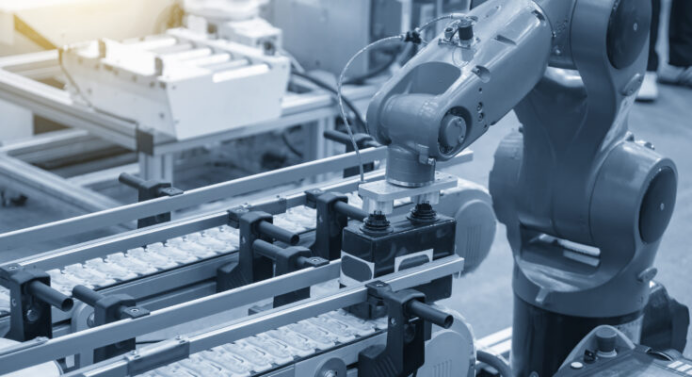
Заключительные мысли
Laser cutting machines for sheet metal are indispensable tools in modern manufacturing. Their ability to deliver precision, скорость, and versatility makes them ideal for a wide range of applications. By understanding the strengths and capabilities of different machines, manufacturers can select the right equipment to enhance their production processes, achieving superior results and keeping pace with industry demands.
Главные новости
-
Laser Cutting Aluminum Tube: Techniques and Benefits Explained06 Sep 2025
-
Laser Cutting Aluminum with Oxygen: Boosting Precision and Efficiency05 Sep 2025
-
Efficient Laser Cutting Machine for Brass Sheet: Enhance Your Precision Cutting04 Sep 2025
-
Laser Cutting Machine Sheet: The Key to Precision and Efficiency in Modern Manufacturing02 Sep 2025
-
Laser Cutting Stainless Steel with Oxygen: Revolutionizing the Cutting Process31 Август 2025
Категории продуктов
- Металлический лазерный резак
- Лазерный сварочный аппарат
- Лазерный очиститель
- Лазерный маркер
- Пресс-тормозная машина