News
Laser Cutting Metal Machine: The Future of Metal Processing
In today’s fast-paced manufacturing landscape, the laser cutting metal machine has become a game-changer. With its exceptional precision, speed, and versatility, it is replacing traditional cutting methods across a wide range of industries. From aerospace to automotive, the ability to cut metal with a focused laser beam is transforming production lines and enabling manufacturers to produce complex components with minimal waste. In this article, we’ll dive deep into the technology, benefits, applications, and future of laser cutting metal machines.

1. What is a Laser Cutting Metal Machine?
A laser cutting metal machine uses a high-powered laser beam to precisely cut or engrave metal sheets, tubes, and other materials. The technology utilizes a laser’s intense light energy, which is directed onto the material. The heat from the laser melts or vaporizes the metal, and a stream of gas is used to blow away the molten material, leaving behind a clean, sharp cut.
Unlike traditional cutting methods like plasma or mechanical cutting, the laser cutting process does not involve direct physical contact with the material. This results in less wear and tear on the equipment and the elimination of mechanical stress on the workpiece.
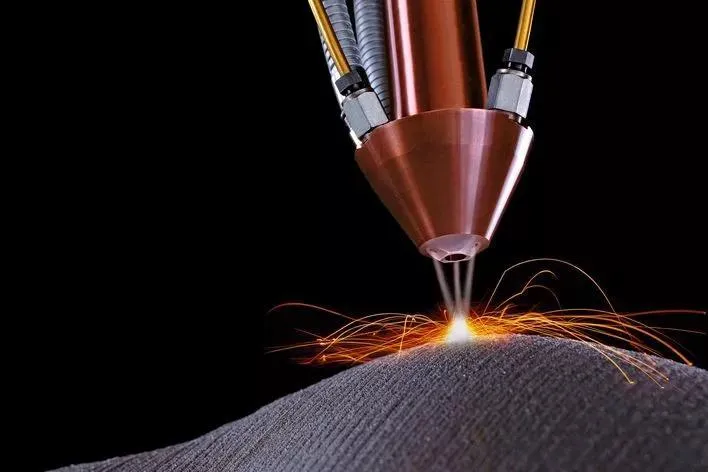
2. How Does Laser Cutting Work?
The laser cutting process involves several key steps that contribute to its precision and efficiency. Here’s a breakdown of how it works:
◆ Laser Generation
A high-powered laser is generated using either a CO2 laser or a fiber laser. In a fiber laser, light is amplified through optical fibers, whereas CO2 lasers generate light through a chemical reaction in a gas-filled tube. The laser’s light is concentrated into a fine beam that can be accurately focused on the material.
◆ Beam Focusing
The focused laser beam is directed onto the metal material. The diameter of the beam can be as small as 0.1 mm, allowing for extremely fine and detailed cuts. A series of mirrors and lenses are used to focus the laser beam to the exact point of cutting.
◆ Melting and Vaporization
As the laser beam hits the metal, it rapidly heats the material to its melting point. For thinner materials, the laser vaporizes the metal directly. For thicker materials, the heat causes the metal to melt, and a high-pressure gas is used to blow the molten metal away from the cutting area.
◆ Edge Formation
The result is a precise cut with smooth edges and minimal heat distortion. The controlled process reduces the amount of scrap material and allows for intricate shapes to be cut with accuracy.
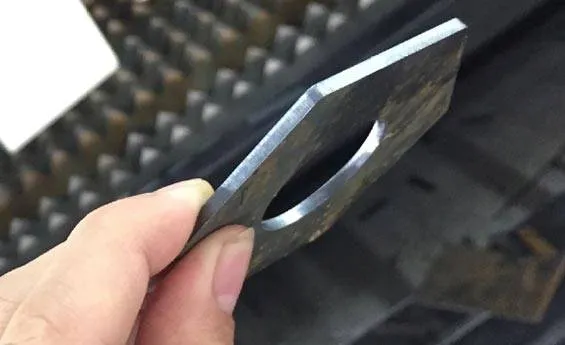
3. Advantages of Using a Laser Cutting Metal Machine
The laser cutting metal machine offers a multitude of benefits that have made it a staple in modern manufacturing. Here are some of the key advantages:
◆ High Precision and Accuracy
Laser cutting machines are known for their remarkable precision. The focused laser beam allows for extremely fine cuts, which are crucial for industries where accuracy is paramount. The ability to cut tight tolerances with minimal error makes laser cutting ideal for applications like aerospace and medical device manufacturing.
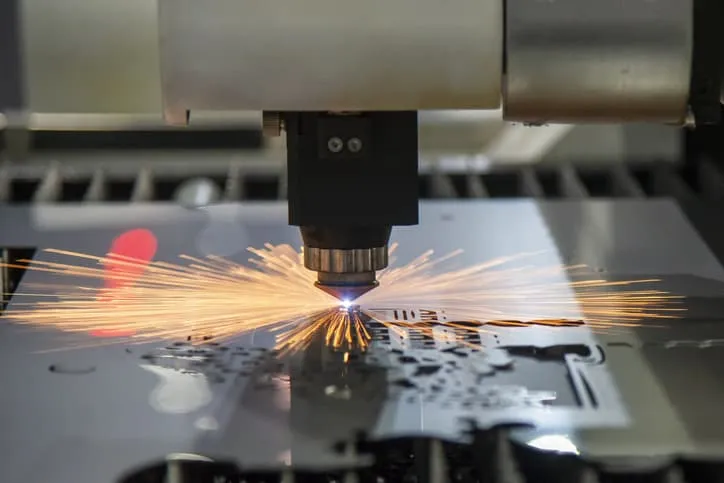
◆ Versatility Across Materials
Laser cutting metal machines are highly versatile and can cut through a wide variety of metals, including steel, aluminum, brass, and titanium. Additionally, the technology can be used on both thin and thick materials, making it suitable for a range of industries.
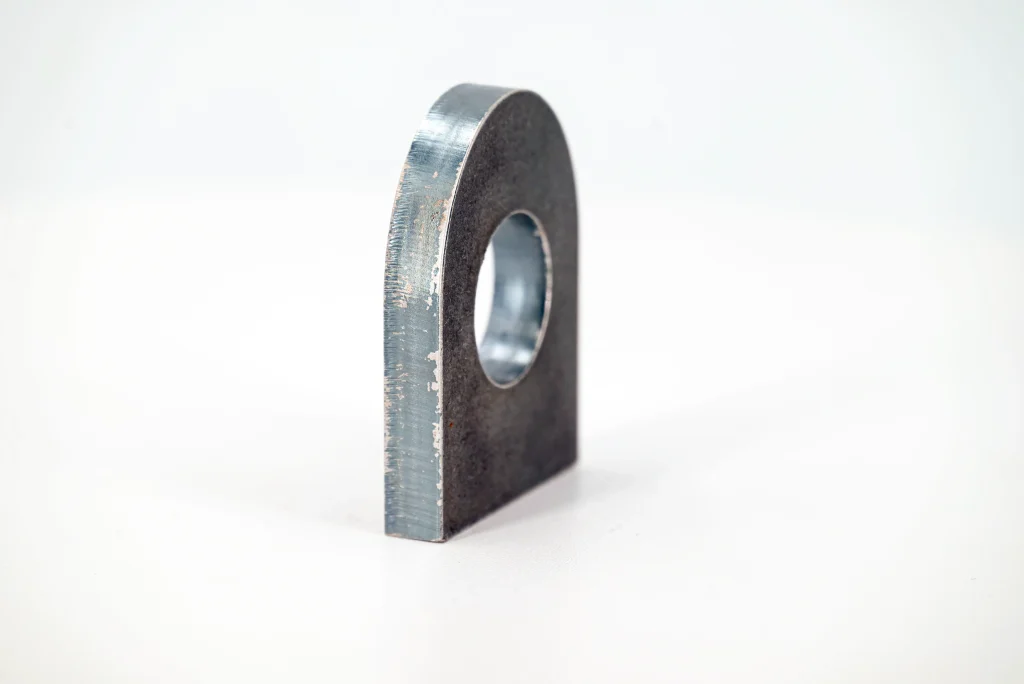
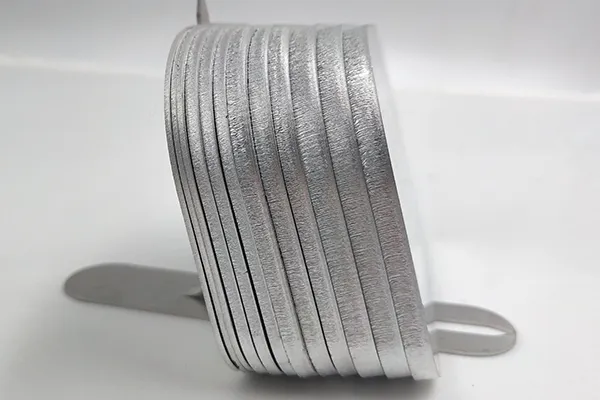
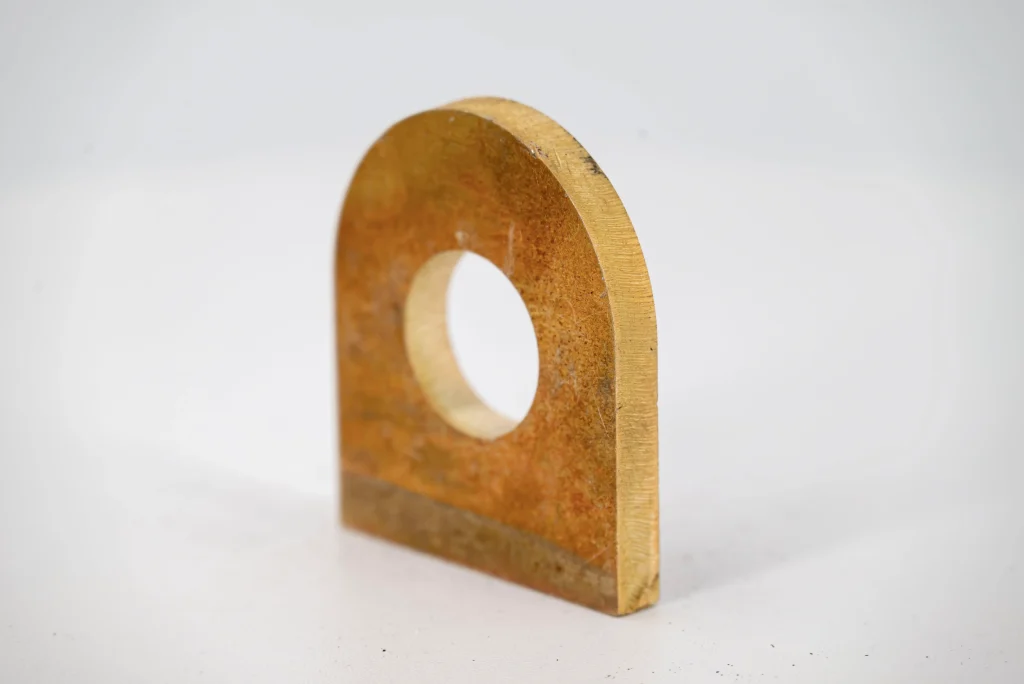
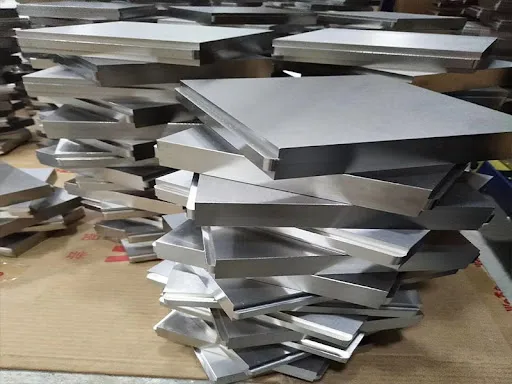
◆ Speed and Efficiency
Compared to traditional cutting methods, laser cutting is significantly faster. The speed of the process allows manufacturers to increase production output, which can lead to reduced lead times and lower operational costs. Moreover, laser cutting reduces the need for post-processing or finishing work, further increasing overall efficiency.
◆ Reduced Waste
Because laser cutting is such a precise process, it results in less material waste compared to traditional cutting methods. The clean cuts and minimal heat-affected zones mean that less scrap material is generated, helping manufacturers save on raw materials and reduce costs.
◆ No Tool Wear
Unlike mechanical cutting methods, laser cutting does not involve any contact between the cutting tool and the material. This means that there is no wear on the tool, and the machine’s cutting head remains sharp, reducing downtime and maintenance costs.

4. Key Applications of Laser Cutting Metal Machines
Laser cutting machines are used in various industries for a wide range of applications. The versatility of the technology makes it suitable for applications ranging from simple sheet metal cutting to intricate component fabrication.
◆ Automotive Industry
In the automotive industry, precision is critical when manufacturing components like exhaust systems, chassis parts, and body panels. Laser cutting machines are widely used for producing high-precision automotive components, which require exact dimensions and tight tolerances.
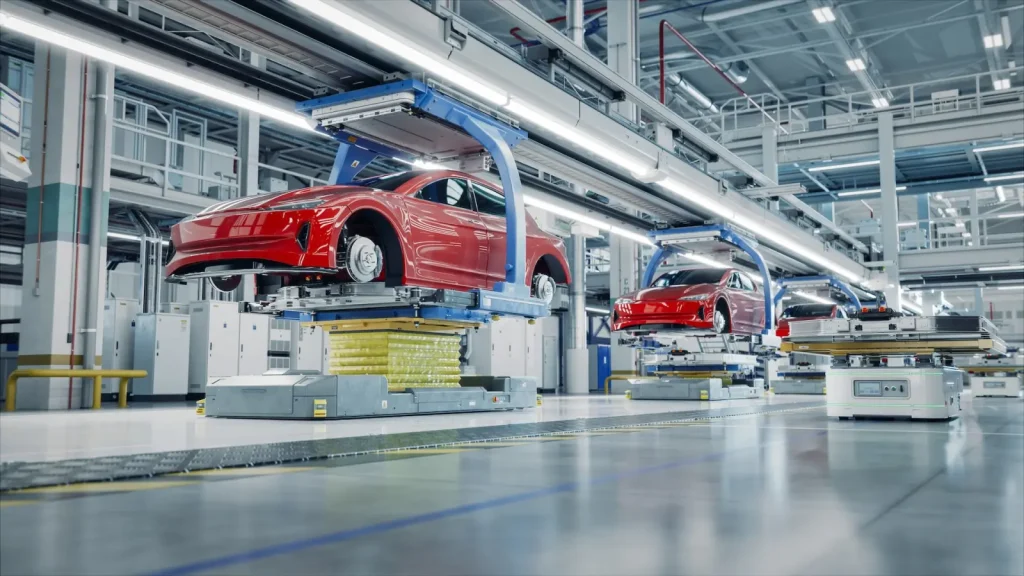
◆ Aerospace Industry
The aerospace sector demands materials with exceptional strength-to-weight ratios. Laser cutting machines are used to cut materials such as titanium and aluminum, which are commonly used in the construction of aircraft parts. The precision of the laser ensures that each part meets strict quality standards, essential for safety and performance.
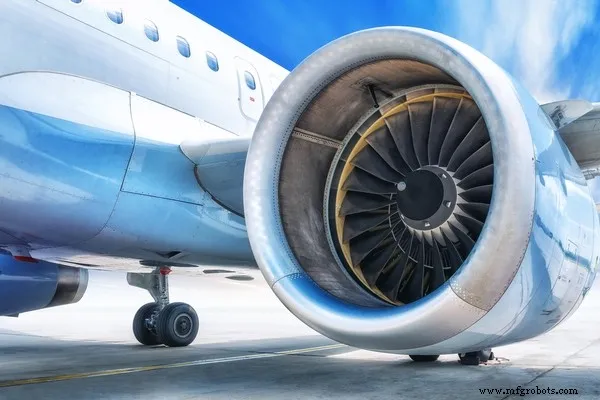
◆ Industrial Equipment Manufacturing
Laser cutting is commonly used to manufacture parts for industrial machinery. The ability to cut thick materials with clean edges ensures that components such as gears, pipes, and frames are manufactured to high standards. Additionally, laser cutting allows for complex shapes and designs that would be difficult or impossible to achieve with traditional cutting methods.
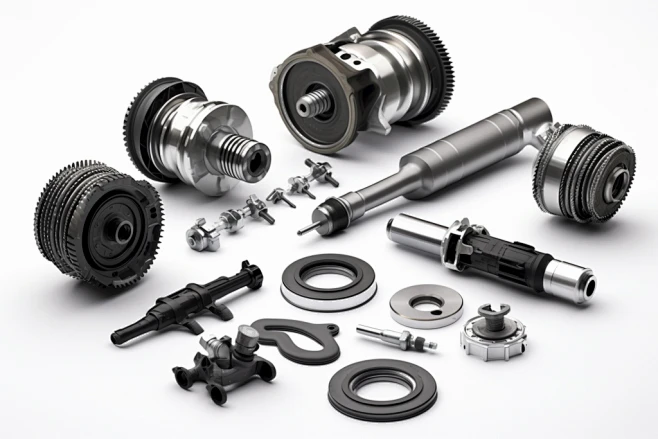
◆ Metal Fabrication
For metal fabricators, the ability to quickly and accurately cut metal is crucial to meeting customer demands. Laser cutting metal machines are a go-to solution for fabricators who need to create custom metal parts or products. Whether it’s a small batch or large-scale production, laser cutting ensures consistency and quality.
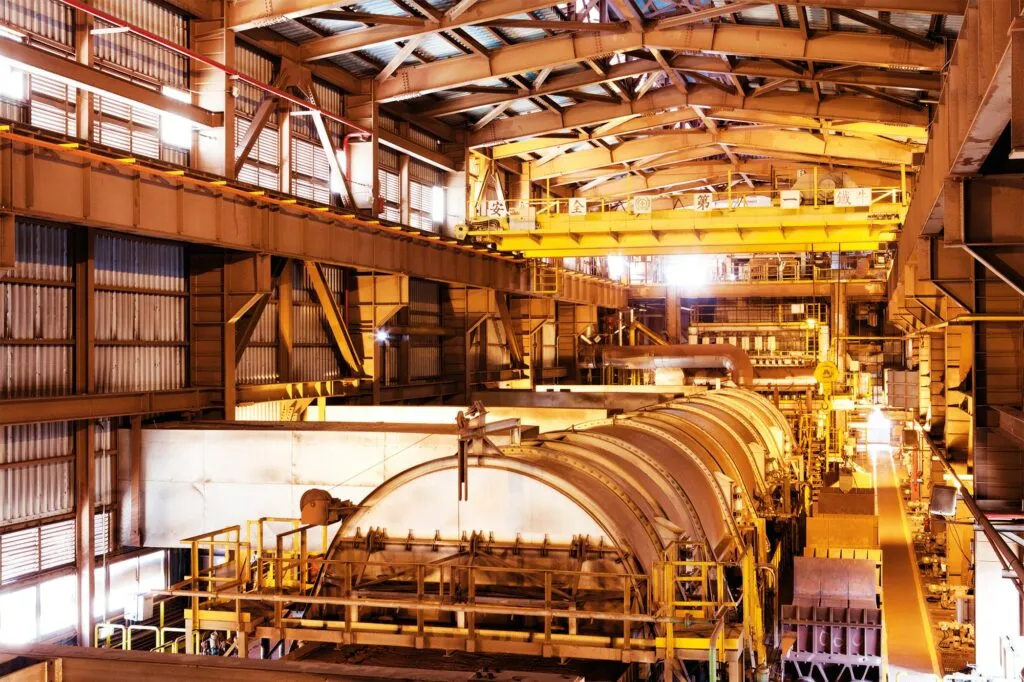
◆ Signage and Artistic Designs
Laser cutting machines are also used in the creation of custom signage and artistic designs. The precision of the laser allows for highly detailed patterns, logos, and designs to be cut into metal sheets. This is especially useful in the creation of decorative metalwork for interior design or outdoor signage.
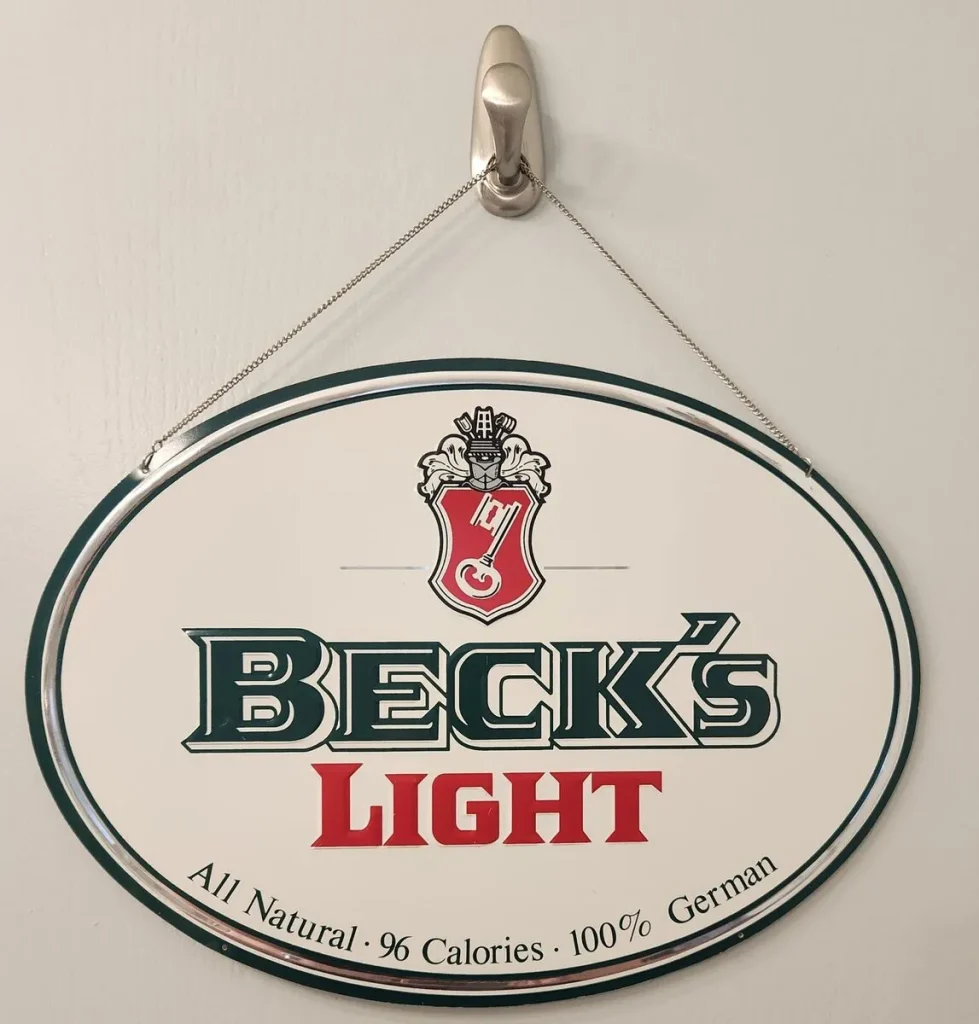
5. Comparison with Other Metal Cutting Technologies
While laser cutting metal machines are a powerful tool in modern manufacturing, it’s important to compare them with other cutting technologies to understand when laser cutting is the most effective option.
◆ Laser Cutting vs. Plasma Cutting
Plasma cutting is another popular method for cutting metal. While plasma cutting is faster and better suited for thicker materials, it produces rougher edges compared to laser cutting. Laser cutting provides a higher degree of precision and clean edges, making it more suitable for applications where appearance and accuracy matter.
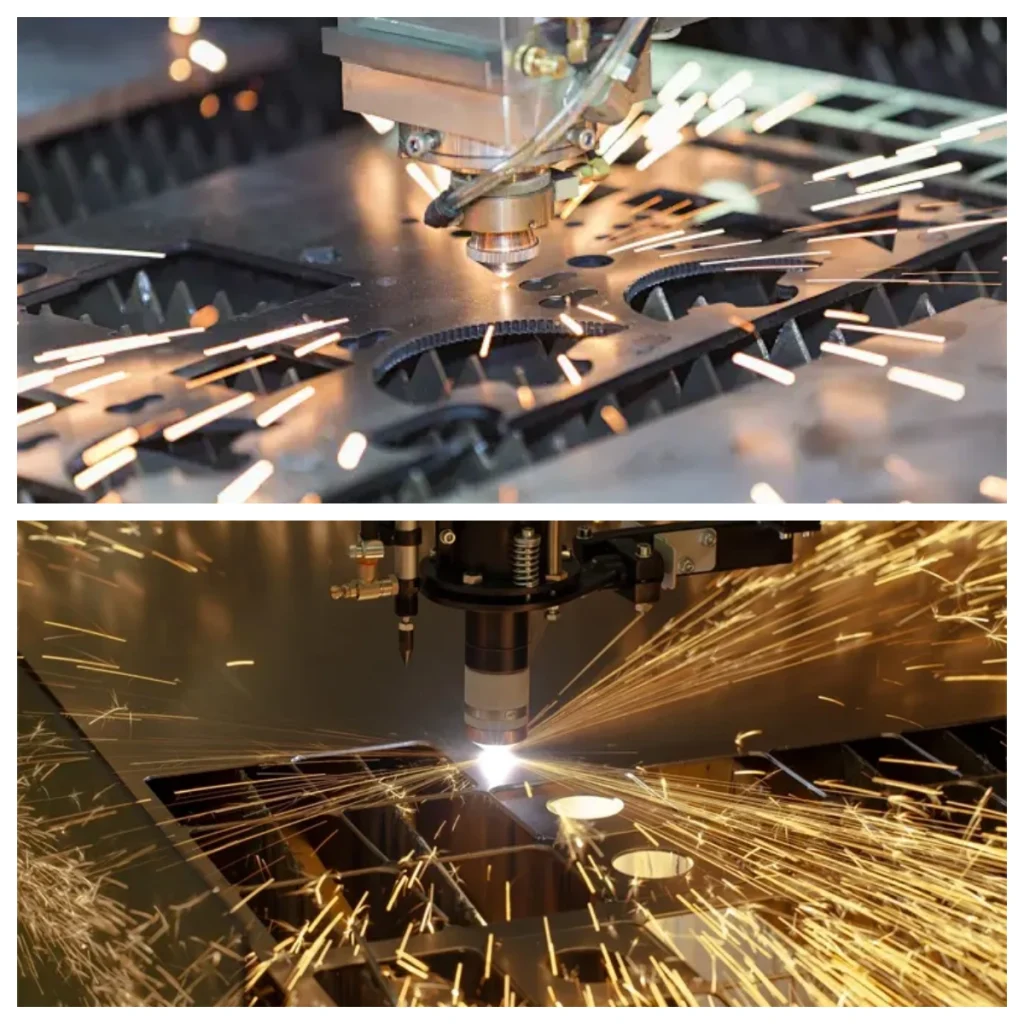
◆ Laser Cutting vs. Waterjet Cutting
Waterjet cutting uses a high-pressure stream of water mixed with abrasives to cut through materials. While waterjet cutting can also be used on a variety of metals, it is slower and may produce more material waste compared to laser cutting. Laser cutting, on the other hand, offers faster processing speeds and greater precision.
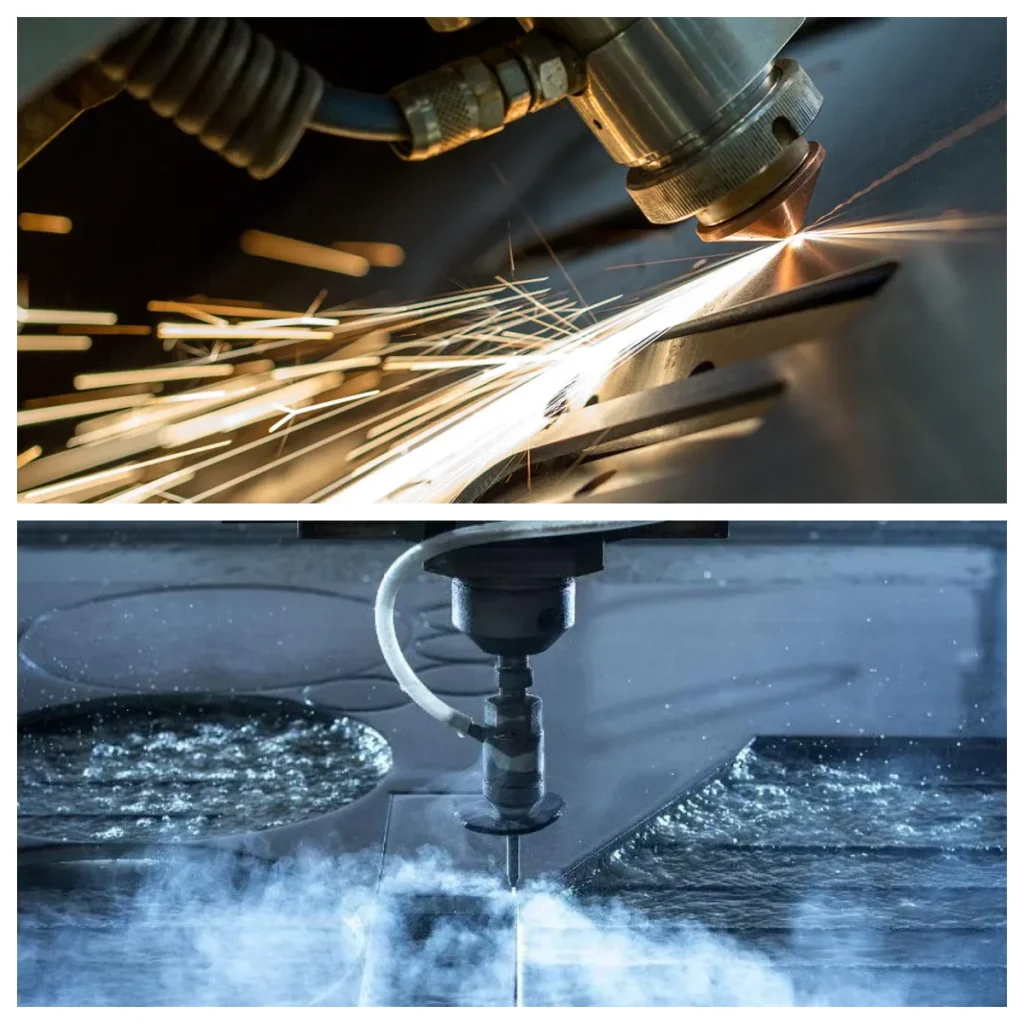
◆ Laser Cutting vs. Mechanical Cutting
Mechanical cutting methods, such as sawing or shearing, involve physical contact with the material and often result in material distortion and rough edges. Laser cutting, with its non-contact process, eliminates these issues, providing smoother cuts with minimal material stress.
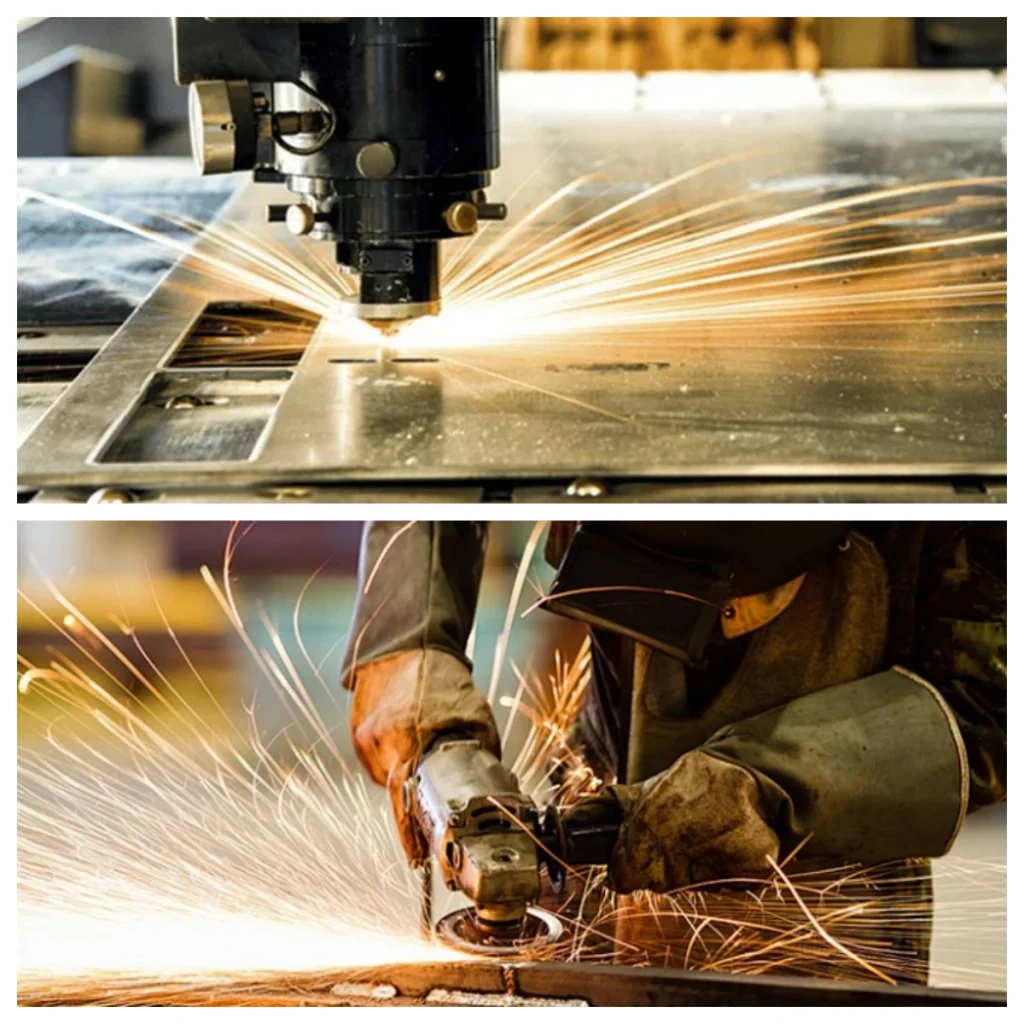
6. Factors to Consider When Choosing a Laser Cutting Metal Machine
When investing in a laser cutting metal machine, there are several factors to consider to ensure you choose the right machine for your needs.
◆ Power and Cutting Capacity
The power of the laser and its cutting capacity determine the thickness and type of metal the machine can handle. Higher-powered lasers are needed for cutting thicker metals, while lower-powered lasers are ideal for thinner materials.
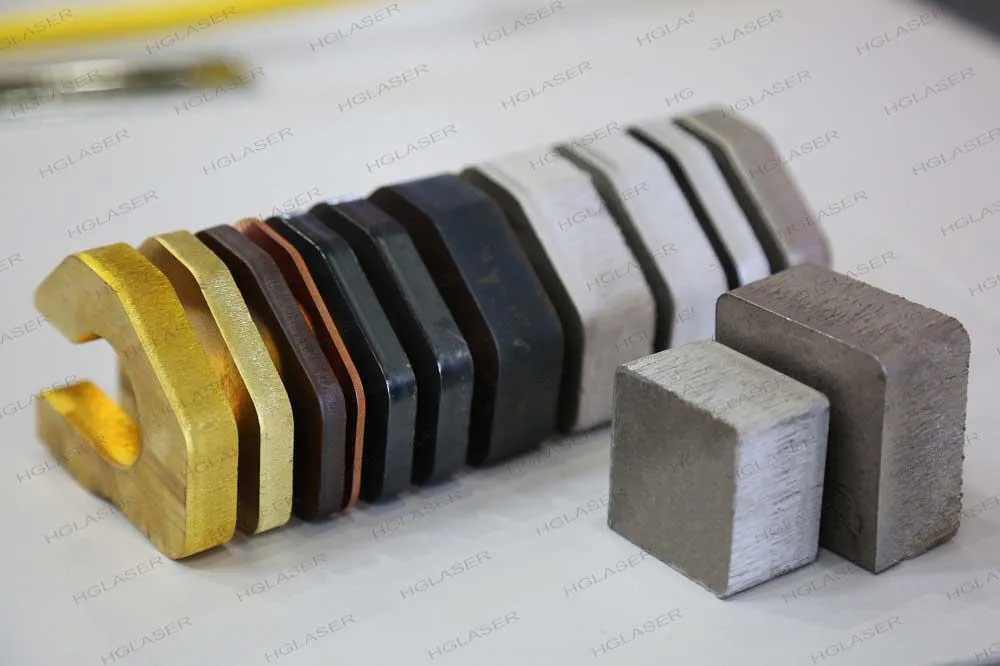
◆ Cutting Speed and Efficiency
Cutting speed is a critical factor when considering a laser cutting machine. Faster cutting speeds will increase throughput, while more efficient machines can help reduce energy consumption and lower operational costs.
◆ Automation Features
Modern laser cutting machines come with a range of automation features, such as automatic material loading and unloading, which can streamline production and reduce the need for manual labor. Be sure to consider the level of automation that will suit your production needs.
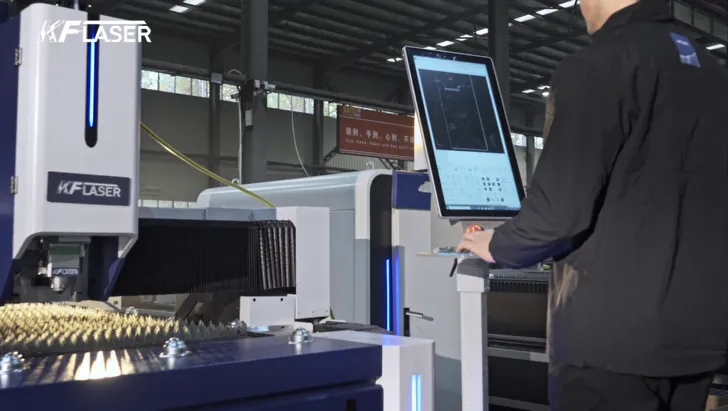
◆ Maintenance and Support
Regular maintenance is essential for the longevity and performance of a laser cutting machine. Choose a machine that offers easy maintenance and reliable support from the manufacturer to minimize downtime.
Laser Cutting Metal Machine: The Future of Metal Processing
The laser cutting metal machine has proven itself as a powerful and efficient tool for a wide range of industries. With its ability to deliver high-precision cuts at incredible speeds, it’s no surprise that laser cutting is fast becoming the preferred method for metal fabrication. Whether for automotive, aerospace, or industrial manufacturing, the advantages of laser cutting are undeniable, providing manufacturers with a tool that enhances both productivity and quality.
Top Stories
-
Laser Cutting Aluminum Tube: Techniques and Benefits Explained06 Sep 2025
-
Laser Cutting Aluminum with Oxygen: Boosting Precision and Efficiency05 Sep 2025
-
Efficient Laser Cutting Machine for Brass Sheet: Enhance Your Precision Cutting04 Sep 2025
-
Laser Cutting Machine Sheet: The Key to Precision and Efficiency in Modern Manufacturing02 Sep 2025
-
Laser Cutting Stainless Steel with Oxygen: Revolutionizing the Cutting Process31 Aug 2025
Product Categories
- Metal Laser Cutter
- Laser Welder Machine
- Laser Cleaner Machine
- Laser Marker Machine
- Press Brake Machine