News
Laser Metal Cutting: Precision Redefined for the Modern World
★ Preface
Imagine a world where precision meets speed, where raw metal transforms into intricate, flawless designs with the power of light. This is not just a technological marvel; it’s the heart of laser metal cutting, a game-changing process revolutionizing industries.
From aerospace to automotive, construction to custom art, laser cutting has emerged as the ultimate solution for those seeking perfection and efficiency in metal fabrication.
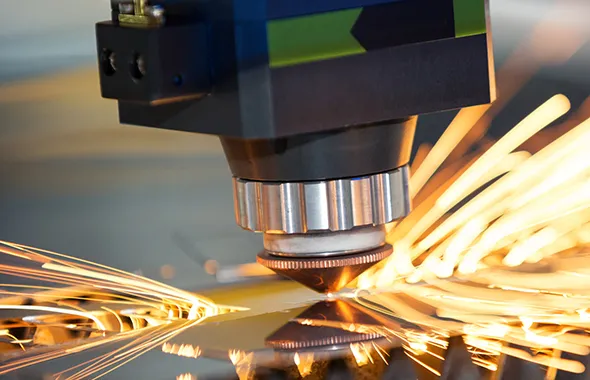
1.What is Laser Metal Cutting?
Laser metal cutting is a process that uses a focused beam of light to slice through various metals with unparalleled accuracy. By heating, melting, or vaporizing the material, the laser creates precise cuts, clean edges, and intricate patterns that traditional methods struggle to achieve.
The process relies on a combination of:
– Laser Source: The energy center that produces the high-powered beam.
– Optics and Focusing System: These concentrate the laser into a fine point, directing it precisely onto the metal surface.
– Assist Gas: Gases like oxygen or nitrogen are used to clear molten material, improve edge quality, and increase cutting efficiency.
☟ 10mm carbon steel cutting demonstration video is as follows:
From thin sheets of aluminum to robust steel plates, laser metal cutting works across a range of materials and thicknesses, offering versatility unmatched by other cutting methods.
2.Why Laser Metal Cutting is the Future of Fabrication
1. Precision Engineering
At the core of laser metal cutting is its unmatched precision. The focused laser beam can create intricate patterns and achieve tolerances as tight as a few micrometers. This precision is vital in industries like aerospace and medical manufacturing, where even the smallest deviations can have significant consequences.
2. Speed and Efficiency
Compared to traditional cutting methods like plasma or mechanical tools, laser metal cutting is significantly faster. It streamlines production processes, reducing lead times and increasing output without compromising quality.
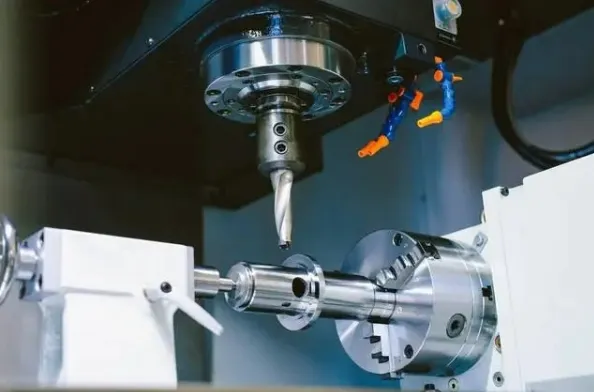
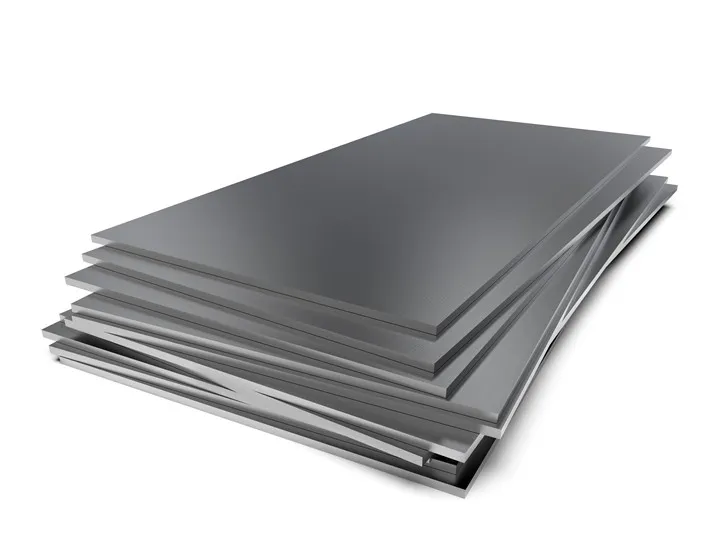
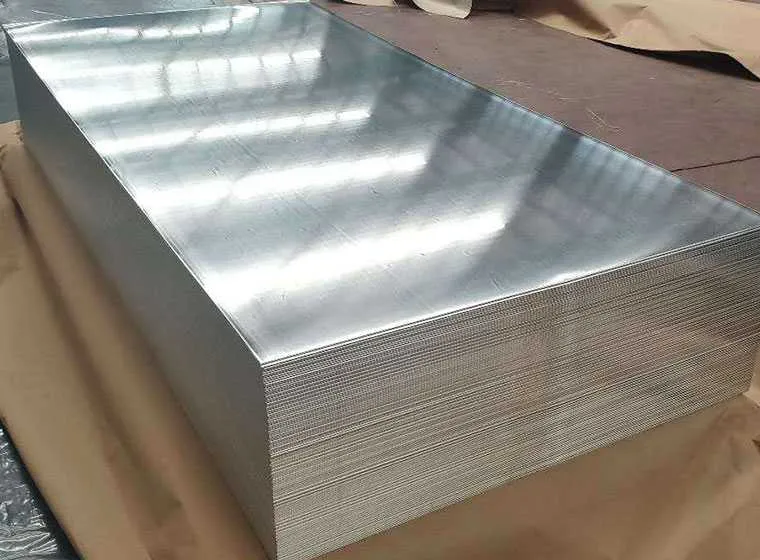
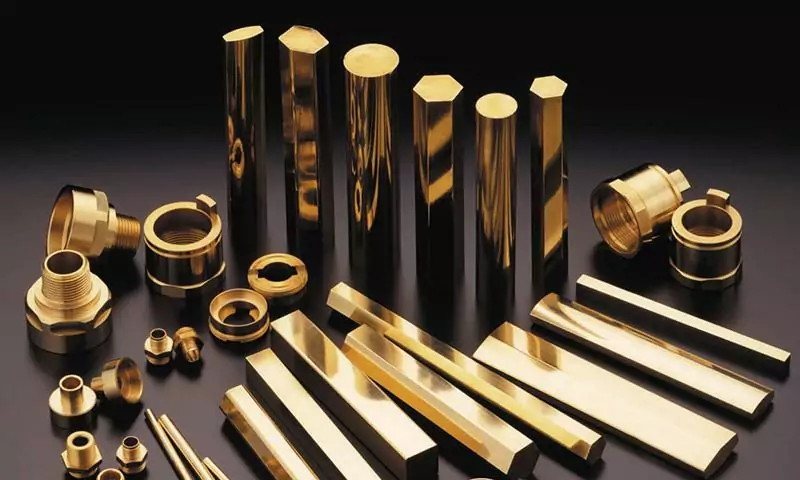
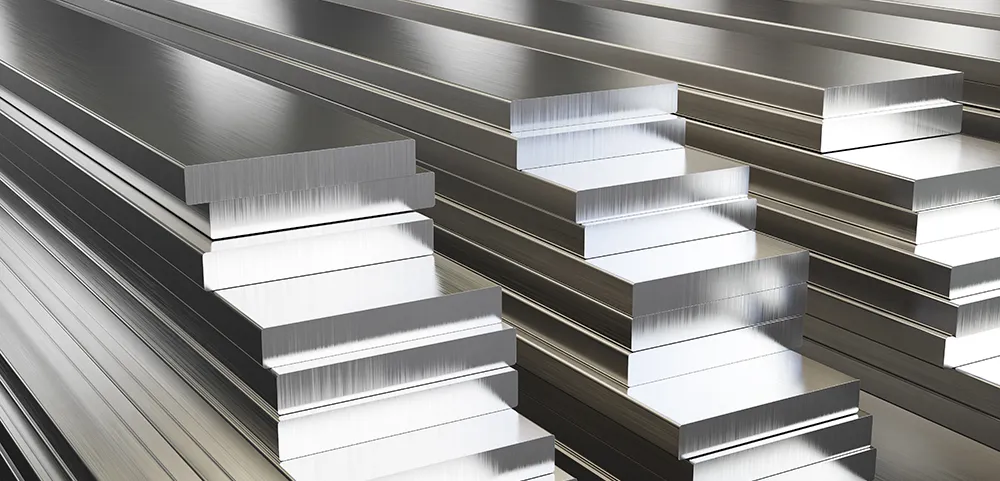
3. Versatility Across Materials
Laser cutting isn’t limited to a single type of metal. It works seamlessly with a variety of materials, including:
– Stainless Steel: Ideal for applications requiring strength and corrosion resistance.
– Aluminum: Lightweight and reflective, perfect for aerospace and automotive uses.
– Brass and Copper: For decorative elements or components needing high conductivity.
– Carbon Steel: A cost-effective choice for structural and industrial parts.
4. Cost-Effective Production
By minimizing material waste and reducing the need for additional finishing processes, laser metal cutting lowers production costs. Its precision also reduces errors, further saving time and money.
5. Eco-Friendly Fabrication
With minimal waste and energy-efficient operation, laser metal cutting aligns with sustainable manufacturing practices. The use of recyclable metals enhances its environmental credentials.
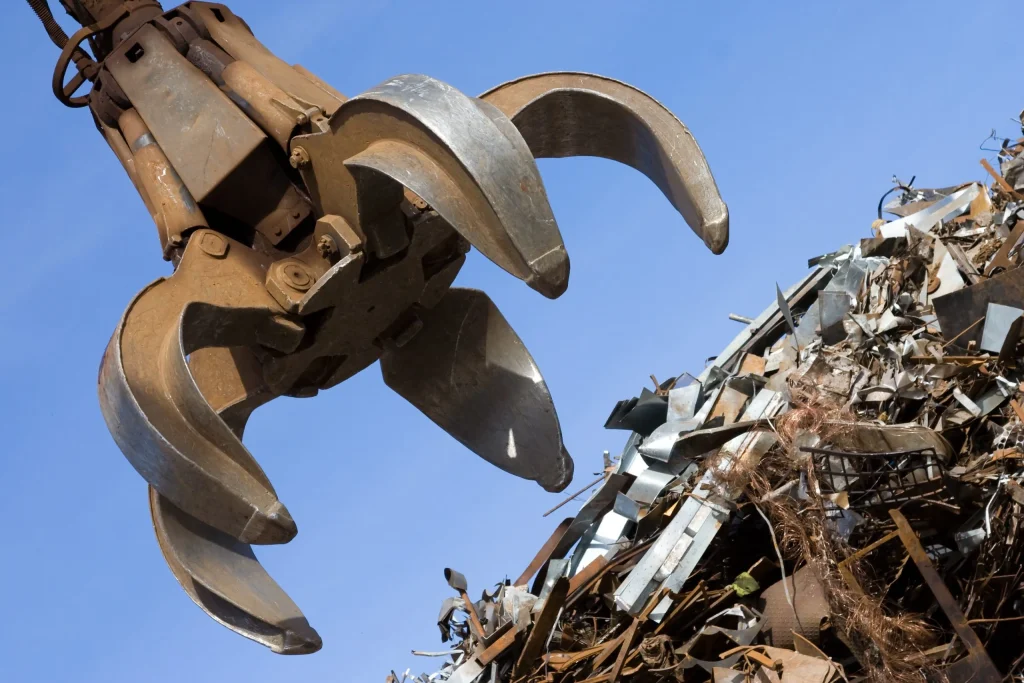
3.Key Applications of Laser Metal Cutting
1. Automotive Industry
Laser cutting is pivotal in the automotive sector, producing everything from chassis components to exhaust systems. Its ability to cut lightweight metals like aluminum helps manufacturers meet fuel efficiency and performance goals.
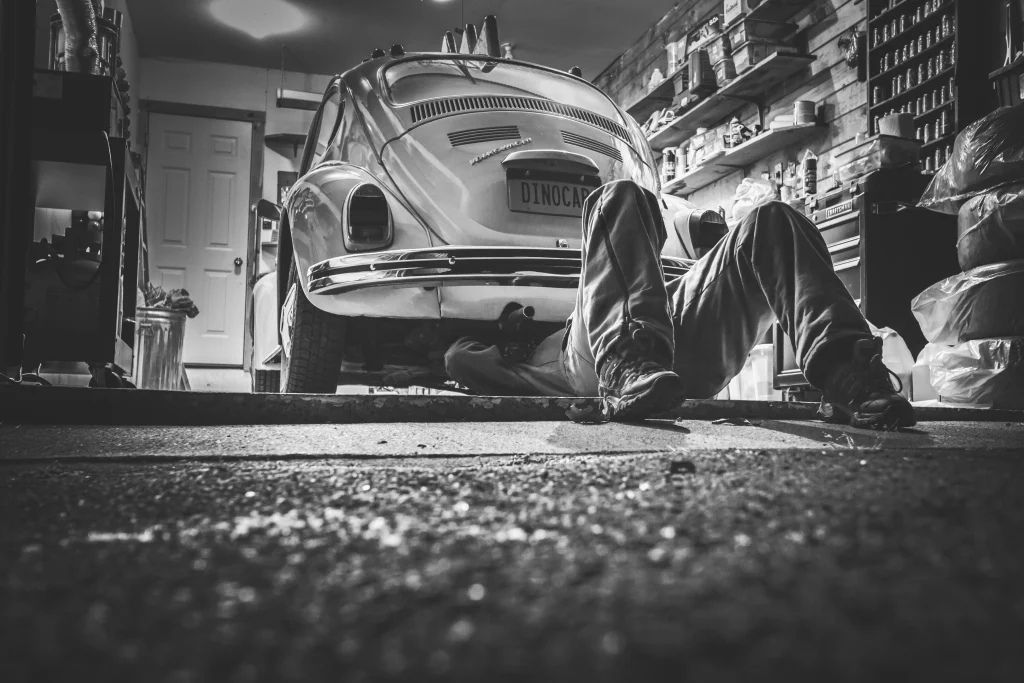
2. Aerospace and Defense
High precision and reliability make laser metal cutting indispensable for aerospace applications. Whether crafting turbine blades, fuselage panels, or intricate structural supports, the process ensures flawless execution.
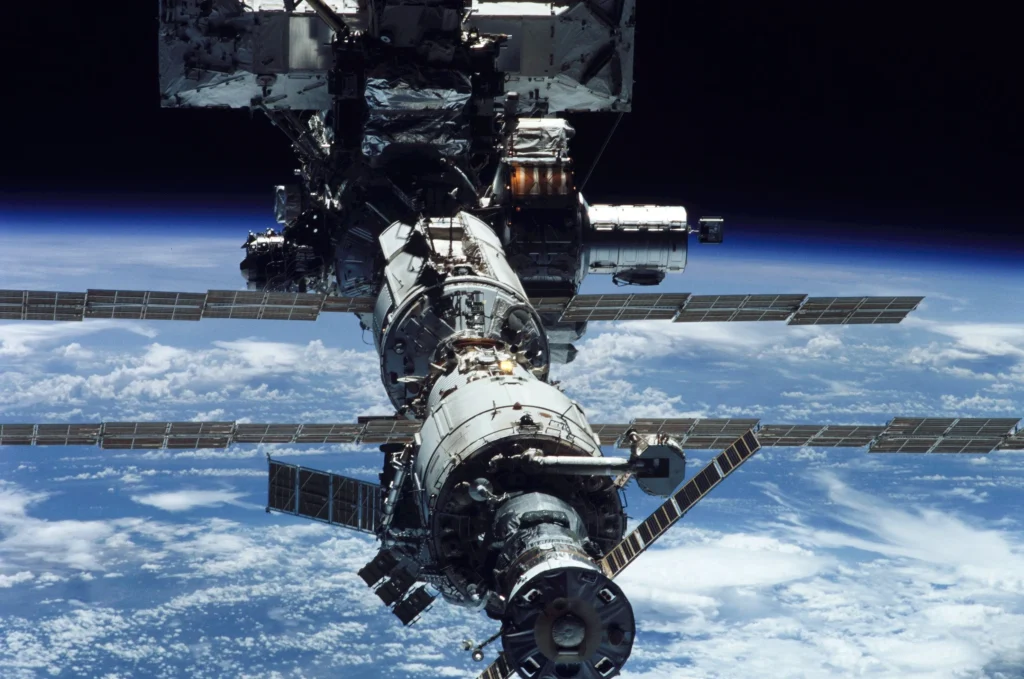
3. Architectural Design
From sleek building facades to custom interior decor, laser-cut metal enhances architectural aesthetics. The technology enables designers to create intricate patterns and shapes that elevate projects to new heights.
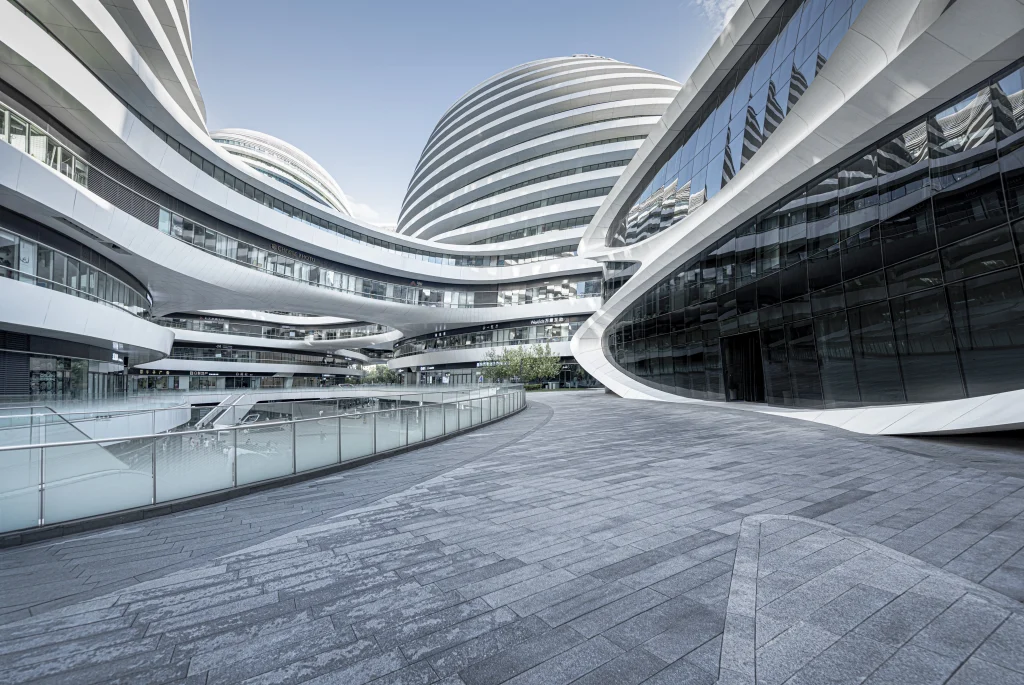
4. Industrial Manufacturing
For industrial applications, laser metal cutting is used to produce machine components, structural supports, and high-performance tools with consistent quality and durability.
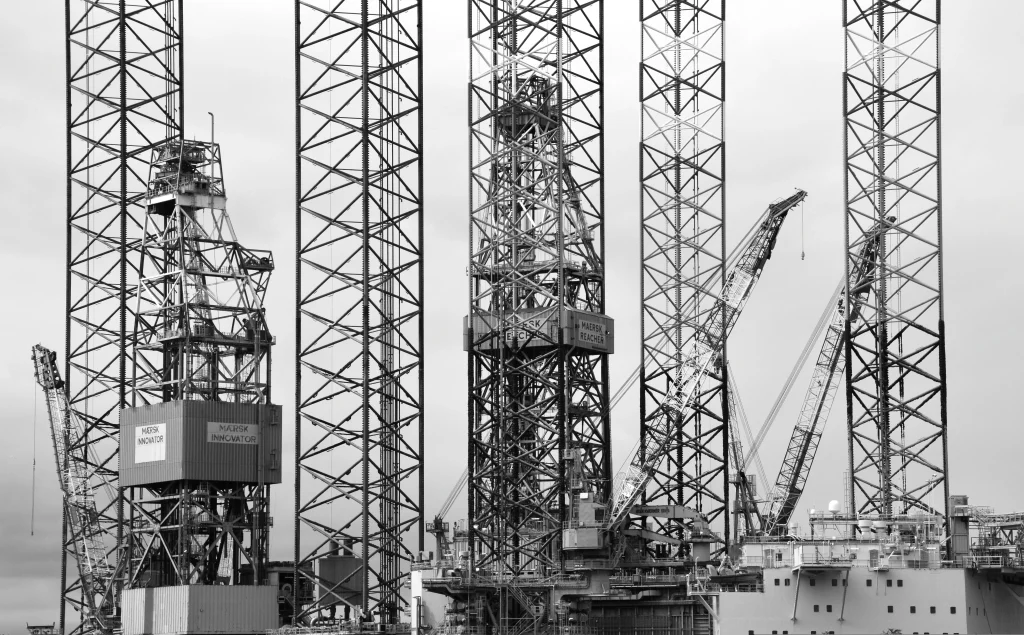
5. Medical Equipment
Medical devices require impeccable precision, and laser metal cutting is the perfect fit for creating surgical instruments, prosthetics, and implantable components.
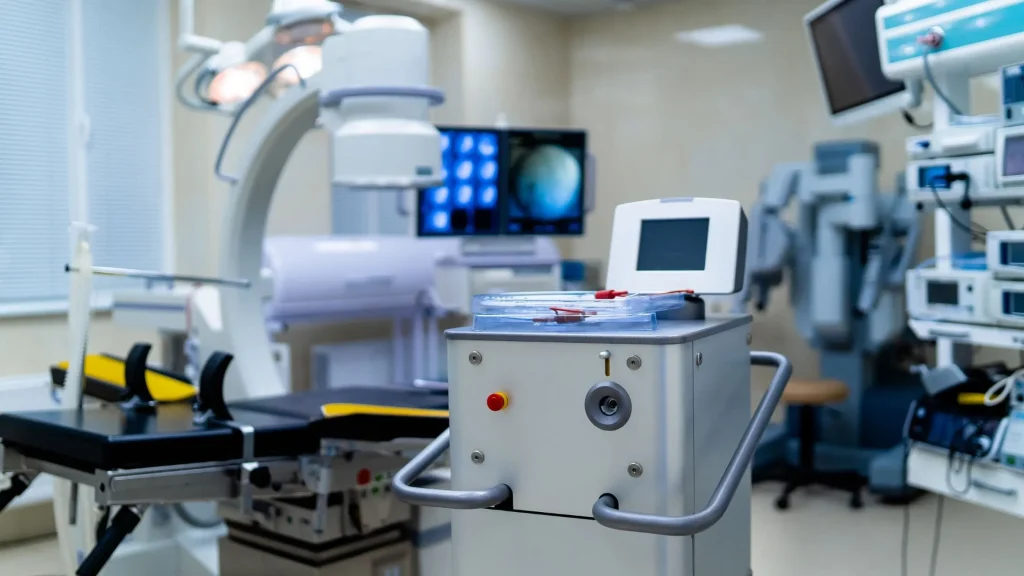
6. Custom Art and Signage
Artists and businesses leverage laser cutting to create unique sculptures, decorative pieces, and signage, combining creativity with technological precision.
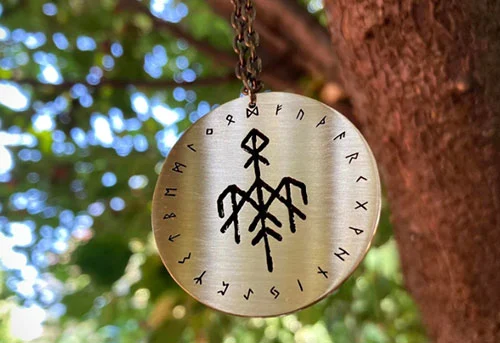
4.How Laser Metal Cutting Works: A Step-by-Step Process
1. Design Creation
The journey begins with a digital design file, often created in CAD software. This file defines the cutting path, ensuring every detail is accounted for.
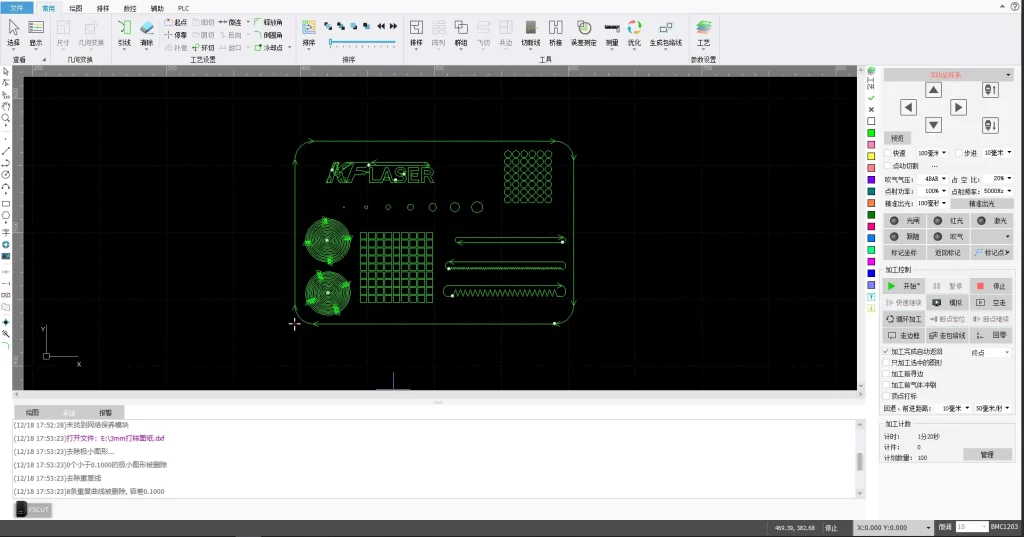
2. Material Selection
Choosing the right metal is crucial. Factors like thickness, reflectivity, and strength influence the laser’s settings and cutting process.
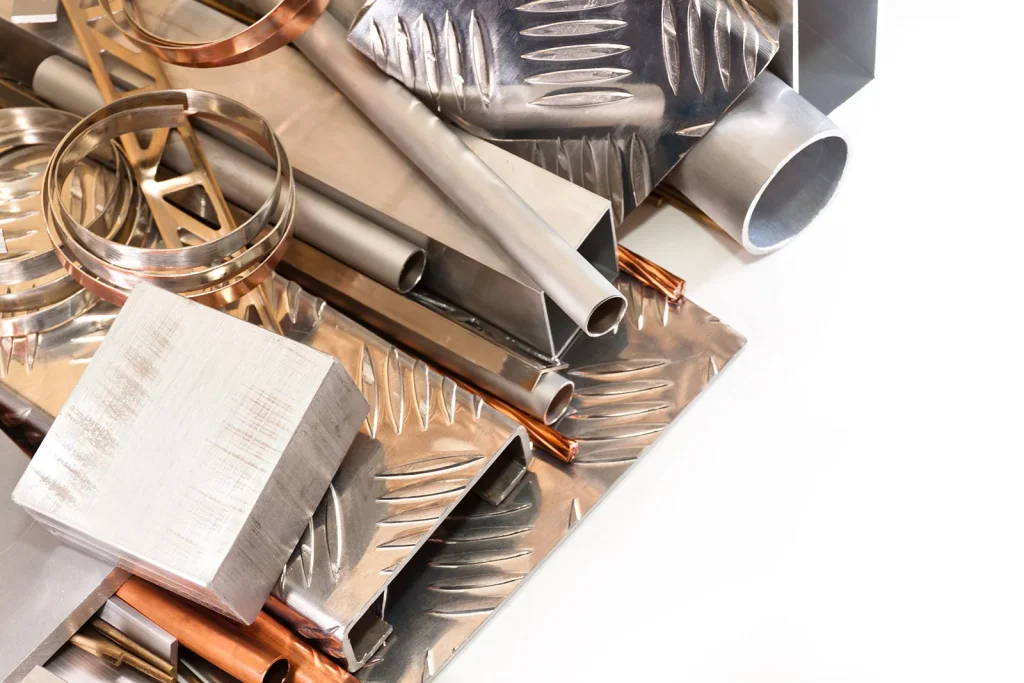
3. Laser Setup
The laser cutter is configured based on the material and design requirements. Parameters like beam intensity, speed, and assist gas flow are adjusted to optimize performance.
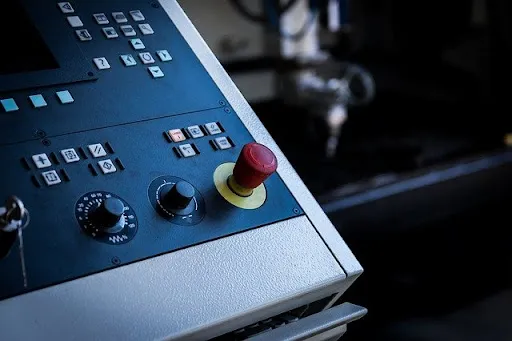
4. Cutting Process
The laser beam focuses on the metal surface, rapidly heating and vaporizing it along the cutting path. Assist gases clear debris and enhance the quality of the cut.
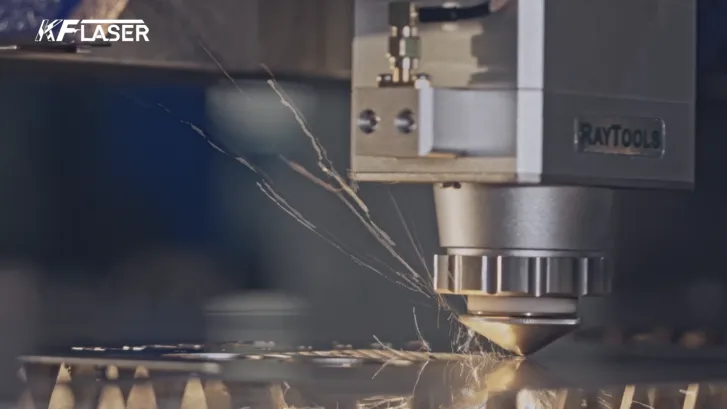
5. Quality Assurance
After cutting, the product undergoes inspection to ensure it meets design specifications. Minimal finishing is required due to the precision of the laser process.
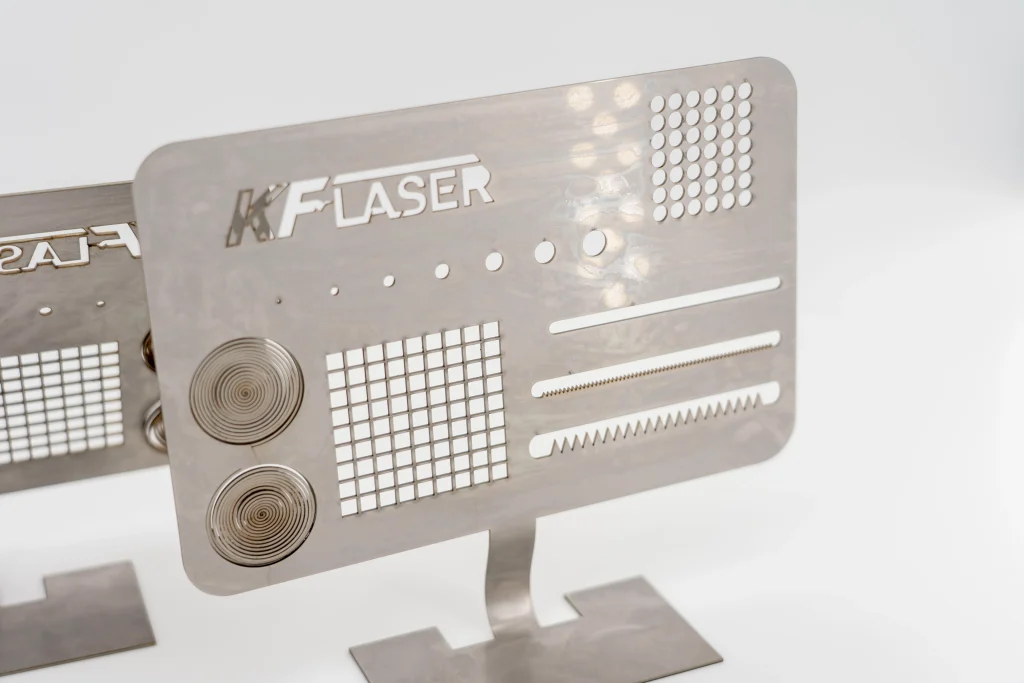
5.Advantages of Laser Metal Cutting Over Traditional Methods
1. Superior Edge Quality
Unlike mechanical cutting tools, laser cutting leaves smooth, burr-free edges, reducing the need for post-processing.
2. High Repeatability
Once programmed, laser cutters can replicate the same design with consistent quality, making them ideal for mass production.
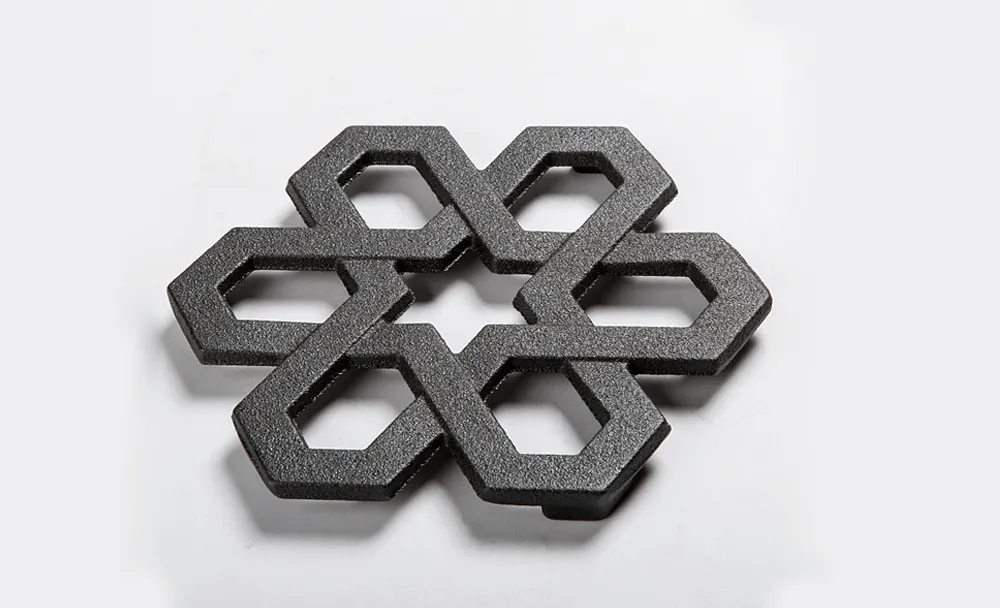
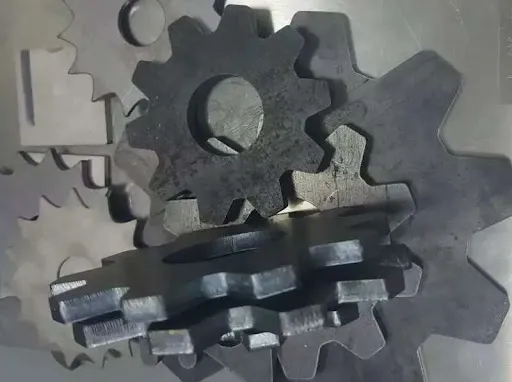
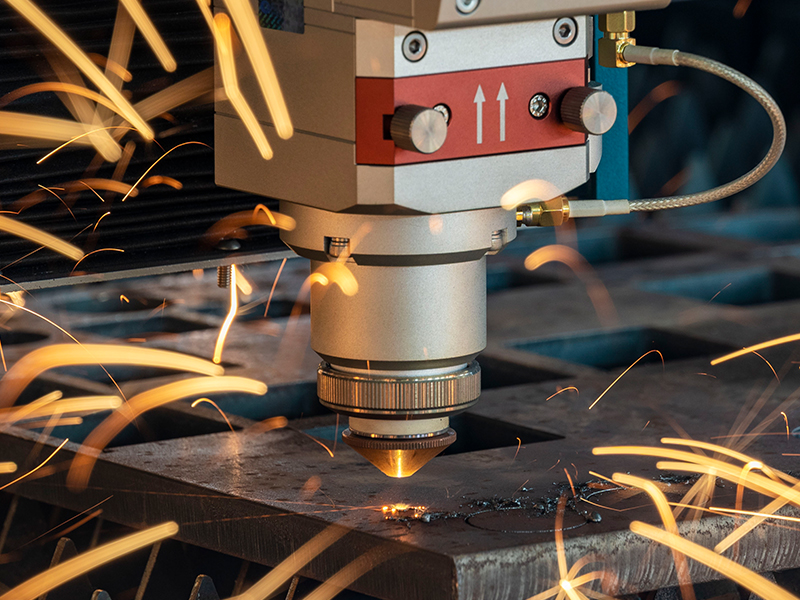
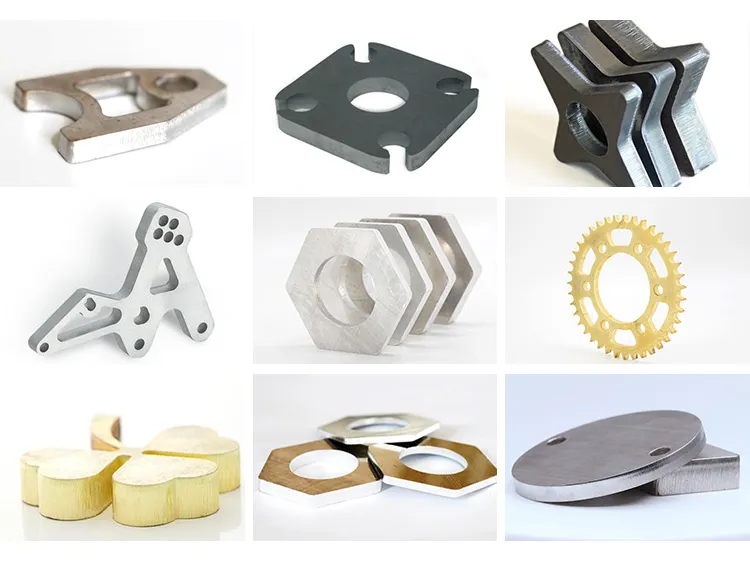
6.Challenges and Solutions in Laser Metal Cutting
1. Reflective Materials
Metals like aluminum and copper can reflect the laser beam, reducing efficiency. Modern laser systems, however, incorporate anti-reflective technologies to overcome this challenge.
2. Material Thickness
Cutting very thick metals requires higher laser power, which can increase costs. Advanced systems optimize power usage to maintain efficiency without sacrificing quality.
3. Operating Costs
While the initial investment in a laser cutting machine can be high, its long-term cost savings in reduced waste, maintenance, and labor outweigh the upfront expense.
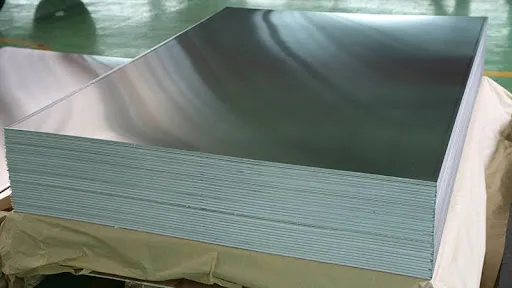
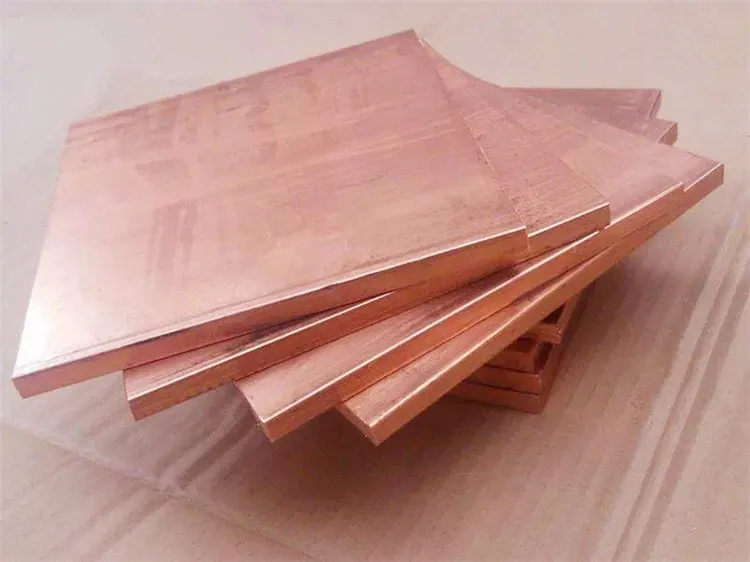
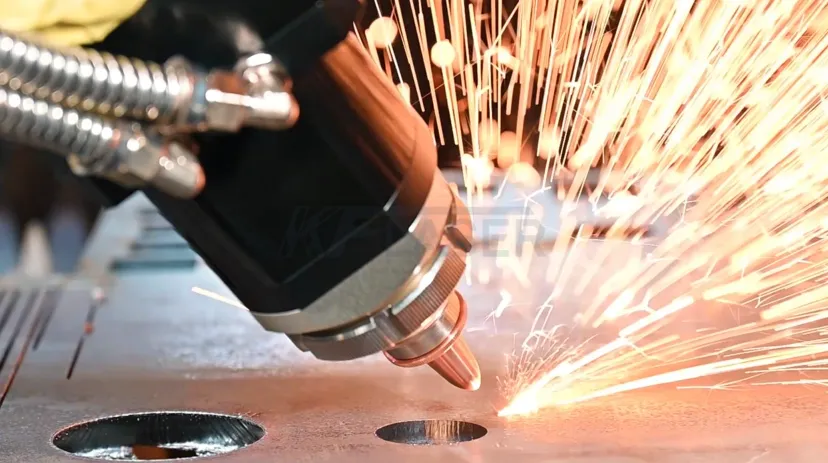

7.The Role of KF LASER in Advancing Laser Metal Cutting
KF LASER has established itself as a leader in laser cutting technology, offering systems that combine precision, efficiency, and reliability. Their machines cater to diverse industries, providing solutions tailored to specific cutting needs.
8.The Future of Laser Metal Cutting
1. AI-Driven Optimization
Artificial Intelligence is set to revolutionize laser cutting, enabling real-time adjustments, predictive maintenance, and enhanced efficiency.
2. Expanded Material Capabilities
Future advancements will allow lasers to cut an even broader range of materials, including advanced alloys and composite metals.
3. Portable and Compact Machines
As technology evolves, smaller, more accessible laser cutting systems will empower small businesses and hobbyists.
4. Sustainable Manufacturing
Laser cutting will continue to align with eco-friendly practices, emphasizing energy efficiency and waste reduction.
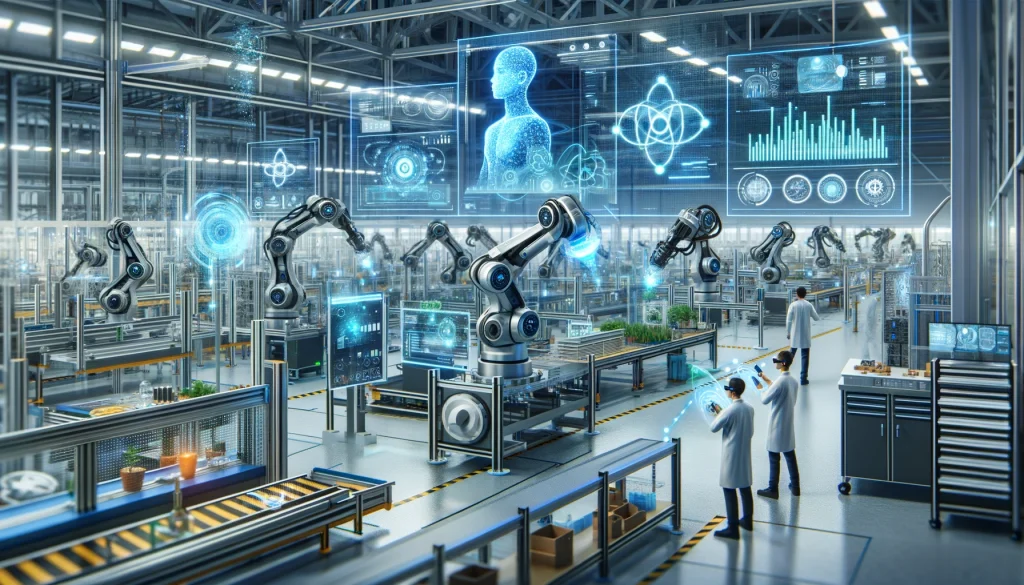
9.How to Choose the Right Laser Cutter for Metal
1. Material Requirements
Consider the types and thicknesses of metal you’ll be cutting. Ensure the machine’s power output matches your needs.
2. Cutting Speed
High-speed systems are ideal for mass production, while slower machines may be suitable for intricate designs.
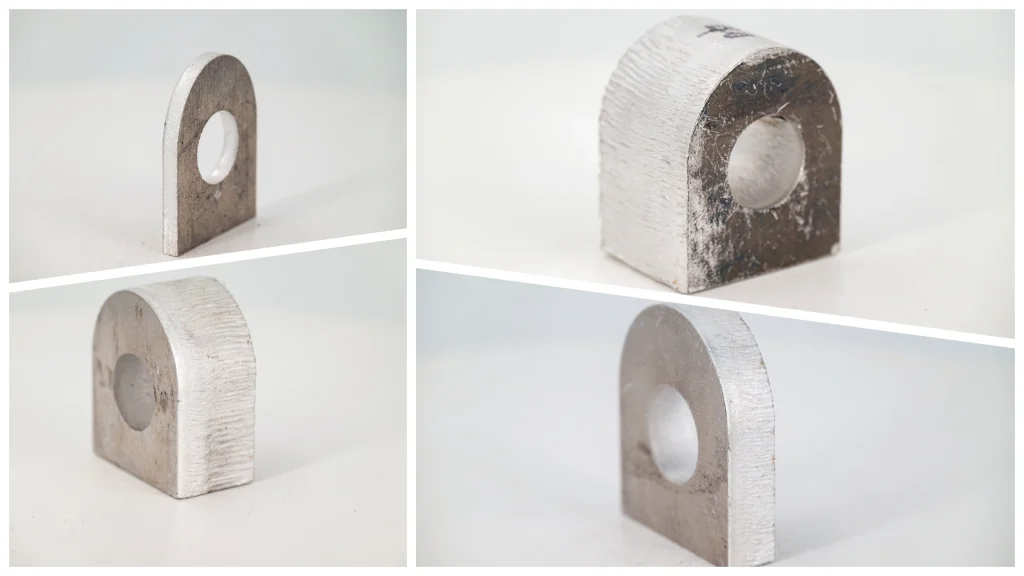
3. Software Integration
Choose a laser cutter with intuitive software that supports CAD files and allows for customization.
4. Maintenance and Support
Partner with a trusted provider like KF LASER to ensure ongoing support and reliable performance.
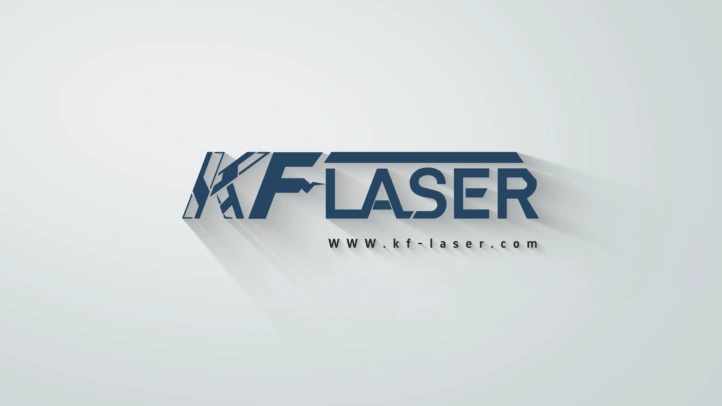
10.Conclusion: The Precision of Light, The Power of Metal
Laser metal cutting is more than just a technological process; it’s a revolution in precision, efficiency, and versatility. From crafting aerospace components to creating custom art, this technology empowers industries to push boundaries and achieve excellence.
With KF LASER, you’re not just investing in cutting-edge technology; you’re embracing a future where creativity and precision converge. Discover the limitless possibilities of laser metal cutting and take your projects to the next level. The future of fabrication is here—light the way.
Top Stories
-
Laser Cutting Aluminum Tube: Techniques and Benefits Explained06 Sep 2025
-
Laser Cutting Aluminum with Oxygen: Boosting Precision and Efficiency05 Sep 2025
-
Efficient Laser Cutting Machine for Brass Sheet: Enhance Your Precision Cutting04 Sep 2025
-
Laser Cutting Machine Sheet: The Key to Precision and Efficiency in Modern Manufacturing02 Sep 2025
-
Laser Cutting Stainless Steel with Oxygen: Revolutionizing the Cutting Process31 Aug 2025
Product Categories
- Metal Laser Cutter
- Laser Welder Machine
- Laser Cleaner Machine
- Laser Marker Machine
- Press Brake Machine