Noticias
Máquina de cortar láser de tubo de metal: El futuro de la fabricación de metal de precisión
The metal tube laser cutting machine is an advanced technological marvel that is reshaping industries worldwide. Its ability to cut metal tubes with extreme precision and speed is revolutionizing fabrication processes in sectors ranging from aerospace to automotive, medical, and beyond. En este artículo, we will dive deep into how this cutting-edge technology works, its numerous benefits, and why it is becoming the go-to tool for high-quality, efficient metal tube cutting.
1. What is a Metal Tube Laser Cutting Machine?
A metal tube laser cutting machine uses a high-powered laser beam to cut and shape metal tubes. The laser’s focused light energy is directed onto the metal, where it melts or vaporizes the material, with an assist gas blowing away the melted residue. This non-contact process allows for precision cuts without any physical contact between the tool and the material.
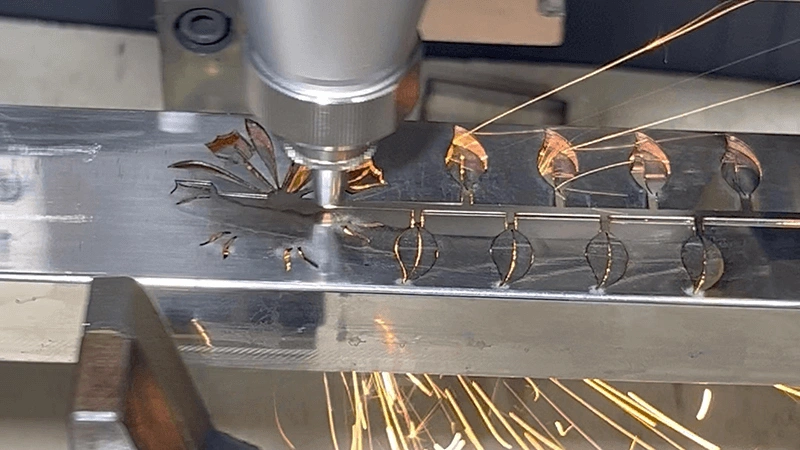
Laser cutting is renowned for its speed, precisión, y versatilidad, and when applied to metal tube cutting, it provides the ability to cut complex shapes and designs with minimal waste. Whether you’re working with steel, aluminio, or other metals, laser cutting technology ensures clean, sharp edges without the need for additional finishing.
2. How Does a Metal Tube Laser Cutting Machine Work?
The operation of a metal tube laser cutting machine is a sophisticated process that combines laser physics with precise engineering. Below is a simplified explanation of the key steps involved:
● Laser Generation
The laser beam is generated by a laser source, typically a fiber laser or CO2 laser. Fiber lasers are increasingly preferred for tube cutting due to their efficiency and ability to produce a smaller beam spot size, which is ideal for high-precision work.
● Beam Delivery and Focusing
Once the laser is generated, it is transported through fiber optic cables to the cutting head, where it is precisely focused. The diameter of the laser beam is reduced to a fraction of a millimeter, which allows for extremely fine, detailed cuts. The laser beam can also be manipulated to move along multiple axes, providing dynamic cutting capabilities.
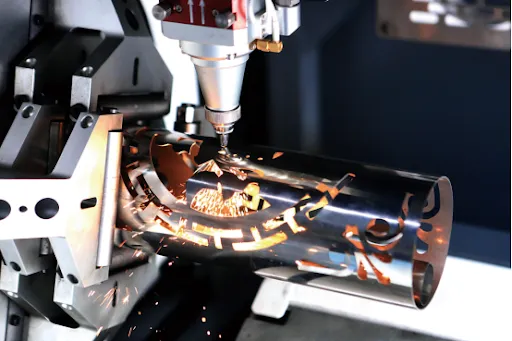
▲ The above video is of KF Laser TS series laser tube cutting machine. You can also click here to enter the Láser KF YOUTUBE homepage.
● Cutting Process
The laser beam is directed onto the tube’s surface, rapidly heating it to the point where the material melts or evaporates. The high-pressure gas—such as nitrogen or oxygen—is then directed onto the cutting area to blow away the molten metal, leaving behind a clean cut.
● Edge Formation
One of the standout features of the metal tube laser cutting machine is the smooth, burr-free edges it produces. The precise nature of the laser reduces material distortion and avoids the need for additional finishing, resulting in a higher-quality final product.
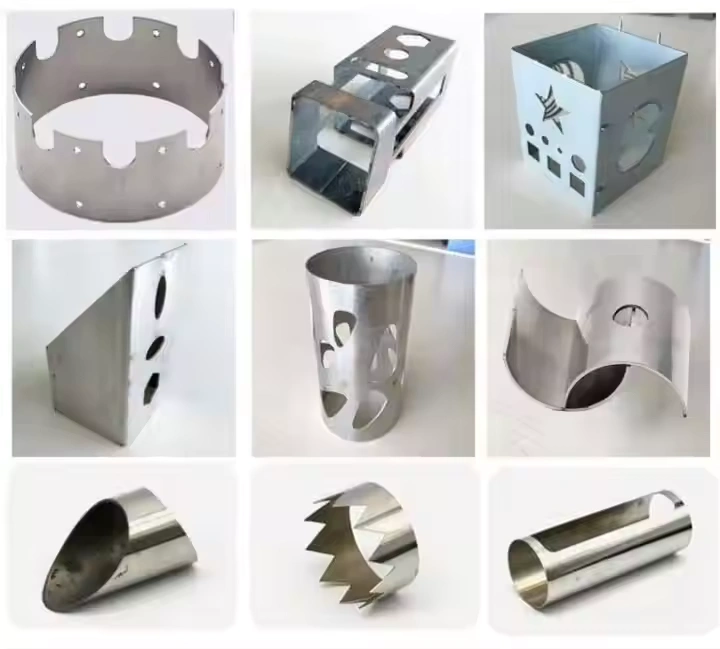
3. Benefits of Using a Metal Tube Laser Cutting Machine
There are several reasons why the metal tube laser cutting machine is rapidly becoming the preferred choice for many industries. Some of the key benefits include:
● High Precision and Accuracy
The laser cutting process offers unparalleled precision, enabling manufacturers to create intricate and complex tube shapes with high accuracy. This is crucial for industries like aerospace, automotor, and medical device manufacturing, where the slightest deviation can affect functionality and safety.
● Flexibility and Versatility
Laser cutting machines can handle a wide variety of materials, incluyendo acero inoxidable, aluminio, latón, y titanio. They also provide the flexibility to cut different types of tubes, such as round, square, rectangular, and oval shapes, with ease.
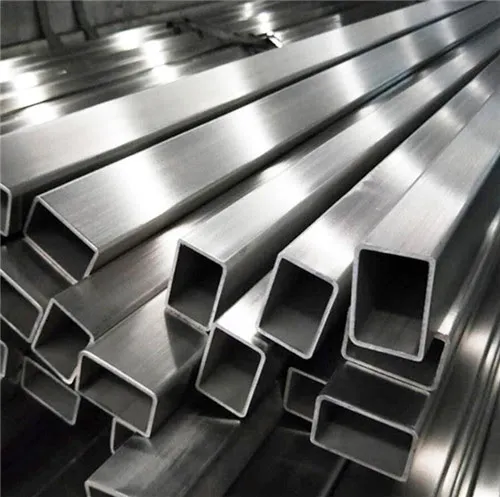
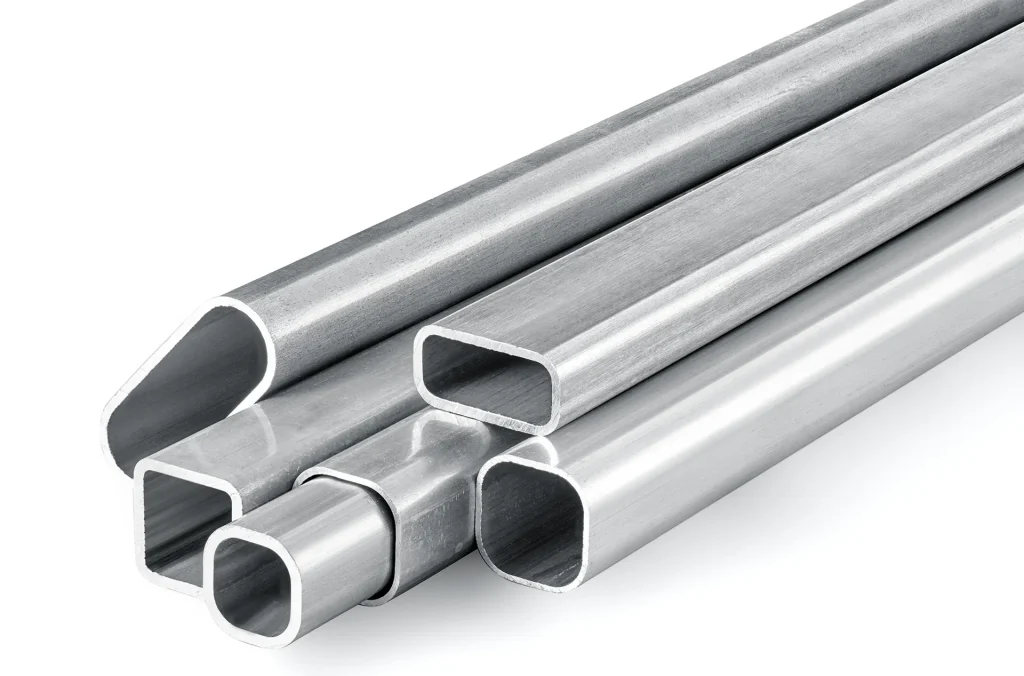
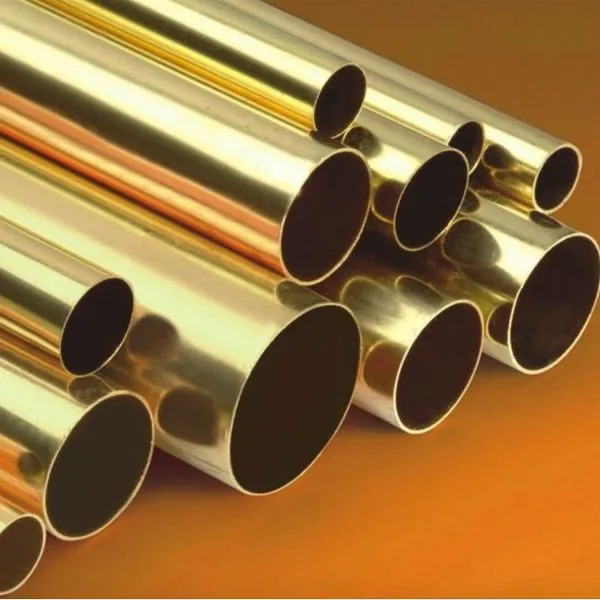
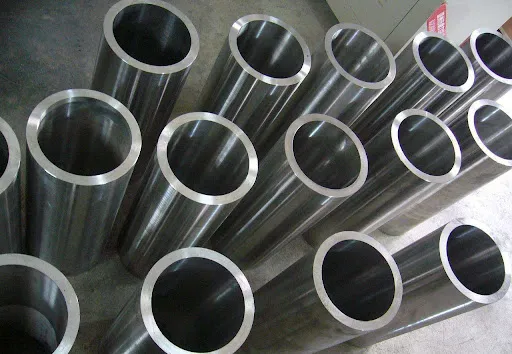
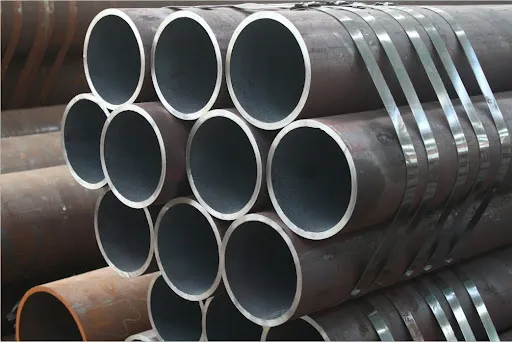
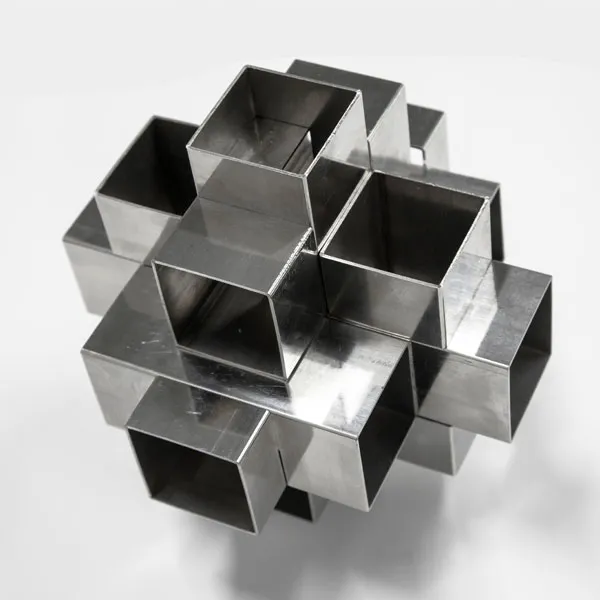
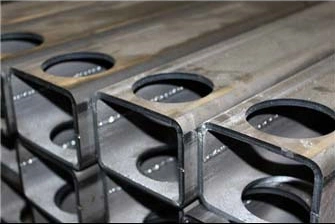
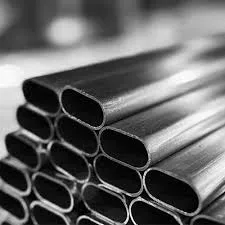
● Faster Production Times
Compared to traditional cutting methods, laser cutting significantly speeds up the process. With the ability to perform high-speed, high-quality cuts, manufacturers can reduce production lead times and meet tight deadlines more effectively.
● Reduced Material Waste
Laser cutting is a highly efficient process that results in minimal material waste. Because the laser beam is so precise, it cuts metal tubes with minimal kerf (the width of the cut), leaving more usable material behind compared to other methods.
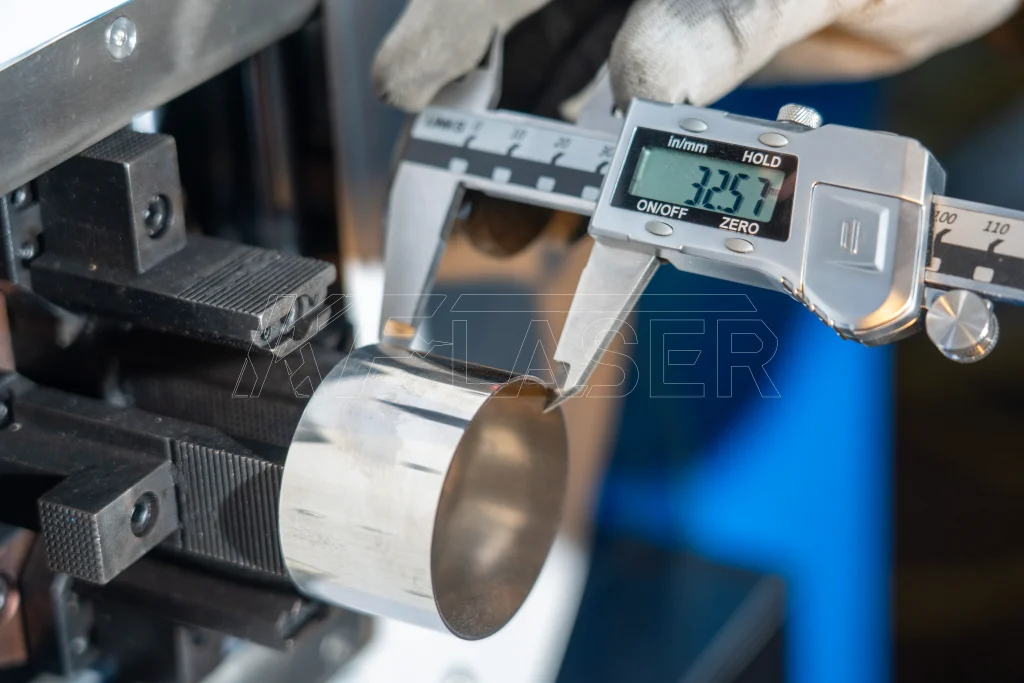
● No Tool Wear
Unlike mechanical cutting processes, laser cutting does not involve direct physical contact with the material. This eliminates tool wear, which can lead to increased maintenance and downtime in other cutting methods. With a laser cutting machine, there’s no need for regular tool replacement.
4. Applications of Metal Tube Laser Cutting Machines
Laser cutting technology is used across many different industries due to its ability to cut tubes with high precision. Here are some of the major industries benefiting from this technology:
● Aerospace
En la industria aeroespacial, where precision is non-negotiable, metal tube laser cutting machines are used to cut titanium and aluminum tubes for aircraft parts. These materials need to be cut with extreme accuracy to ensure the safety and performance of the aircraft.
● Automotive
The automotive industry uses laser cutting for the production of exhaust systems, structural components, and other parts that require tight tolerances. The ability to cut complex tube shapes is crucial for the manufacture of custom or performance parts.
● Medical Devices
Medical device manufacturers rely on laser cutting for components such as implants, herramientas quirúrgicas, and medical tubing. The precision of the laser ensures that even the smallest components are manufactured to exact specifications.
● Industrial Equipment
Laser cutting is used extensively in the manufacturing of industrial equipment, including machinery frames, pipelines, y componentes estructurales. The ability to cut thick and thin metal tubes efficiently makes laser cutting machines a vital part of industrial manufacturing processes.
● Furniture Design and Architecture
Laser cutting is not only used for functional parts but also for decorative purposes. The ability to create intricate designs in metal tubes has made laser cutting a popular choice in architecture, furniture design, and artistic applications.
5. Key Factors to Consider When Choosing a Metal Tube Laser Cutting Machine
Selecting the right metal tube laser cutting machine for your business depends on several factors. Here are the most important considerations to keep in mind:
● Laser Power
The power of the laser will determine the thickness of the metal tubes you can cut. A higher-power laser is necessary for cutting thicker materials, while a lower-power laser can handle thinner tubes with precision.
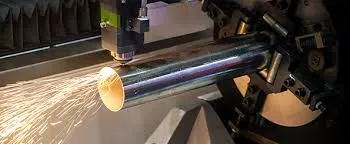
● Cutting Speed
Cutting speed is an essential factor for productivity. Faster cutting speeds increase throughput and reduce production times. Sin embargo, it’s important to balance speed with the quality of the cut to ensure the final product meets specifications.
● Machine Automation
Modern laser cutting machines come with automated features, such as automatic loading and unloading systems, to increase efficiency and reduce manual labor. Consider how much automation your production line requires.
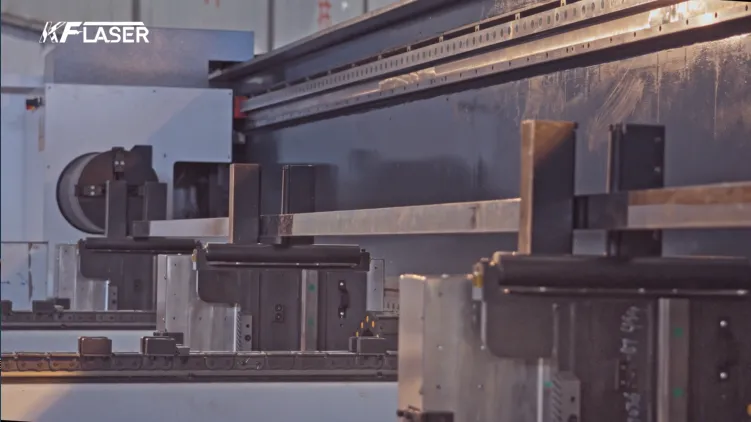
● Maintenance and Support
Regular maintenance ensures that your laser cutting machine runs smoothly and lasts longer. Choose a machine that is easy to maintain and comes with reliable support from the manufacturer to avoid downtime and costly repairs.
6. How Metal Tube Laser Cutting Machines Compare to Other Cutting Methods
● Laser Cutting vs. Plasma Cutting
While plasma cutting is often faster and more cost-effective for thicker materials, it produces rougher edges than laser cutting. Laser cutting, por otro lado, provides cleaner cuts with less heat distortion, making it ideal for high-precision applications.
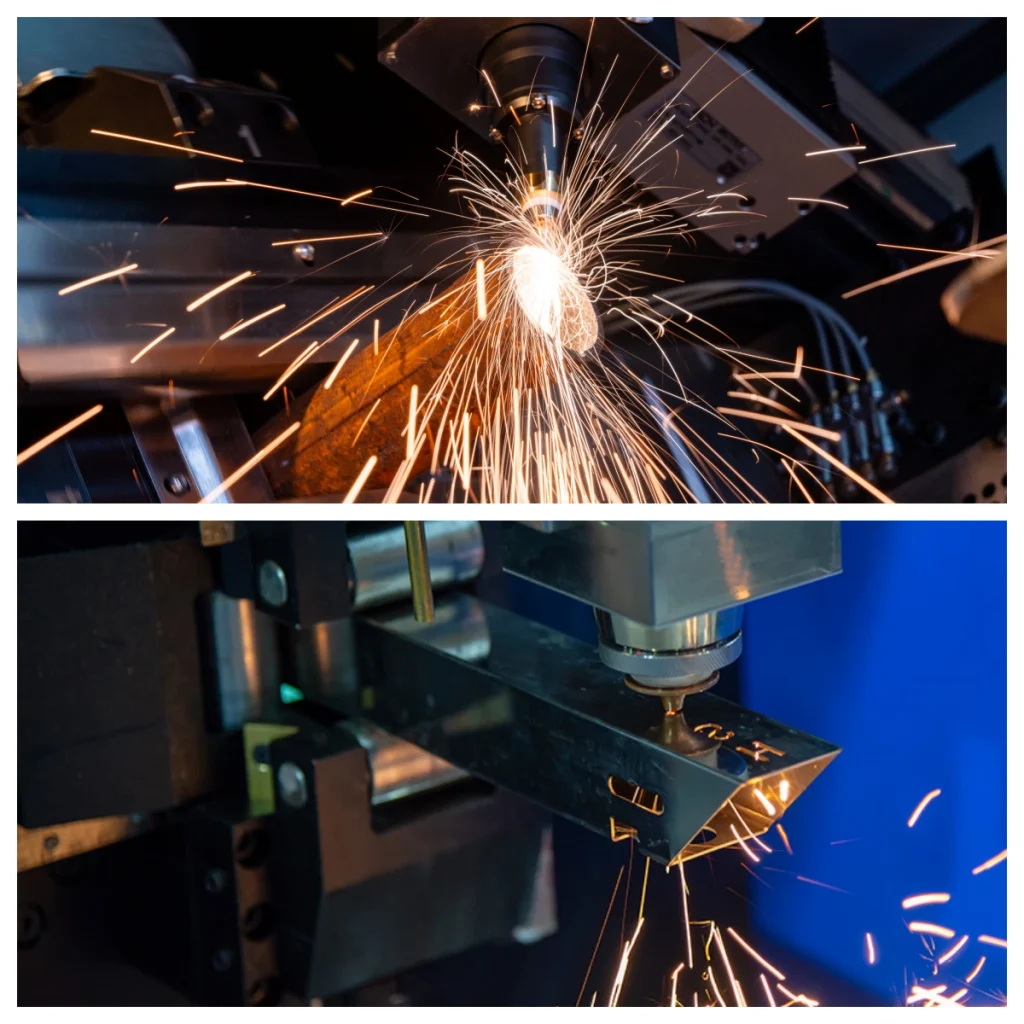
● Laser Cutting vs. Waterjet Cutting
Waterjet cutting is effective for cutting a wide range of materials, but it is slower and produces larger kerf widths compared to laser cutting. The absence of heat in waterjet cutting is beneficial for some materials, but for metal tubes, laser cutting offers superior precision.
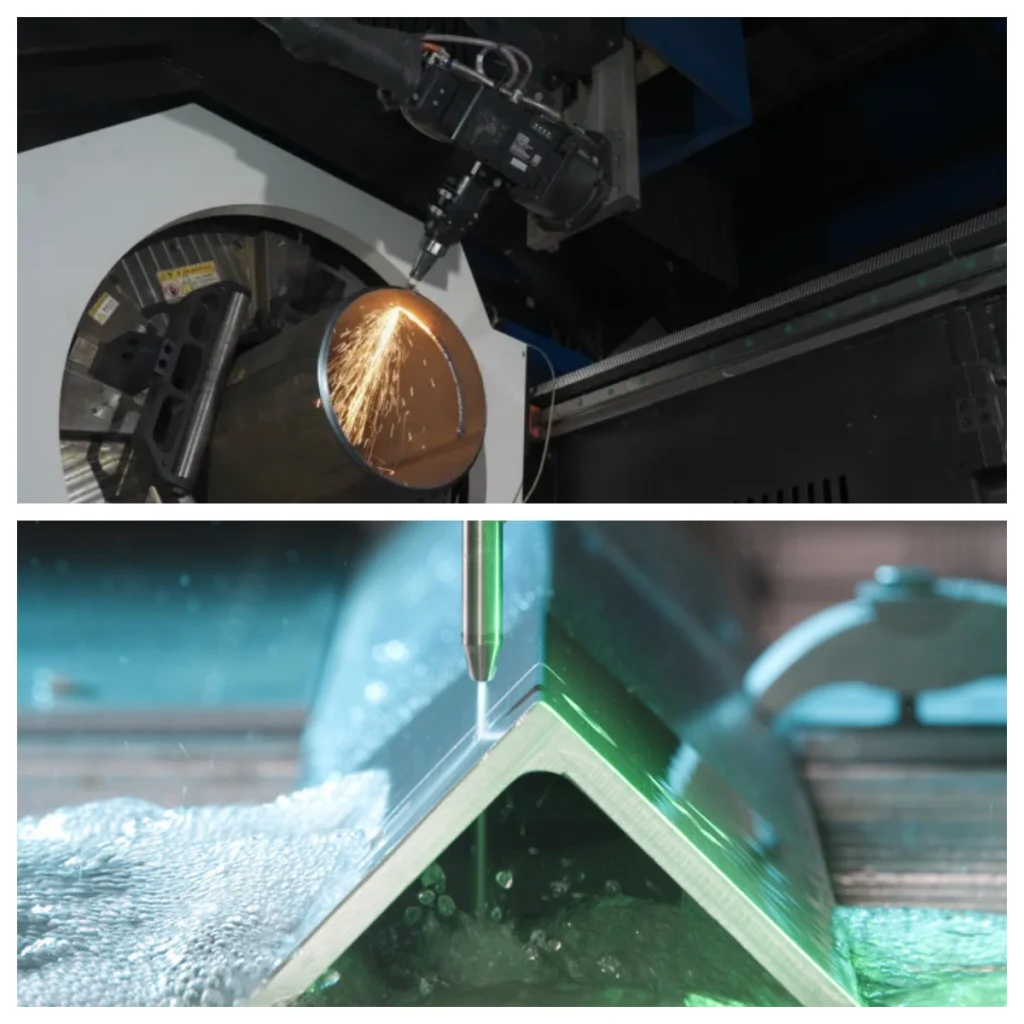
● Laser Cutting vs. Mechanical Cutting
Mechanical cutting methods like sawing and shearing involve direct contact with the material, which can lead to tool wear and material distortion. Laser cutting, by contrast, is a non-contact method that produces smoother cuts with fewer defects.
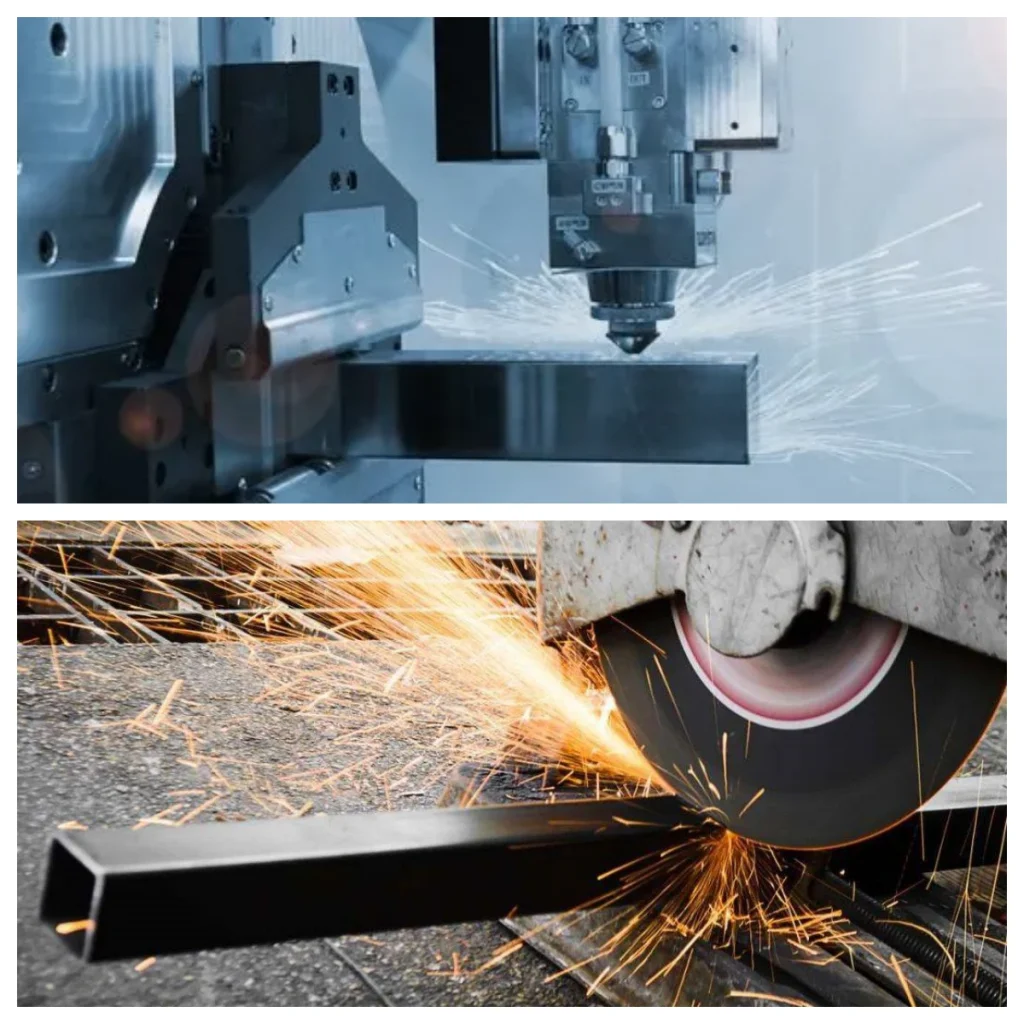
The metal tube laser cutting machine has become a vital tool for industries seeking precision, eficiencia, y versatilidad. With its ability to cut metal tubes of various sizes and materials with unmatched accuracy, it is clear why laser cutting is a preferred choice in modern manufacturing. Whether you’re producing parts for the automotive, aeroespacial, or medical industries, investing in a high-quality laser cutting machine is a step toward achieving superior results in less time.
Historias destacadas
-
Laser Cutting Aluminum Tube: Techniques and Benefits Explained06 Sep 2025
-
Láser cortando aluminio con oxígeno: Aumento de la precisión y la eficiencia05 Sep 2025
-
Máquina de cortar láser eficiente para la hoja de latón: Mejora tu corte de precisión04 Sep 2025
-
Hoja de máquina de corte láser: La clave para la precisión y la eficiencia en la fabricación moderna02 Sep 2025
-
Corte láser de acero inoxidable con oxígeno: Revolución del proceso de corte31 Ago 2025
Categorías de productos
- Cortador láser de metales
- Máquina soldadora láser
- Máquina limpiadora láser
- Máquina marcadora láser
- Prensa plegadora