Noticias
Máquina de cortar tubo láser CNC: La solución de vanguardia para la fabricación de metal de precisión
The CNC laser tube cutting machine has emerged as one of the most powerful and versatile tools in the field of metal fabrication. With the ability to cut tubes and pipes made from various materials like steel, acero inoxidable, aluminio, y cobre, this advanced technology has quickly become the preferred choice for industries demanding high precision and efficiency. From automotive to aerospace, medical devices to construction, the laser tube cutting machine is playing a pivotal role in transforming the manufacturing process.
1. Understanding CNC Laser Tube Cutting Technology
En su núcleo, the CNC laser tube cutting machine uses a high-powered laser beam that is focused on the material to cut through it. What makes this technology distinct is its use of Computer Numerical Control (CNC), which allows for precise control of the laser’s movements and cutting paths. This precision leads to clean, smooth cuts, which are ideal for complex designs that traditional cutting methods struggle to achieve.
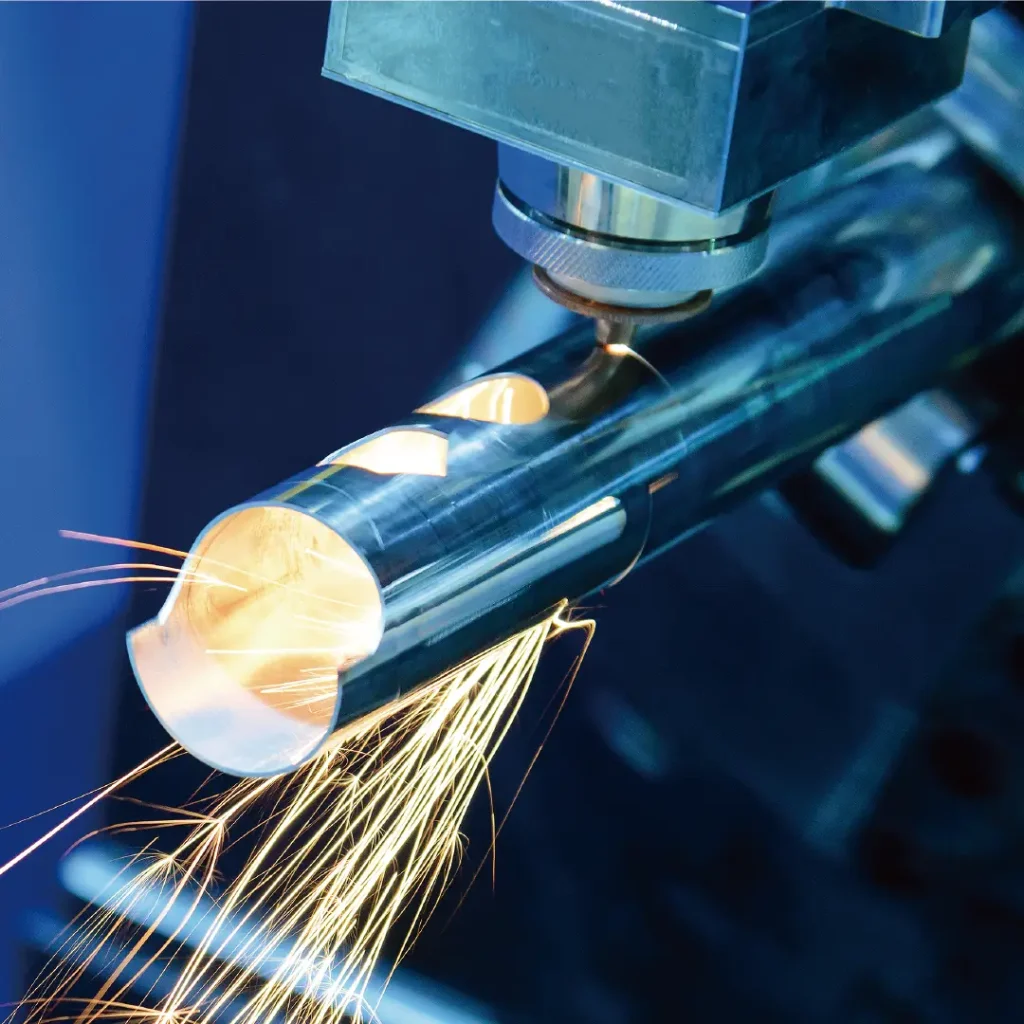
The key advantage of using a laser over mechanical tools is the non-contact nature of the process. There is no physical wear and tear on the cutting tool, and the cutting quality remains consistent throughout the operation, even for longer runs.
2. How CNC Laser Tube Cutting Machines Work
◑ Laser Generation and Focus
The laser beam used in CNC laser cutting machines is typically generated by a fiber laser source. The fiber laser is known for its efficiency and ability to deliver a more concentrated beam compared to other types, making it ideal for precision cutting. The generated laser beam is transported via fiber optics to the cutting head, where it is focused onto the material.
◑ Interacción material
As the focused laser beam strikes the metal tube, it heats the material to a point where it melts, vaporizes, or blows away, depending on the chosen parameters. Assist gases, such as nitrogen or oxygen, are blown through the nozzle at high pressure, helping to clear the molten metal and achieve clean edges.
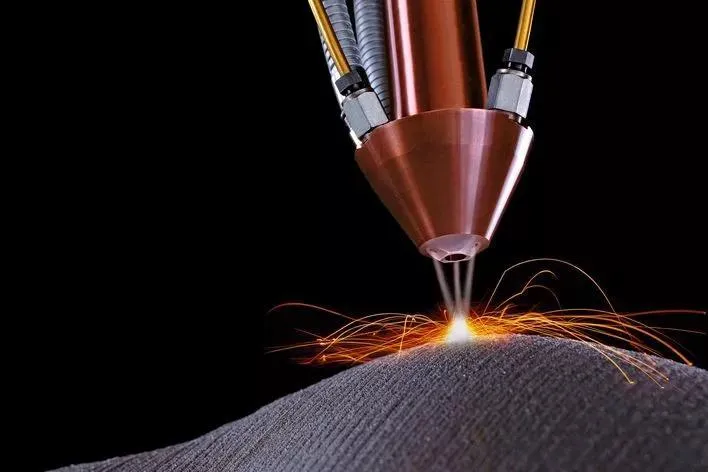
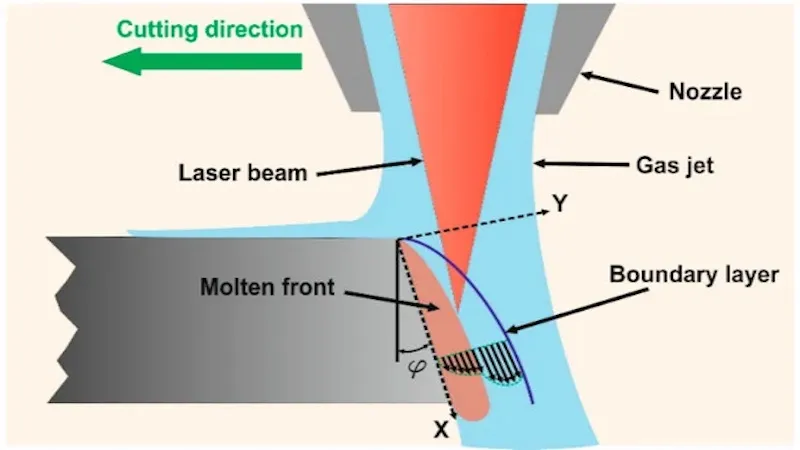
◑ CNC Control
CNC control systems are employed to direct the laser’s path along the metal tube. This allows for intricate patterns, bevels, holes, and other complex shapes to be cut with high precision. The CNC system also allows the machine to be automated, reducing the need for human intervention and minimizing errors in the cutting process.
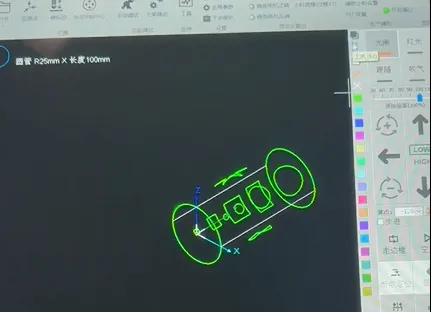
3. Key Advantages of CNC Laser Tube Cutting Machines
The introduction of CNC laser tube cutting machines has provided significant improvements over traditional cutting methods. Here are some of the most notable advantages:
◑ Alta precisión y exactitud
The primary advantage of CNC laser cutting is its high level of accuracy. With a laser cutting system, you can achieve tolerances as tight as +/-0.1mm, ensuring that each part is produced to exact specifications. This level of precision is particularly critical in industries where even a small deviation could lead to failure, such as aerospace or medical device manufacturing.
◑ Velocidad y eficiencia
Laser cutting machines are highly efficient, enabling manufacturers to complete jobs much faster than with traditional cutting methods. The CNC system automates the cutting process, resulting in quicker turnaround times and fewer manual labor requirements. Además, the precision of the machine means there’s minimal need for secondary operations such as deburring or sanding.
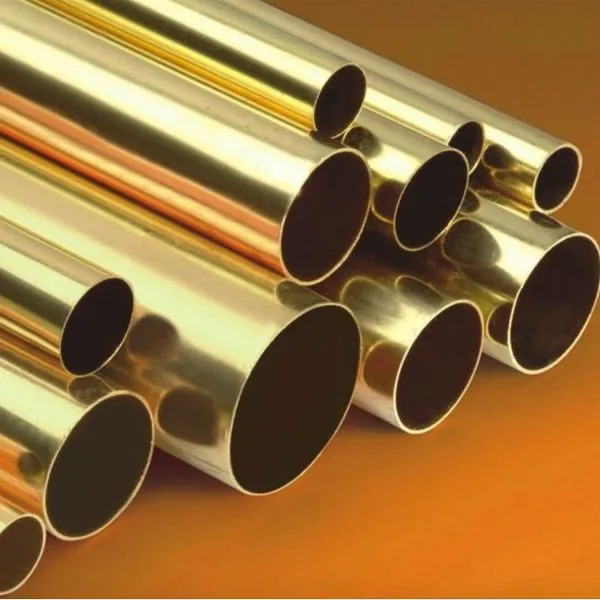
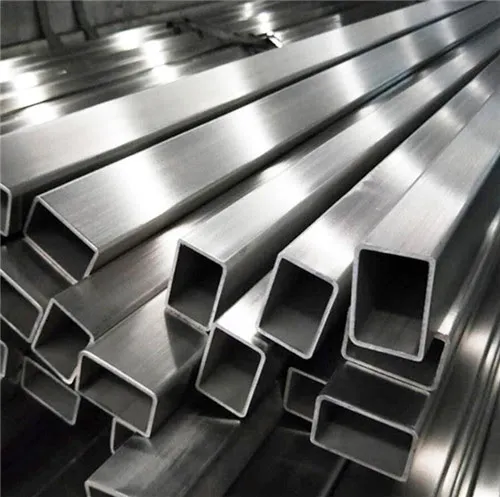
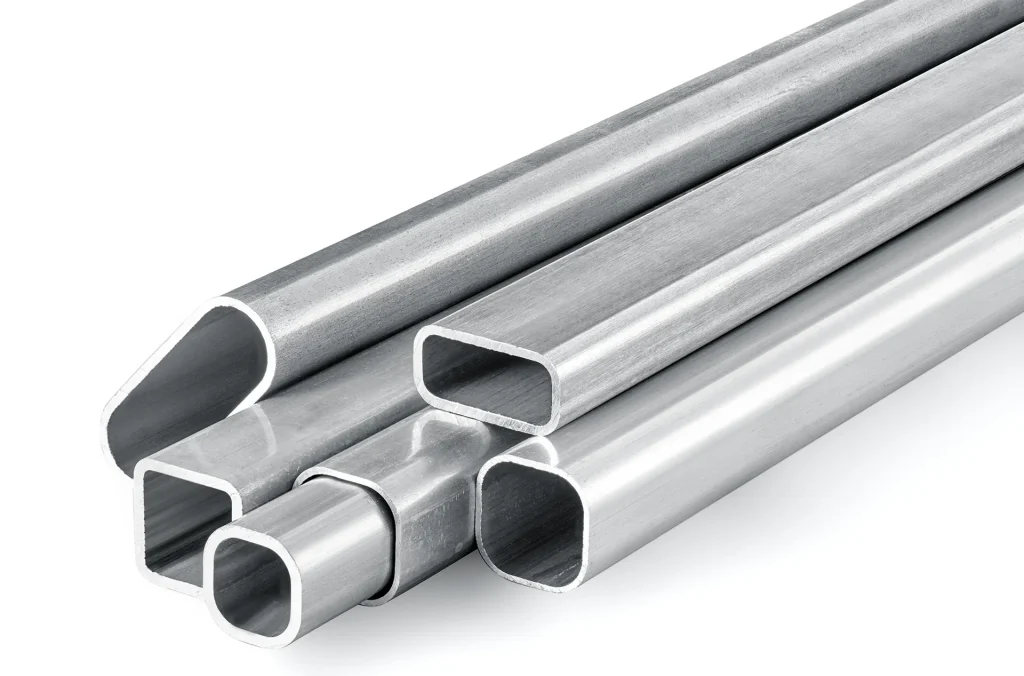
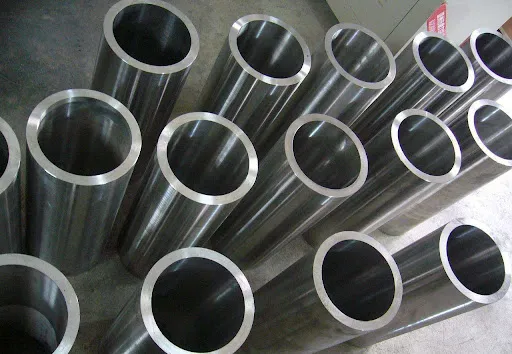
◑ Material Flexibility
CNC laser tube cutting machines can handle a wide range of materials. From standard mild steel to more challenging metals like titanium and alloys, these machines can cut through various thicknesses and diameters of metal tubes, making them suitable for diverse industries and applications.
◑ Desperdicio mínimo
Laser cutting produces very little waste compared to traditional cutting methods, such as saw cutting. The narrow kerf (width of the cut) ensures that less material is removed, allowing manufacturers to get more from their raw materials and lower production costs.
◑ Complex Cuts with Ease
Laser cutting allows for intricate cuts, including bevels, holes, slots, and even complex geometric patterns. This flexibility in cutting capability is a huge advantage for industries that require both functionality and aesthetics in their parts.
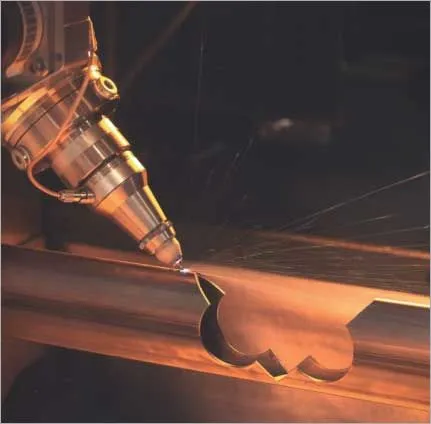
4. Common Applications of CNC Laser Tube Cutting Machines
◑ Automotive Industry
En la industria automotriz, CNC laser tube cutting machines are commonly used to manufacture parts such as exhaust systems, marcos, y otros componentes. The high precision of laser cutting ensures that these parts fit perfectly, contributing to the overall safety and efficiency of the vehicle.
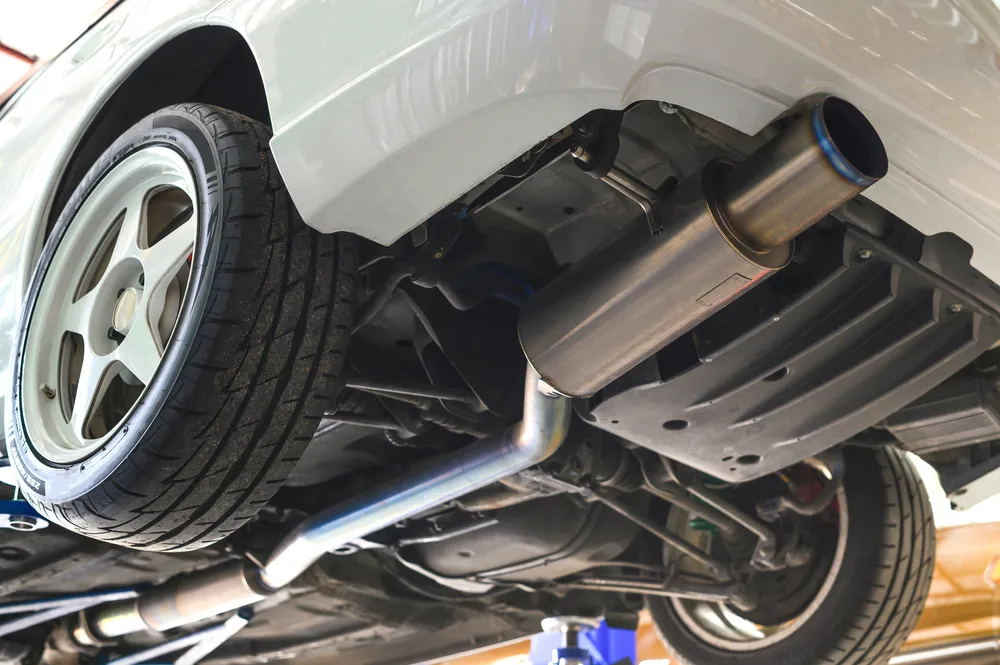
◑ Aerospace Manufacturing
Aerospace companies require high-precision components, and the CNC laser tube cutting machine delivers just that. From cutting fuel lines to creating support structures for aircraft, laser cutting technology is vital in producing parts that meet stringent aerospace standards.
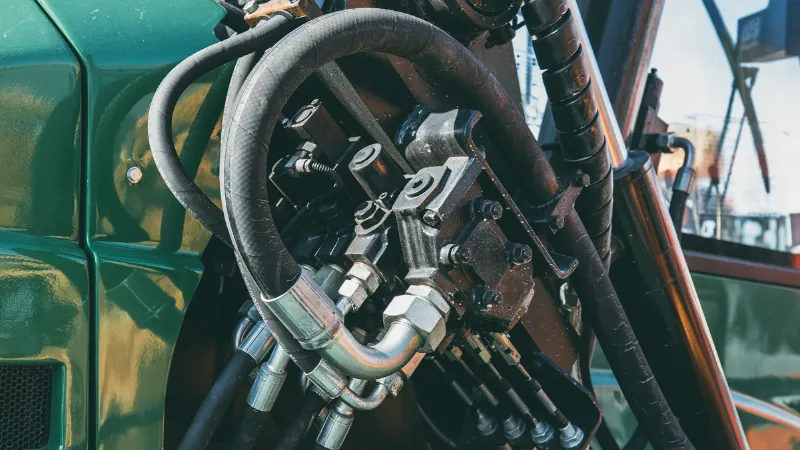
◑ Medical Devices
Medical device manufacturers use CNC laser tube cutting machines to produce implants, surgical instruments, and medical tubing. The need for sterilization and biocompatibility in medical devices makes it essential to use a technology that minimizes contamination and produces precise, high-quality cuts.
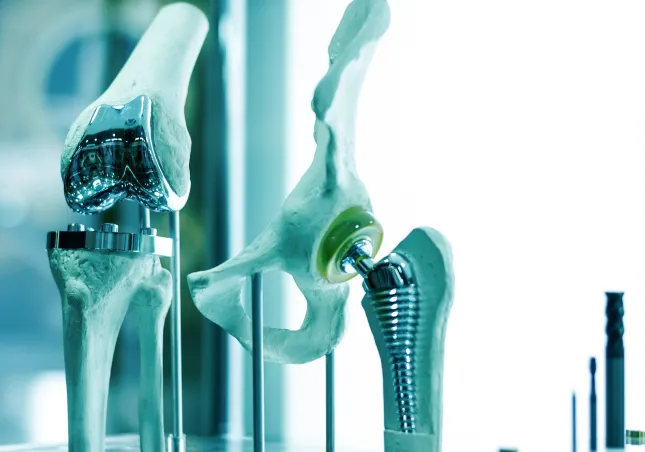
◑ Architectural Design
Laser cutting is also used in architectural applications, such as creating decorative metal elements for buildings or installations. The precision of the CNC laser tube cutter allows architects to incorporate intricate designs into their projects, making them both functional and visually appealing.
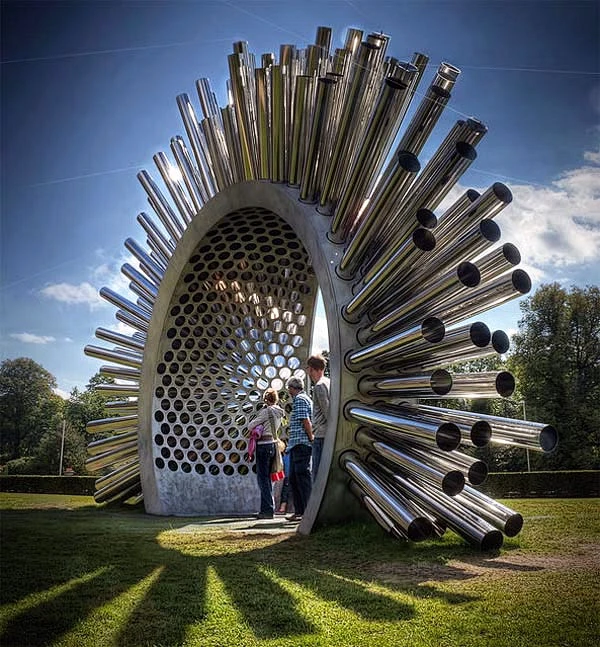
5. Factors to Consider When Choosing a CNC Laser Tube Cutting Machine
When selecting a CNC laser tube cutting machine, several factors must be considered to ensure the best fit for your production needs.
◑ Potencia del láser
The power of the laser determines the thickness of the material that can be cut. Higher-powered lasers are capable of cutting thicker materials, but they also require more energy and may result in higher operational costs. Be sure to match the laser power to your material thickness requirements.
◑ Cutting Speed and Precision
The cutting speed and precision are crucial considerations for high-volume production. While laser cutting is generally faster than traditional cutting methods, some machines may offer faster speeds or more precise cutting paths depending on the model.
◑ Tube Size and Geometry
Ensure that the CNC laser tube cutting machine you choose can accommodate the size and type of tubes you intend to cut. Many modern machines offer flexibility in handling various tube shapes, incluyendo ronda, square, rectangular, and even more complex geometries.
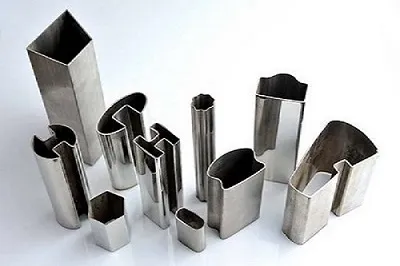
◑ Características de automatización
Many CNC laser tube cutting machines come with automated features, such as automatic tube loading, unloading, and even part sorting. These features can improve production efficiency and reduce labor costs, making them ideal for high-volume operations.
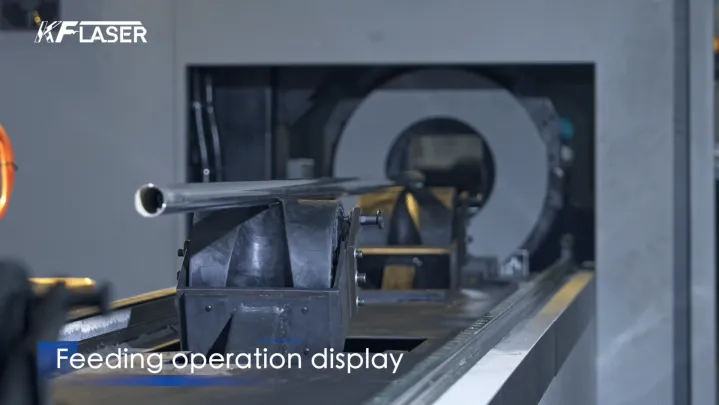
6. CNC Laser Tube Cutting Machine vs. Other Cutting Methods
◑ Laser Cutting vs. Plasma Cutting
While plasma cutting is fast and can handle thicker materials, it doesn’t offer the same precision or clean edges that laser cutting does. The heat affected zone (Cría) in plasma cutting is larger, which can lead to more distortion in the material.
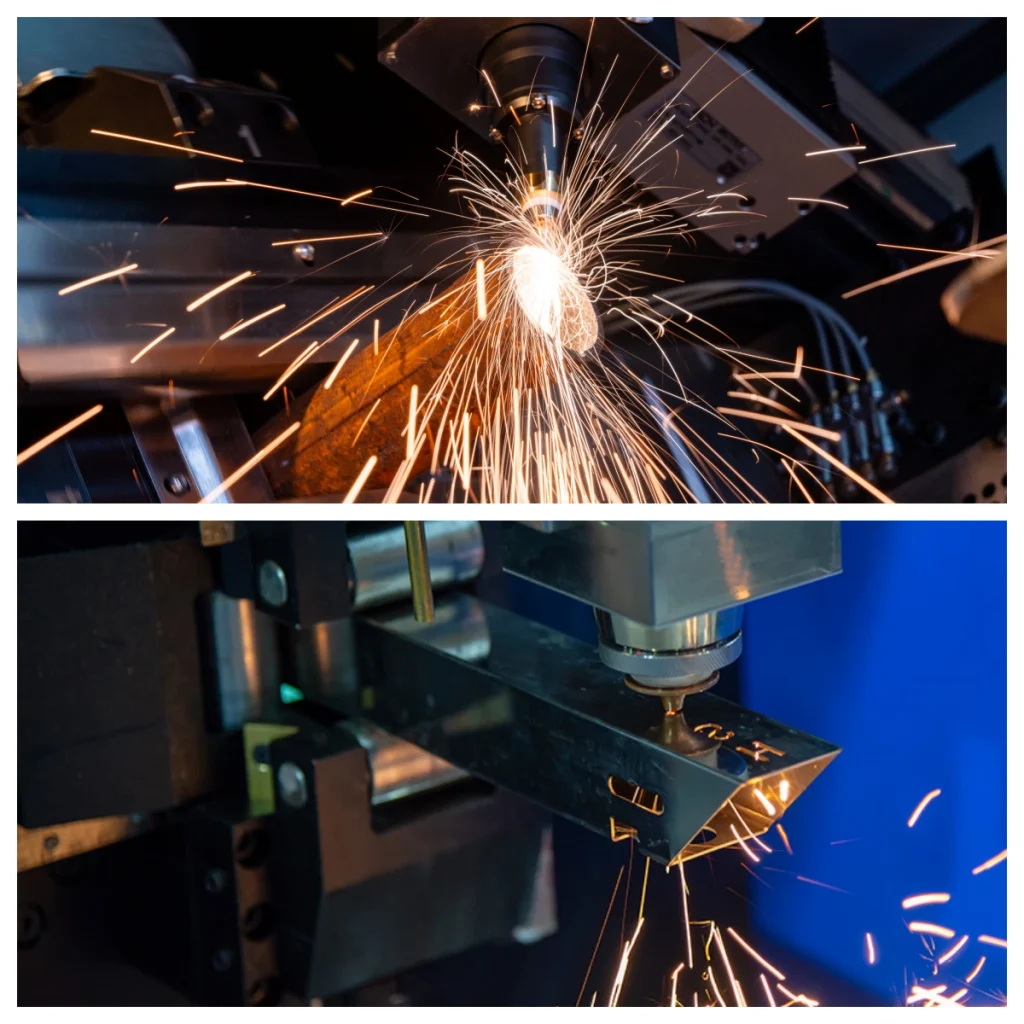
◑ Laser Cutting vs. Waterjet Cutting
Waterjet cutting is a cold process that doesn’t generate heat, making it suitable for materials sensitive to heat. Sin embargo, it is slower compared to laser cutting and produces larger kerfs, which can lead to more material waste.
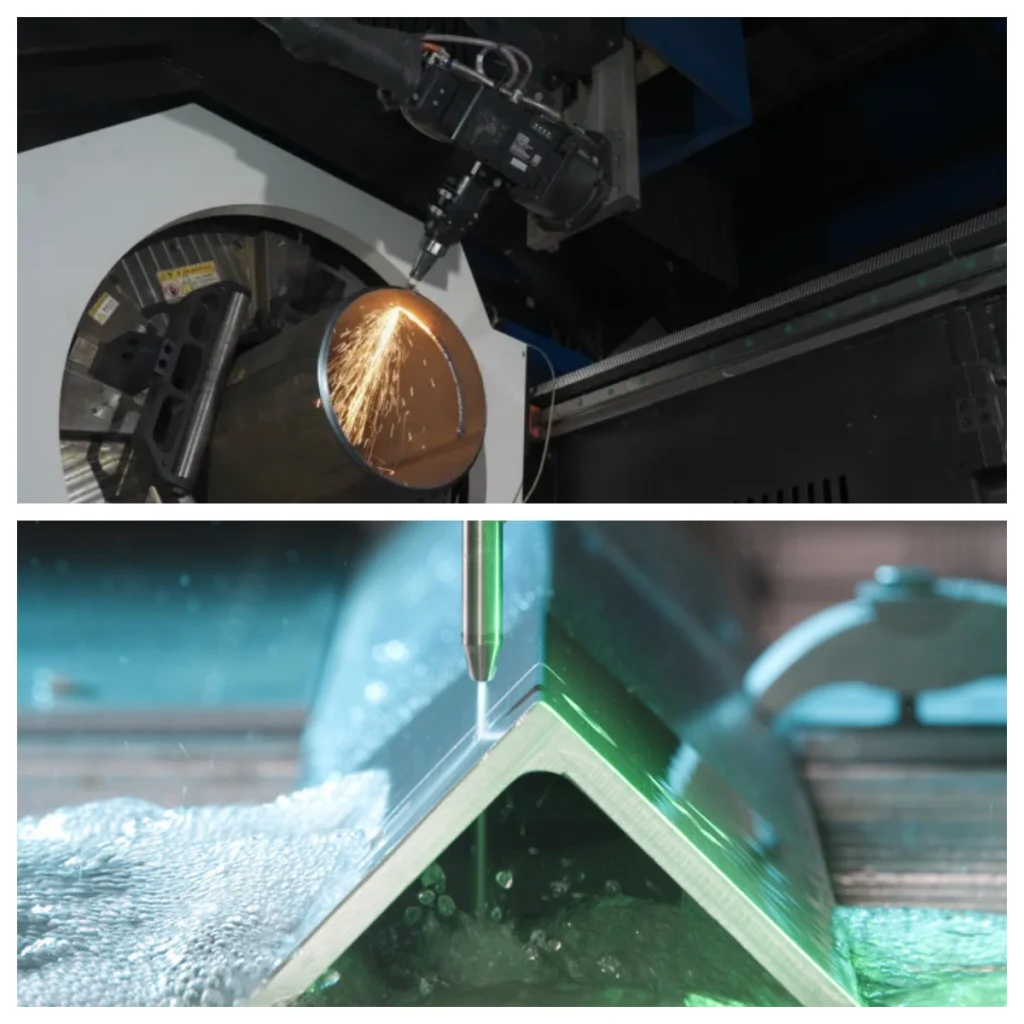
◑ Laser Cutting vs. Mechanical Cutting
Mechanical cutting involves physical contact between the tool and the material, which can lead to wear and tear over time. Laser cutting, por otro lado, eliminates tool wear and reduces the need for additional finishing steps, offering a cleaner, faster solution.
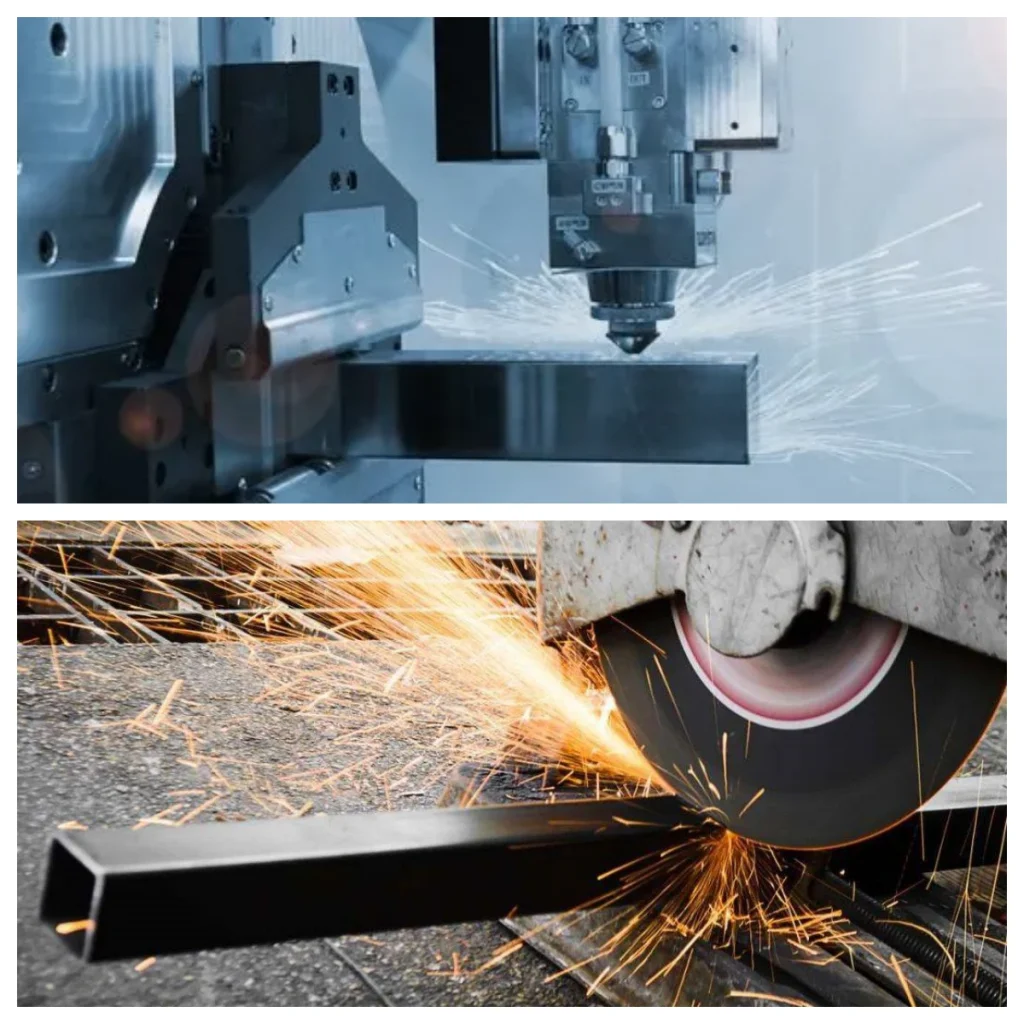
By adopting a CNC laser tube cutting machine, manufacturers can enhance their production processes, increase precision, and minimize waste. As industries continue to evolve, laser cutting technology will play a central role in the advancement of metal tube fabrication, making it an essential tool for modern manufacturing. Whether you’re cutting simple or complex shapes, investing in a CNC laser tube cutting machine ensures high-quality, cost-effective, and reliable results.
Historias destacadas
-
Laser Cutting Aluminum Tube: Techniques and Benefits Explained06 Sep 2025
-
Láser cortando aluminio con oxígeno: Aumento de la precisión y la eficiencia05 Sep 2025
-
Máquina de cortar láser eficiente para la hoja de latón: Mejora tu corte de precisión04 Sep 2025
-
Hoja de máquina de corte láser: La clave para la precisión y la eficiencia en la fabricación moderna02 Sep 2025
-
Corte láser de acero inoxidable con oxígeno: Revolución del proceso de corte31 Ago 2025
Categorías de productos
- Cortador láser de metales
- Máquina soldadora láser
- Máquina limpiadora láser
- Máquina marcadora láser
- Prensa plegadora