News
The Complete Guide to Choosing and Using a Laser Metal Cutting Machine
In the evolving world of manufacturing and metalworking, the laser metal cutting machine has become an indispensable tool for precision, speed, and versatility. Laser technology offers manufacturers and engineers the ability to cut through a variety of metals, including steel, aluminum, copper, and brass, with incredible accuracy. If you’re involved in any industry that requires metal fabrication, understanding the ins and outs of laser metal cutting machines is crucial.
This article will take you through everything you need to know about laser metal cutting machines, from how they work and their advantages to choosing the right machine for your specific needs. Whether you are new to laser cutting technology or looking to upgrade your equipment, this guide will provide the comprehensive information you need to make informed decisions.
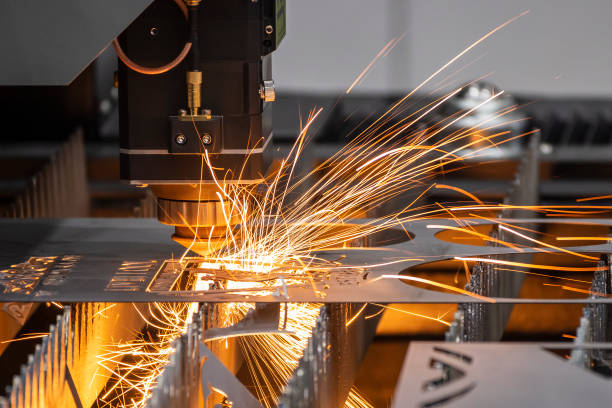
1.What is a Laser Metal Cutting Machine?
A laser metal cutting machine is a device that uses a focused laser beam to cut through various types of metal. Unlike traditional cutting tools, laser cutters can melt, burn, or vaporize metal using a concentrated beam of light, resulting in clean, precise cuts. Laser cutting technology works on the principles of thermal separation, where the laser melts or vaporizes the material, leaving a smooth edge with little to no burr.
Laser metal cutting machines are often controlled by CNC (computer numerical control) systems, ensuring high precision and repeatability in complex designs. They are widely used in industries such as automotive, aerospace, construction, and metal fabrication.
- How It Works
The cutting process of a laser metal cutting machine involves generating a high-powered laser beam that is directed at the metal surface. The energy from the laser heats the material to its melting point, and a gas, typically nitrogen or oxygen, blows away the molten metal. The entire process is contactless, meaning no physical tools touch the metal, which minimizes wear and tear and enhances the accuracy of the cut.
There are different types of laser cutting methods depending on the material and desired finish:
– Fusion cutting:
Uses an inert gas to blow molten metal away as the laser melts the surface.
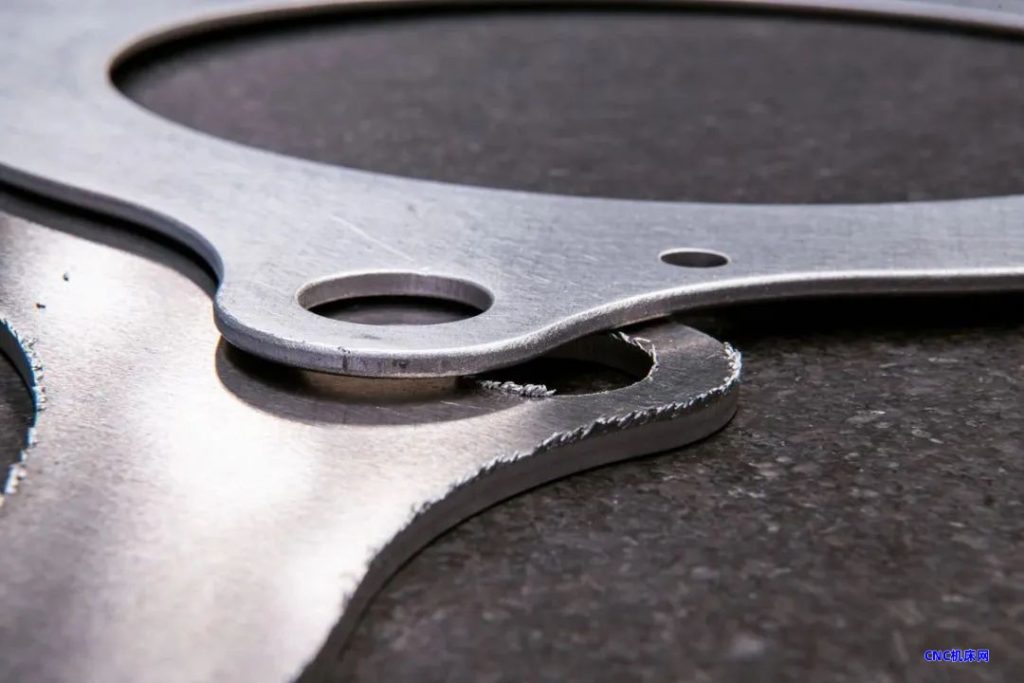
– Flame cutting:
Combines the laser’s heat with oxygen to ignite and melt the material, often used for thicker metals.
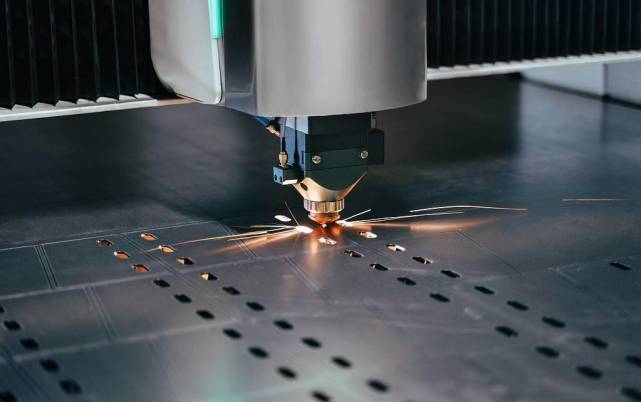
– Vaporization cutting:
The laser heats the material to the point of vaporization, leaving no molten residue behind.
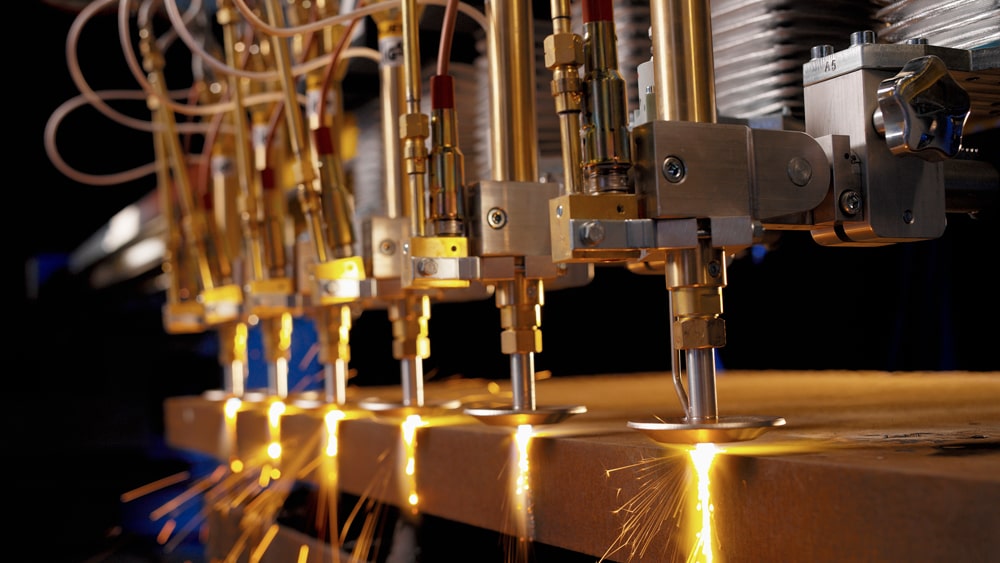
2.Benefits of Using a Laser Metal Cutting Machine
- Precision and Accuracy
One of the most significant advantages of laser metal cutting machines is their ability to produce precise and intricate cuts. The laser’s focused beam can achieve incredibly tight tolerances, making it possible to create designs that would be difficult or impossible with traditional cutting methods. Whether you are cutting delicate components for medical devices or thick sheets for automotive parts, laser cutting ensures consistent and accurate results.
- Speed and Efficiency
Laser metal cutting is a fast process compared to mechanical cutting techniques such as shearing or sawing. The speed at which the laser can cut through materials significantly reduces production times, especially for high-volume manufacturing operations. Additionally, because laser cutting is automated and controlled by CNC systems, it requires minimal human intervention, which further increases efficiency.
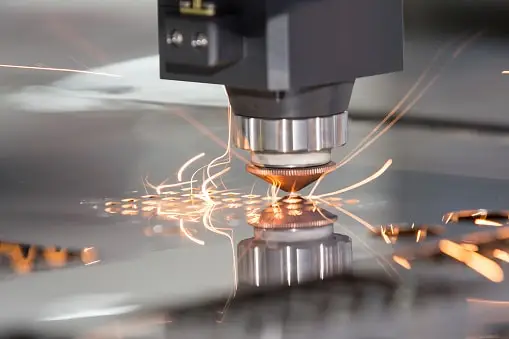
- Clean, Burr-Free Cuts
One of the standout benefits of using a laser metal cutting machine is the quality of the cut edge. Laser technology leaves a smooth finish with minimal to no burrs, eliminating the need for secondary finishing processes. This clean edge quality is particularly important in industries like aerospace or electronics, where surface smoothness and dimensional accuracy are critical.
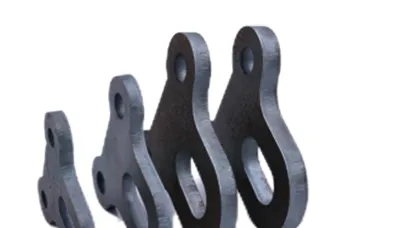
- Versatility Across Materials
Laser metal cutting machines are not limited to a specific type of metal. They can cut through a variety of metals, including:
– Stainless steel: Known for its strength and resistance to corrosion, stainless steel is widely used in industries such as construction and automotive. Laser cutters excel at cutting this material with minimal distortion.
– Aluminum: Due to its lightweight and reflective properties, aluminum can be challenging for some cutting methods, but laser cutting handles it with ease.
– Copper and brass: While these metals are known for their thermal conductivity, fiber lasers are particularly effective at cutting them due to their precision and speed.
- Cost-Effective in the Long Run
While the initial investment in a laser metal cutting machine can be substantial, the long-term cost savings are significant. The automation and precision of laser cutting reduce material waste and increase throughput, which lowers production costs over time. Additionally, because laser cutters are highly durable and require minimal maintenance, operational costs remain low.
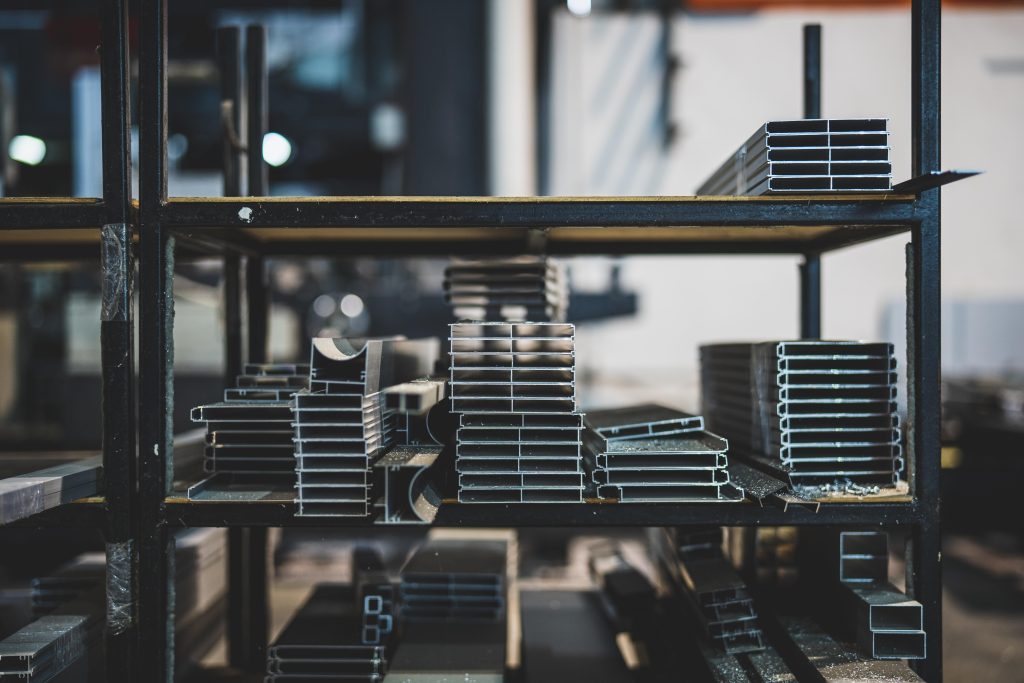
3.Types of Laser Metal Cutting Machines
When selecting a laser metal cutting machine, understanding the different types of laser technologies available is crucial. Each type has its advantages and is best suited to specific materials and applications.
Fiber lasers are the most advanced and energy-efficient option for cutting metals. These machines use a fiber-optic cable to transmit the laser beam, resulting in high-powered precision cutting. Fiber lasers are ideal for cutting reflective metals like aluminum and copper, which can be challenging for other laser types.
Advantages of fiber lasers include:
– High cutting speed, especially for thin metals.
– Low maintenance, as there are no moving parts or mirrors to adjust.
– Energy efficiency, as they convert more of the input energy into the laser beam compared to CO2 lasers.
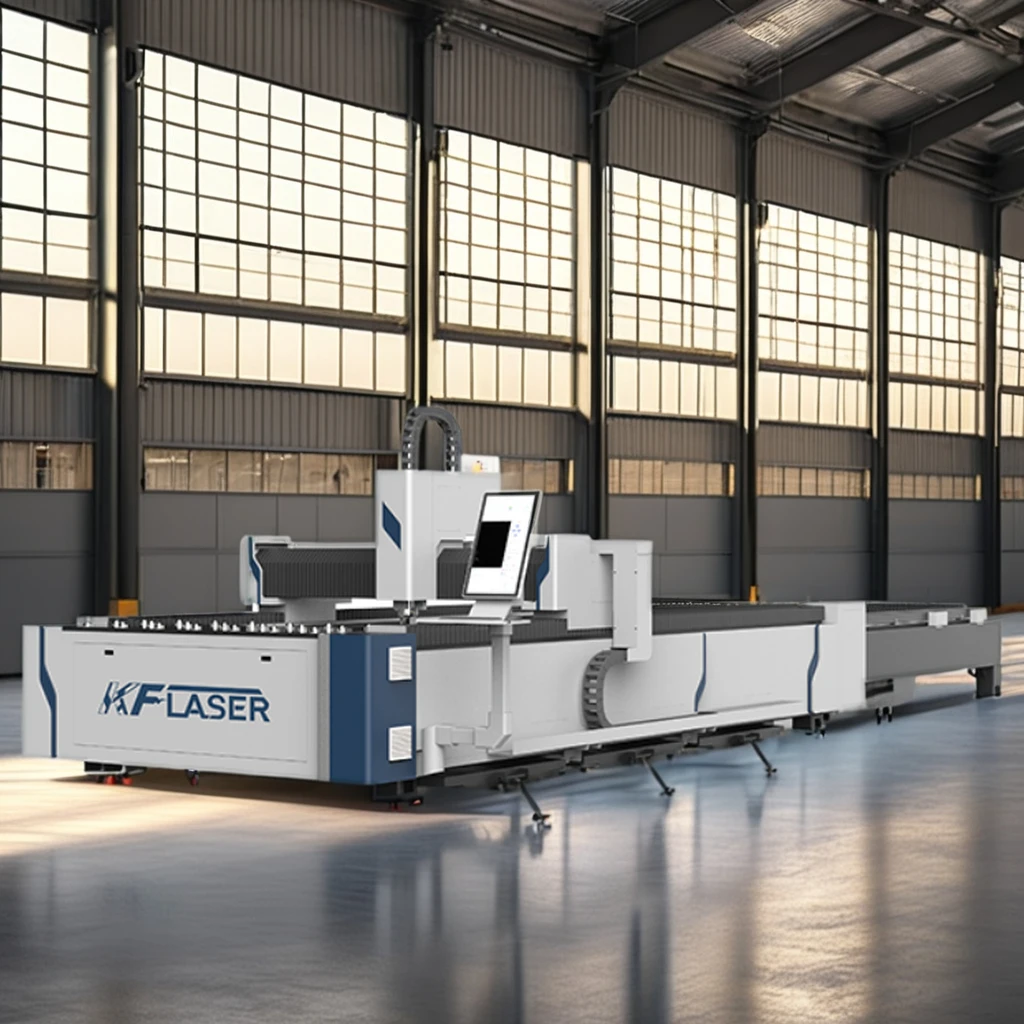
- CO2 Laser Cutting Machines
CO2 lasers are one of the most established types of laser metal cutting machines. They use a gas mixture (usually carbon dioxide) to generate the laser beam and are known for their versatility. CO2 lasers are effective at cutting both metals and non-metals, making them suitable for industries that require a wide range of material processing.
CO2 lasers are particularly good for cutting thicker materials, such as steel or aluminum, and offer a smooth edge finish. However, they require more maintenance compared to fiber lasers and are less efficient in terms of energy consumption.
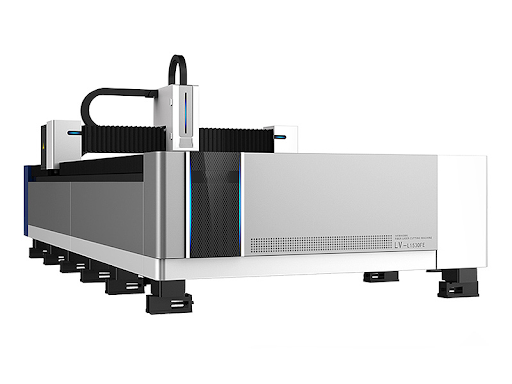
- Crystal Laser Cutting Machines
Crystal lasers, such as Nd:YAG and Nd:YVO lasers, are less common but are known for their high power and ability to cut through thick metals. These machines are often used in specialized applications where extreme precision is required. However, crystal lasers have a shorter lifespan than fiber or CO2 lasers and are generally more expensive to maintain.
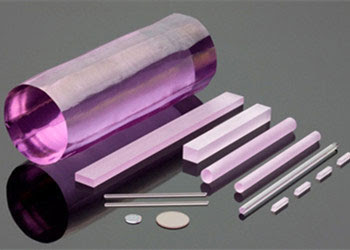
4. Factors to Consider When Choosing a Laser Metal Cutting Machine
Selecting the right laser metal cutting machine for your business depends on several key factors. Understanding these considerations will help you make an informed decision and ensure you get the best return on your investment.
- Material Type and Thickness
The type and thickness of the material you plan to cut will play a significant role in determining which laser machine is right for you. Fiber lasers are ideal for cutting reflective metals and thinner sheets, while CO2 lasers are better suited for cutting thicker metals and non-metals. Consider the specific materials you work with and choose a machine that offers optimal cutting performance for those materials.

- Cutting Speed and Power
Laser cutting machines come with varying power levels, typically measured in kilowatts (kW). The higher the power, the faster and more efficiently the machine can cut through thick materials. However, higher power levels also mean increased energy consumption and potentially higher operational costs. Choose a machine with the right balance of power and speed for your production needs.
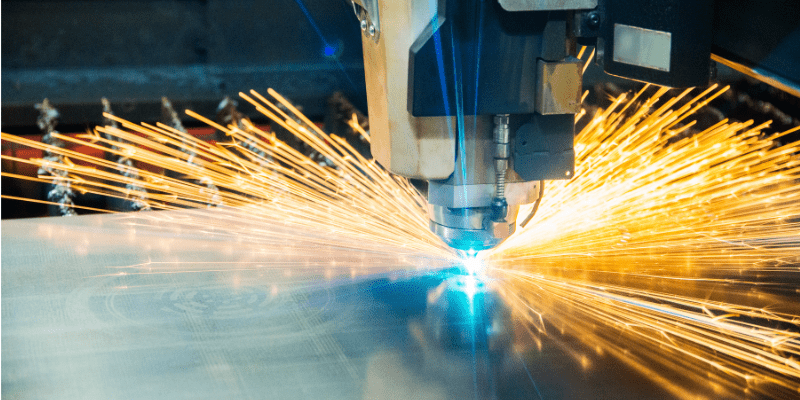
- Work Area Size
The size of the work area on a laser metal cutting machine is another critical factor, especially if you’re working with large sheets of metal. Ensure that the machine you select has a bed size that can accommodate your largest materials, and consider whether you will need additional space for handling or storage.
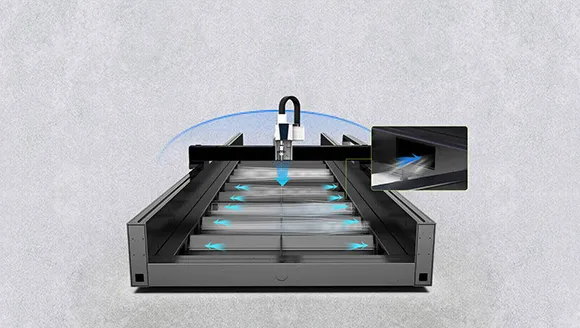
- Maintenance Requirements
Different types of laser cutting machines require different levels of maintenance. Fiber lasers, for example, are known for their low maintenance requirements due to their lack of moving parts. CO2 lasers, on the other hand, may require more frequent adjustments and maintenance due to the mirrors and gas involved in generating the laser beam. Assess the maintenance needs of the machine before making a purchase to ensure that it fits into your production schedule.
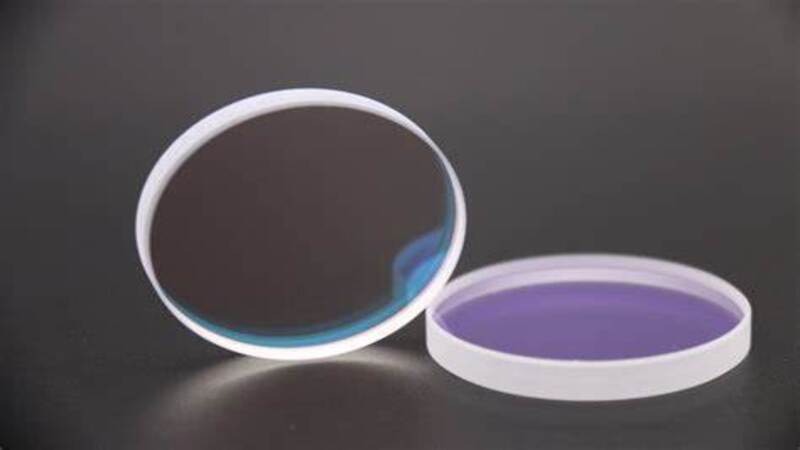
- Automation and Software Integration
Many modern laser metal cutting machines come equipped with automation features, such as automatic loading and unloading systems. These features can significantly increase productivity by reducing the need for manual intervention. Additionally, consider whether the machine integrates with your existing software, such as CAD or CAM systems, to ensure a seamless workflow.
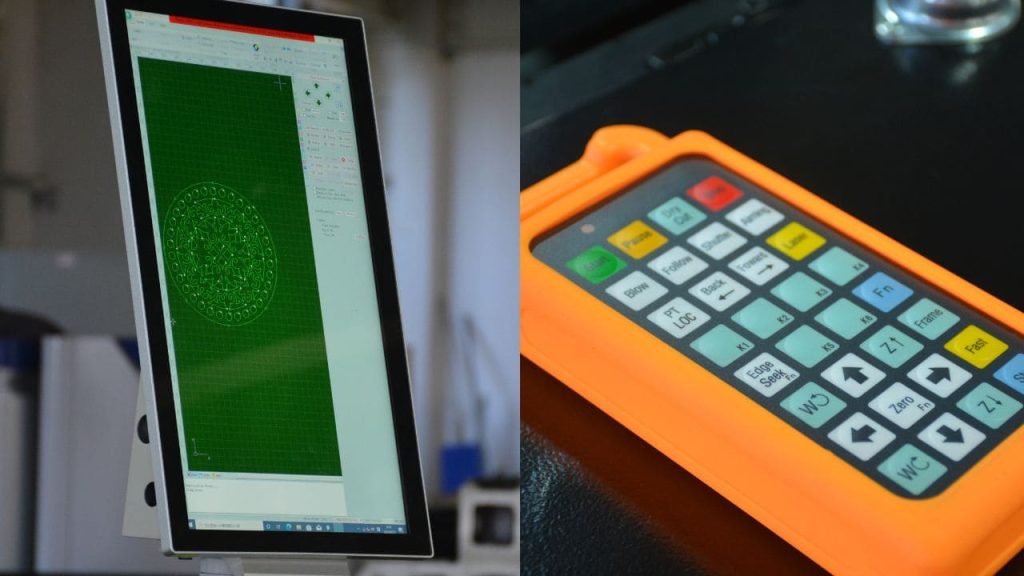
- Safety Features
Safety is always a priority when working with high-powered laser machines. Look for machines that come with built-in safety features, such as protective enclosures, emergency stop buttons, and ventilation systems to handle fumes and gases produced during cutting.
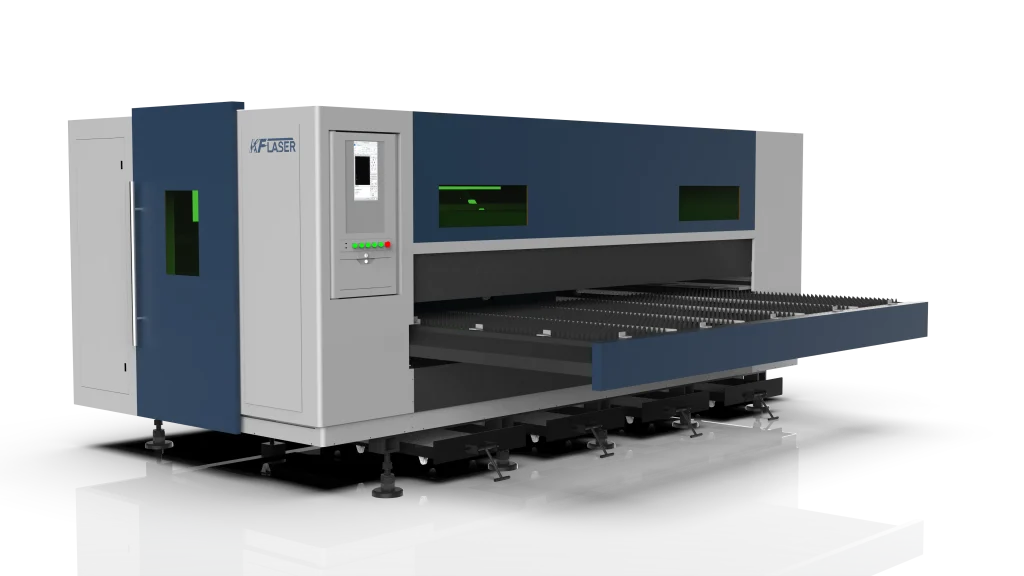
5.Best Practices for Laser Metal Cutting
To get the most out of your laser metal cutting machine, it’s important to follow best practices that ensure optimal performance and longevity of the machine.
- Optimize Cutting Parameters
The key to achieving the best results with laser cutting is to fine-tune the machine’s settings to match the material you’re working with. Adjust parameters like laser power, cutting speed, and gas pressure based on the thickness and type of metal. For instance, cutting thicker materials may require higher laser power and slower speeds to ensure a clean cut.
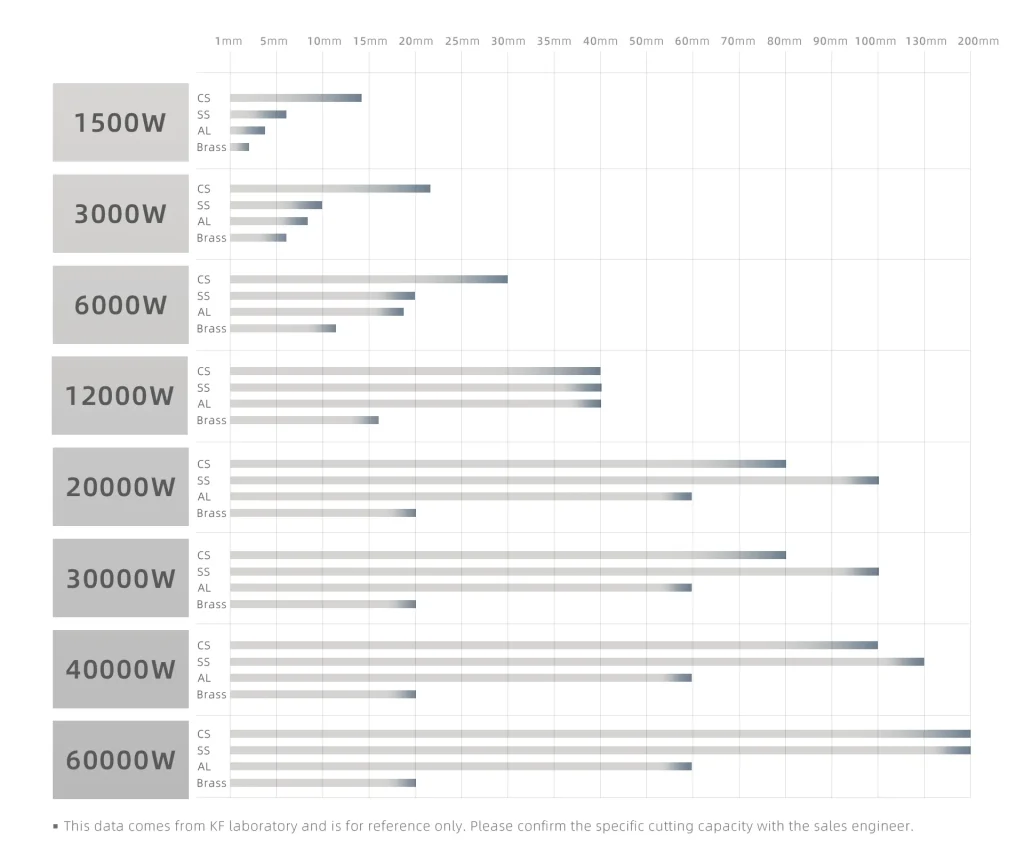
- Regular Maintenance and Cleaning
Even though laser metal cutting machines require less maintenance than traditional tools, regular upkeep is still essential. Clean the lenses and mirrors regularly to prevent debris from affecting the beam’s focus. Check for wear and tear on consumable parts like nozzles, and replace them as needed to maintain cutting quality.
- Use the Right Assist Gas
Assist gases like oxygen and nitrogen are used in laser cutting to help blow away molten metal and prevent oxidation. For materials like aluminum and
stainless steel, nitrogen is often preferred because it produces a cleaner edge. For carbon steel, oxygen can increase cutting speed but may leave slight oxidation on the cut edges.
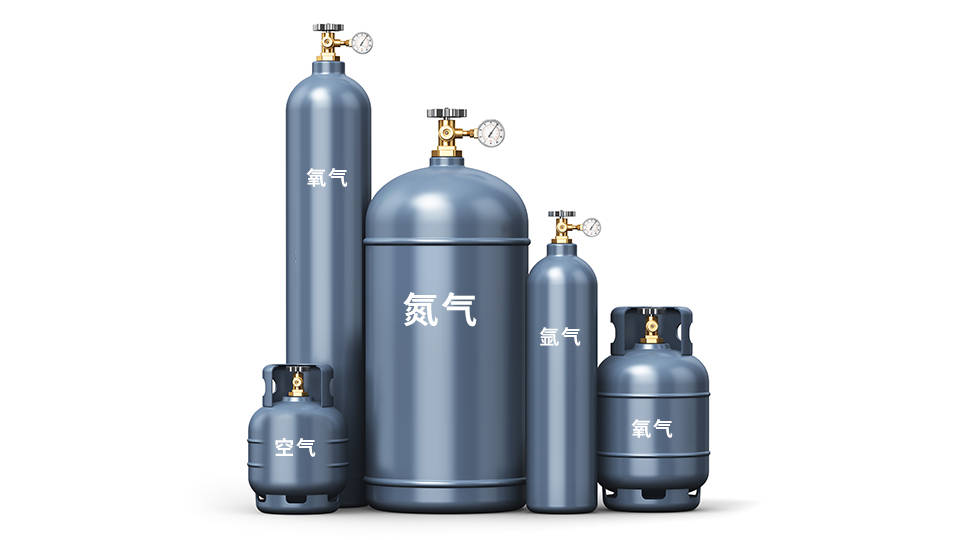
- Monitor and Adjust Focus
The laser’s focal point is crucial for achieving clean cuts. Regularly check and adjust the focus to ensure that the laser is concentrated precisely on the material’s surface. Proper focus minimizes heat distortion and ensures a smooth, burr-free finish.
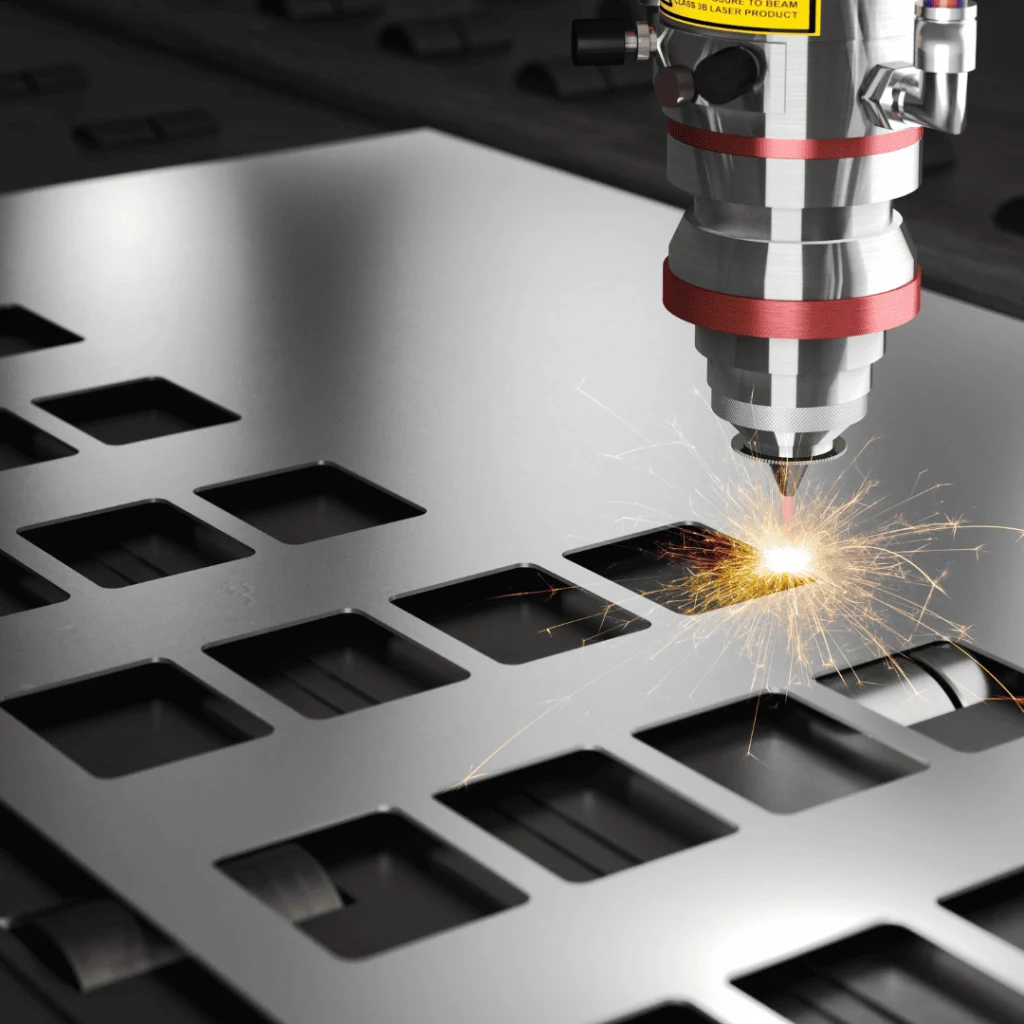
6. Applications of Laser Metal Cutting Machines
Laser metal cutting machines are used across a wide range of industries due to their versatility and precision. Some of the most common applications include:
- Automotive Industry
In the automotive sector, laser cutting is used to manufacture parts such as body panels, exhaust systems, and engine components. The high precision of laser cutting ensures that these parts fit together perfectly, reducing the need for further adjustments during assembly.
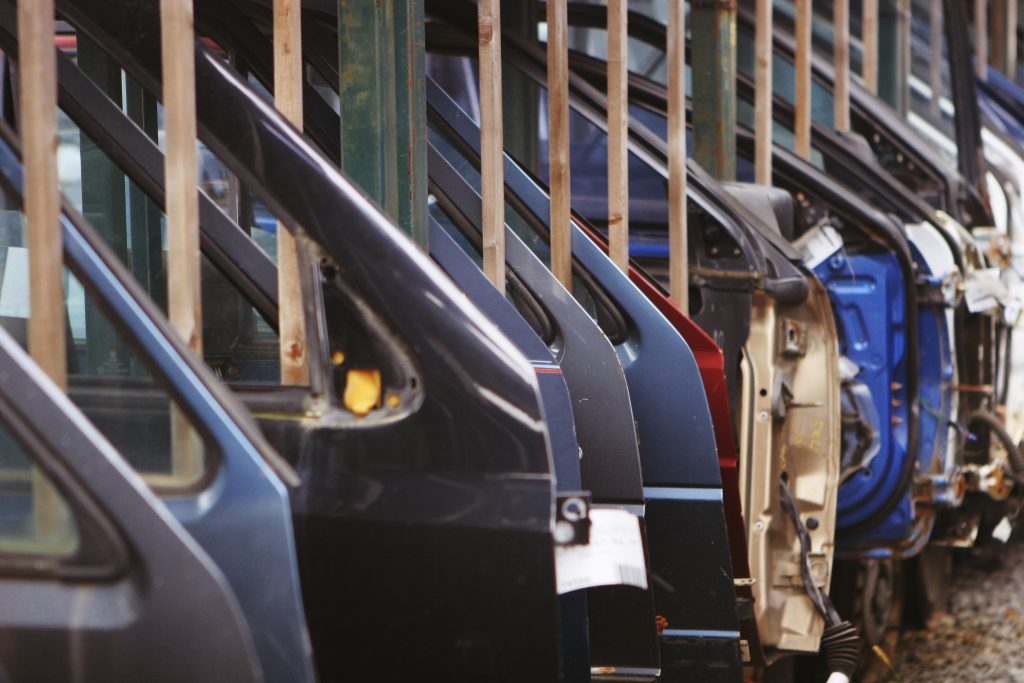
- Aerospace Industry
The aerospace industry requires parts that are lightweight and extremely durable. Laser metal cutting machines are used to cut high-performance alloys used in aircraft and spacecraft, where precision and strength are critical.
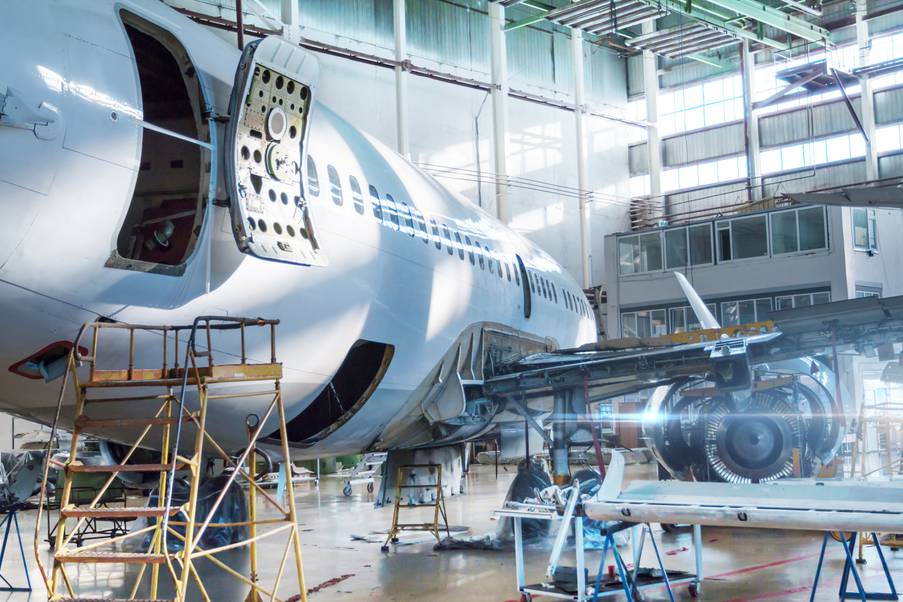
- Medical Equipment
In the medical field, laser cutting is used to manufacture surgical instruments, implants, and other components that require high precision. The smooth, burr-free cuts produced by lasers ensure that these tools meet stringent hygiene and safety standards.
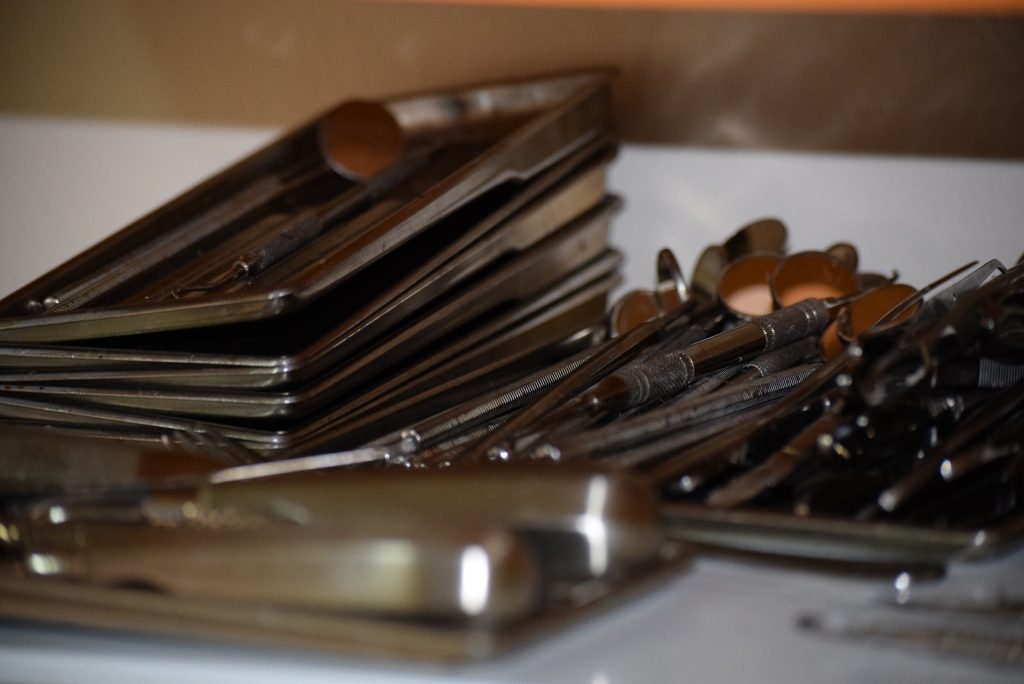
- Architectural and Decorative Uses
Laser-cut metal panels are commonly used in architectural designs, from building facades to interior decorations. The ability of laser cutting machines to create intricate patterns makes them popular for decorative applications in homes, offices, and public spaces.
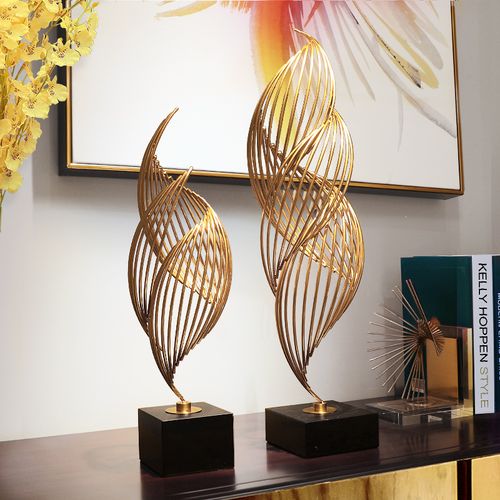
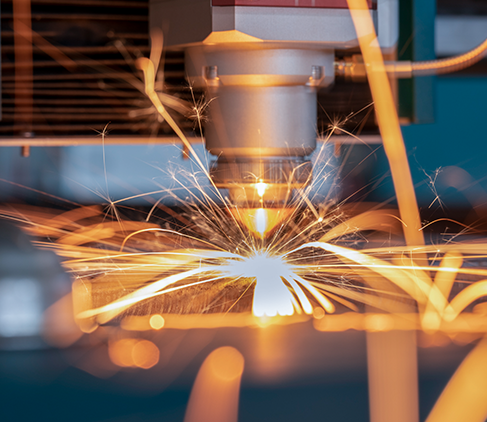
7.The Future of Laser Metal Cutting Machines
As technology continues to evolve, laser metal cutting machines are becoming more efficient, versatile, and accessible. Advances in automation, AI, and real-time monitoring are set to improve the speed and accuracy of laser cutting even further. The shift towards more energy-efficient machines is also likely to reduce the environmental impact of manufacturing processes.
For businesses looking to stay competitive, investing in a laser metal cutting machine represents not just a technological upgrade but a strategic move toward increasing productivity and reducing operational costs.
Top Stories
-
Laser Cutting Aluminum Tube: Techniques and Benefits Explained06 Sep 2025
-
Laser Cutting Aluminum with Oxygen: Boosting Precision and Efficiency05 Sep 2025
-
Efficient Laser Cutting Machine for Brass Sheet: Enhance Your Precision Cutting04 Sep 2025
-
Laser Cutting Machine Sheet: The Key to Precision and Efficiency in Modern Manufacturing02 Sep 2025
-
Laser Cutting Stainless Steel with Oxygen: Revolutionizing the Cutting Process31 Aug 2025
Product Categories
- Metal Laser Cutter
- Laser Welder Machine
- Laser Cleaner Machine
- Laser Marker Machine
- Press Brake Machine